Metal Bonding Glue: Choose the best adhesive for bonding metal
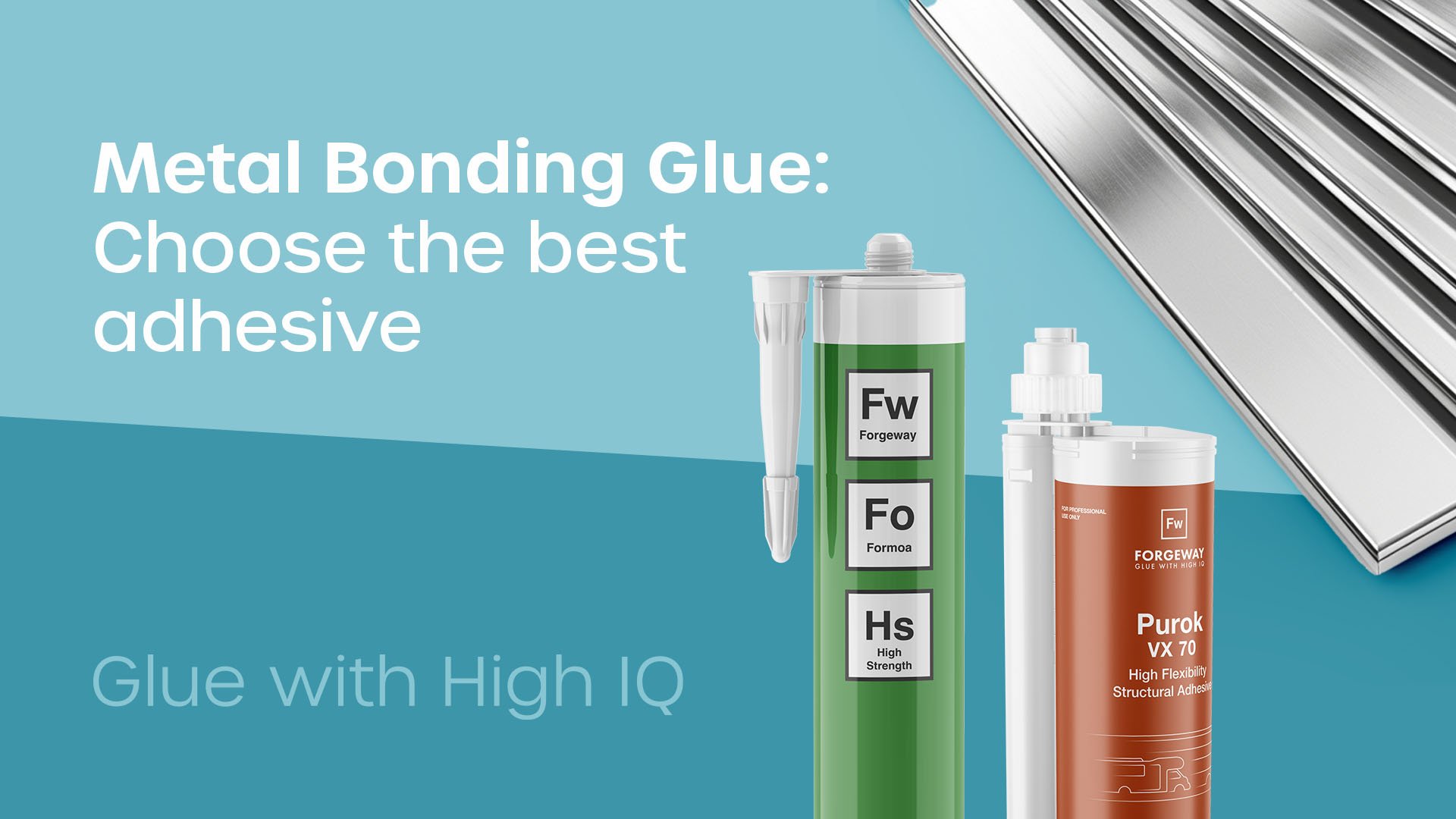
You have decided that an adhesive is the best joining method for your metal joining application. Now, you need to decide which adhesive is going to be best for that metal bonding application.
Here at Forgeway, we manufacture industrial adhesives. We know how difficult it can be to find the right metal bonding adhesive. When customers ask us for the ‘best’ metal bonding glue, we try and stay away from the ‘it depends’ answer.
However, it does ‘depend’. It depends on what that application requires from the adhesive. So that’s why we will help you through the dependencies.
By the end of this article, you will be aware of the dependencies and factors that you should consider when choosing the right adhesive. You will become educated on how to choose the right metal bonding glue for your application.
What are you bonding the metal to?
Before we get started with the different adhesive choices, you need to know what you are bonding. The substrates you are bonding will determine what adhesive you can use.
There are multiple different substrate combinations. However, the two main substrate combinations to look out for are:
- Metal to metal
- Metal to plastic
Watch the video below to learn how you can find out the ‘bondability’ of your substrate.
What to look out for when bonding metal to metal
Most metals will not need anything more than light abrasion to ensure a strong bond. However, there are a few different types of metals which will need severe surface preparation or a specialist adhesive.
When choosing a metal bonding glue, the most problematic metal to look out for is galvanised steel. You will have to ensure the adhesive can bond to your galvanised steel before you progress to the next steps. Otherwise, you may have to look at using surface preparation methods.
The other metals to look out for are powder-coated metals, e-coated metals, and other coated metals can cause problems with bonding.
You may find that you need to use a primer or heavily abrade the surface before bonding to ensure a strong bond. However, checking whether the surface is problematic or not will help you narrow down the metal bonding adhesive options.
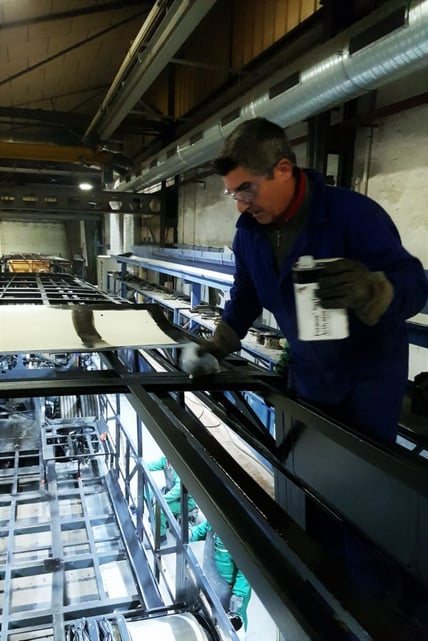
What to look out for when bonding metal to plastic
Some plastics can be very difficult to bond to. Any surface that has a surface energy lower than 37 mJ/m² would qualify as low surface energy. Surfaces with a low surface energy will be very difficult to bond to.
Some plastics have a very low surface energy, causing problems with adhesion. Polypropylene is one of the most popular plastics used in the manufacturing industry. However, polypropylene has a low surface energy.
This means you will struggle to bond metal to polypropylene without using a specialist surface preparation technique or a specialist adhesive.
So, if you are bonding metal to plastic, make sure the surface energy of the plastic isn’t low enough to cause bonding problems.
How to choose the best metal bonding glue
Once you have confirmed the substrates you are bonding, it’s now much easier to choose the right adhesive. If you are unsure of the substrates you are bonding, the video above will help you understand whether your substrate is going to cause bonding problems.
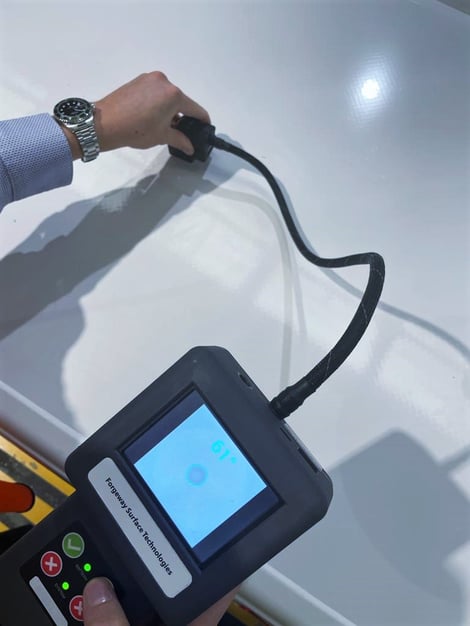
But firstly, if you do find your substrate is likely to cause problems with bonding, you need to establish whether you want to use a specialist adhesive or use an appropriate surface preparation method.
Once you decide between the two, you can move on to the next step of the process. Now it’s time to decide what you want from the adhesive.
However, if you have found that the substrate isn’t going to cause problems, it’s now time to decide what you want from your adhesive.
How much strength do you need from your adhesive
A lot of the time, companies put too much emphasis on the strength needed from an adhesive. Whilst strength is one of the most important characteristics of an adhesive, we would argue that flexibility is more important. The truth is, they are just as important as each other.
However, you will need to determine how much strength your adhesive needs. Will you need a high-strength adhesive (above 15 MPa)? Or is that much strength not actually required?
It will come down to the weight of the substrate you are bonding, and the bond area available to you. The greater the weight and smaller the bond area, the more strength you will need from your adhesive.
For example, a plastic sandwich panel with a bond area of 30mm will not need as high strength adhesive as a heavy metal frame with a bond area of 10mm.
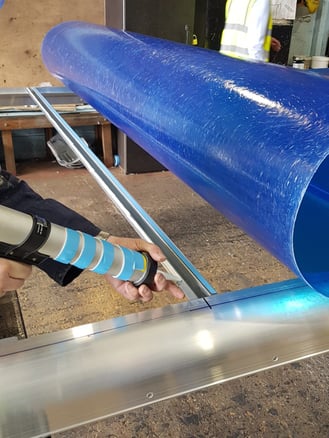
Whilst it’s easy to say you need the strongest adhesive possible, ask yourself, “do I need high strength or high durability?” The two phrases are very different but are very often confused. You will need to understand this before choosing a metal bonding glue.
How much durability do you need from the bond?
Durability basically means that adhesive is going to withstand any knocks and blows that are thrown at it. If the adhesive isn’t able to withstand vibrations (dynamic load) or weathering conditions, then it doesn’t matter how strong it is. That strength can only last so long before the bond fails.
This part of the adhesive selection process is difficult. The difficulty comes with knowing how you can be sure that the adhesive is going to be durable enough.
If you are unsure how you can go from here, we suggest you read our article on how to choose the right adhesive. It will walk you through the different steps we take to ensure your adhesive choice will be durable enough.
However, if you are confident you know what the adhesive will need to withstand, you can move on to the next step. It’s now time to look at the different types of adhesives.
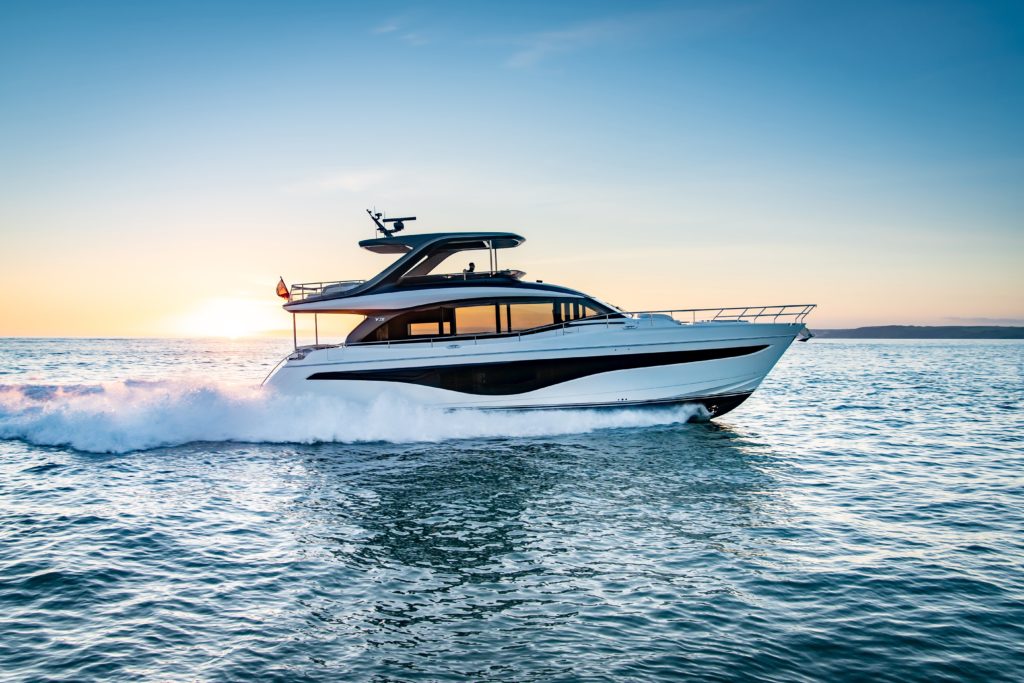
The different types of metal bonding adhesives
Whilst there are thousands of different metal bonding adhesives, you will likely find that they will fit into one of four chemistry types.
Epoxy adhesives
Epoxy adhesives will have the highest strength and are extremely versatile. They also tend to have good chemical and heat resistance making them durable. However, they are often slow curing and will require surface preparation to ensure a strong bond.
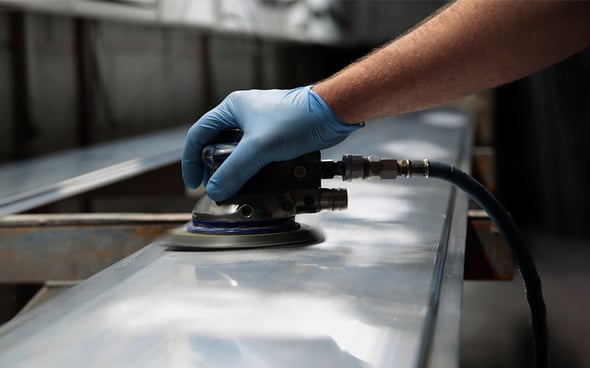
Acrylic adhesives
Acrylic adhesives require minimal surface preparation. They can achieve very fast cure speeds and will also achieve very high strengths. However, they do have a distinct odour making them unpleasant to work with.
Polyurethane adhesives
Polyurethane adhesives are also highly versatile (like epoxies). They tend to be highly flexible if the bond is likely to experience significant movement. However, polyurethane adhesives will also require extensive surface preparation and contain harmful substances.
MS polymer adhesives
MS polymer adhesives are the most flexible adhesives on this list. They are fully primerless meaning you don’t need to prime or abrade the surface before bonding. But, MS polymers are not able to achieve the same strengths as the other adhesives. They should only be used for semi-structural bonding.
Yes, you can find other types of metal bonding adhesives. However, if you are looking for industrial metal bonding, these four are what you want to focus on.
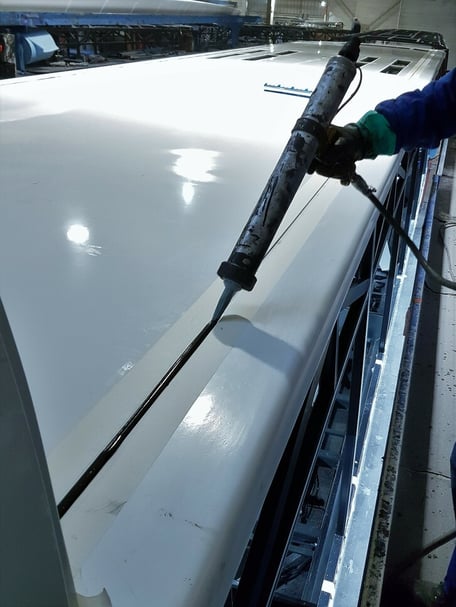
Choosing the best metal bonding adhesive
Now you know what to consider, and the different types of metal bonding adhesives, it’s time to explore which option you think could be best for you. But making that decision still isn’t very easy
Here at Forgeway, we have been manufacturing industrial adhesives for over 25 years. We know that the ‘best’ choice could depend on so many different factors.
That’s why we have attempted to break it down in this article. There are plenty of things you must consider before choosing the ‘best’ metal bonding adhesive.
But most of the time it will come down to whether strength or flexibility is more important for your application. You should make this decision before looking at adhesive products. Read more about this topic by clicking the button below.
However, there are plenty of other things you need to consider too. We recommend you watch the video below to get an idea of what you need to consider when changing adhesive.
Alternatively, you may have read enough and want to speak to an adhesive expert. Reach out and a member of our team will be happy to help.
Thomas is the Content Manager here at Forgeway. Thomas' job is to translate the technical jargon from the ivory tower of academia into easy-to-read content that everyone can understand. Forgeway's mission is to answer every question our customers and prospective clients ask, or are apprehensive to ask.