The Impact of 2023 Isocyanate Regulations on Polyurethane Adhesives
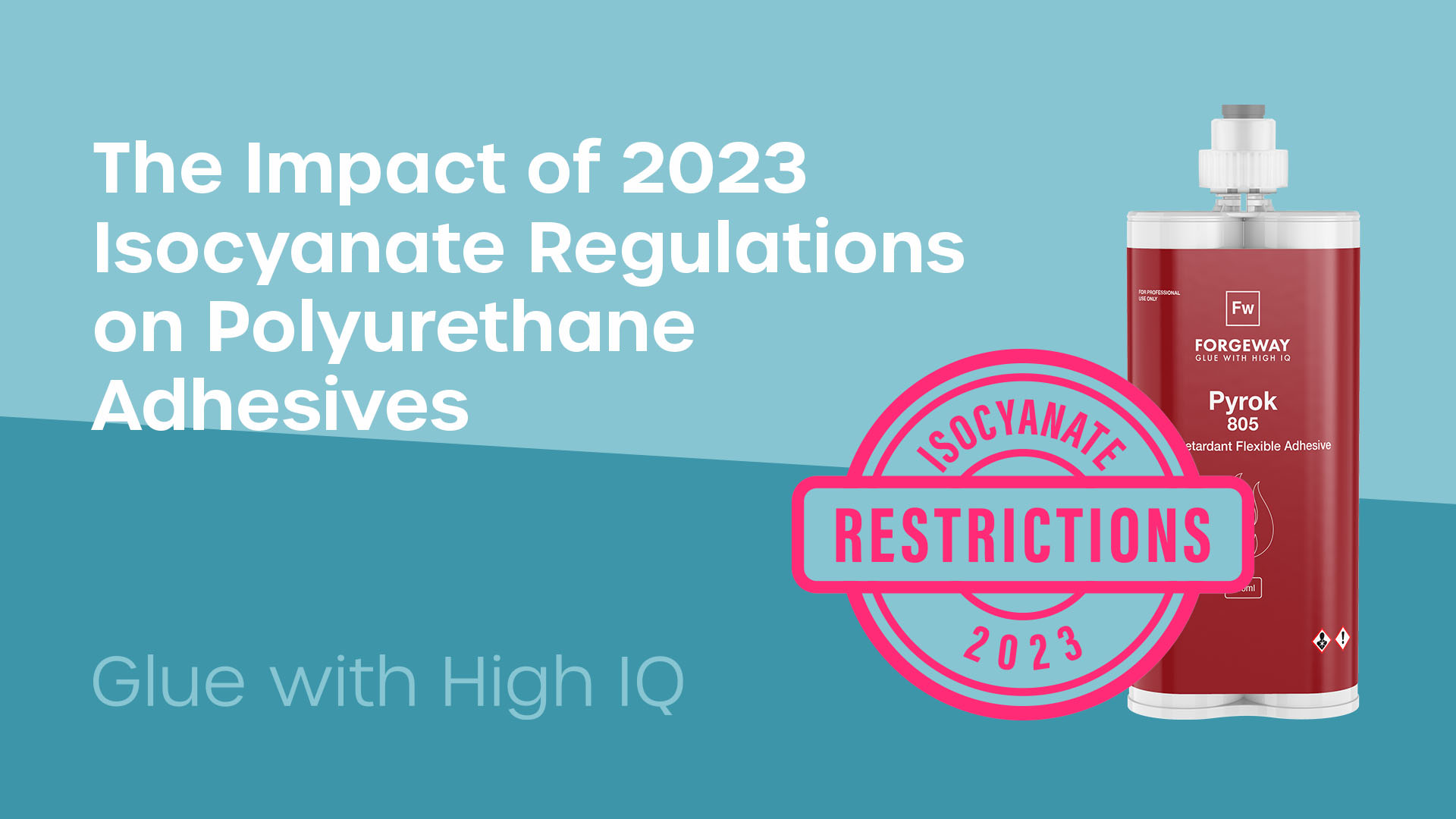
You have likely already heard about the restrictions that came into force about the use of products containing diisocyanates.
Now you’re looking for more information about these restrictions, whether they affect your organisation, and if so, what you can do about them.
As industrial adhesive manufacturers, we work with companies that use products containing diisocyantes. We understand it can be difficult to know what to do next.
This article will give you the information you need to understand the restrictions. Then we will guide you on the options available to you now that they have come into force.
By the end of the article, you will be better prepared to face the upcoming diisocyanate restrictions.
However, you can watch our video below explaining these regulations if you would prefer. (This video was filmed before the restrictions came into force in August 2023)
What are diisocyanates?
Diisocyanates are a key ingredient in the production of polyurethane foams, coatings, adhesives, and other products. They are highly reactive.
The reaction of an isocyanate and a polyol is what forms a diisocyanate. Diisocyantes can come in the form of a liquid or a solid.
A common diisocyanate is methylene diphenyl diisocyanate (MDI), which you would typically find in polyurethane coatings and adhesives.
Diisocyanates are highly reactive and can cause skin and respiratory irritation and allergies in some individuals, especially those who are frequently exposed to them in an occupational setting.
What are the 2023 diisocyanate safety regulations?
Before we explain the regulations, we should explain why they are coming into force. The respiratory sensitization of diisocyanates can lead to occupational asthma for workers using products containing the chemical.
In fact, diisocyanates caused over 5000 cases of new occupational diseases in Europe last year. Although it’s estimated to be a much greater number than this.
To think one chemical is causing this much harm is staggering.
So, the REACH committee voted in favour of the European Commission’s proposal for a REACH restriction on diisocyanates in early 2020.
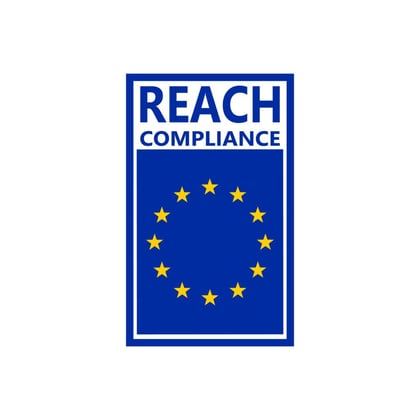
But what do these restrictions actually state?
The restrictions say that diisocyanates shall not be used on their own, or in mixtures for industrial and professional use after August 24, 2023, unless:
- The concentration of diisocyanates is less than 0.1% by weight
- The employer ensures users have completed training on the safe use of diisocyanates before using products containing more than 0.1% of the chemical
The training mentioned in the document must be conducted by an expert on occupational safety and health. The trainer must have competence acquired by relevant training. (Training is usually online).
Any training courses are required to cover defined points set out by REACH. If you want to know what those points are, sections four and five of the Annex detail everything the training must contain.
In summary, it just means that this training must be conclusive and from a trusted source.
What can you do to comply with the diisocyanate safety requirements?
So now you know what the restrictions are all about, it’s time to understand what you can actually do about it. You may be stuck about which way to go now.
We assess the two best options available to you. However a quick disclaimer in here that as industrial adhesive manufacturers, we will mainly be talking about polyurethane adhesives.
But the options apply to all polyurethane products.
Option 1: Ensure all operatives receive the correct training
This option is self-explanatory. You are happy with the polyurethane adhesive you are using and you don’t want to change.
However, as you need to use approved training, you will need to know where you can find that training.
We’ve found a helpful resource which gives you all the information you need to assess which training is right for your organisation.
But there are some advantages and disadvantages to this method.
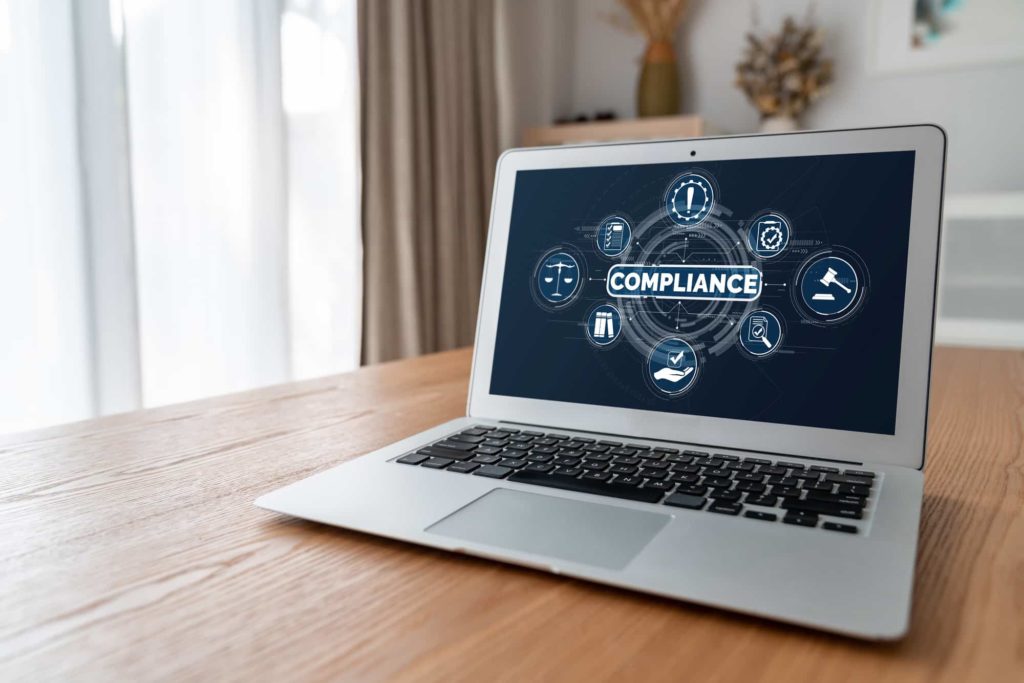
Advantages of providing training:
It will ensure you can carry on using the existing product. As you will likely have experienced, changing adhesive products isn’t easy. Internal resistance to change makes switching products a challenge.
By providing training, you will avoid the process of switching to a new product.
Training is also a more cost-effective option.
Changing to a new product could end up costing more money upfront. However, you will likely be able to find cheaper alternatives to polyurethane products. So this initial cost will help you save money in the long term.
Disadvantages of providing training:
Training, however, is by far a perfect solution. Firstly, you have to find a training course that will pass the criteria set out in the restrictions.
Then, you will have to ensure all operatives using polyurethane products successfully complete the course.
This can be challenging when there is a high staff turnover or you are using temporary employees.
And that’s not all. The polyurethane product you’re using might not even be the best adhesive for the job.
Advancements in adhesive technologies over recent years have led to newer structural adhesives that can exceed the performance of polyurethane systems.
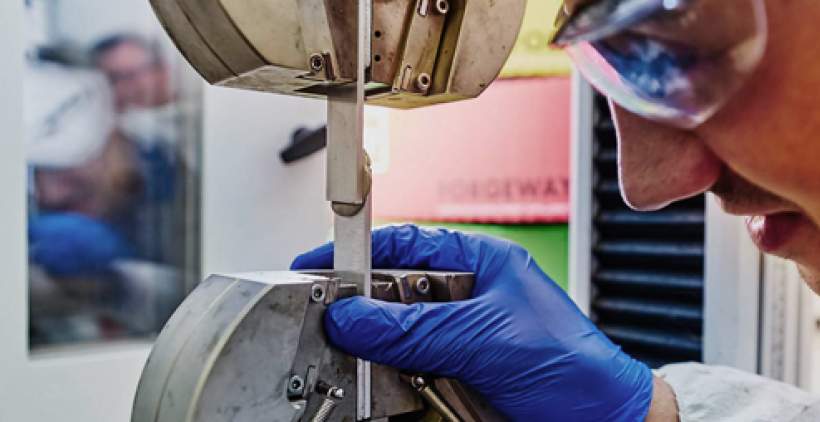
Option 2: Look at alternatives to polyurethane products
The second option available is to move away from using a polyurethane system. This will involve finding an alternative adhesive that matches the requirements but doesn’t contain more than 0.1% of diisocyanates.
Again, there are advantages and disadvantages to this option.
Advantages of changing adhesives:
The main advantage to changing adhesives is you remove the need to train your staff on how to handle diisocyanates.
You will also be able to look at improving your processes. Some consider structural polyurethane adhesives to be outdated. There are newer adhesive technologies available with increased performance.
A lot of the time, companies are only using polyurethane adhesives because they have been specified and used for years.
When they look at changing away from polyurethane adhesives, companies find they can vastly improve their production processes with newer and improved adhesives.
Methyl methacrylate adhesives and epoxy adhesives are the two most popular structural adhesive types. However, you will want to make sure you know what you are looking for when changing structural adhesive.
Disadvantages of changing adhesives:
Nonetheless switching adhesives is by no means easy. The change process is often difficult due to resistance internally.
The change process can also take a long time. Usually 3-6 months which requires a lot of effort and commitment towards finding a suitable alternative.
You will also have to ensure that any new products match the required performance for that application.
Stick or twist? Should you continue using polyurethane products in 2023?
So now you know about the restrictions and the options available to you, it’s time to decide what your organisation should do. However, we understand it’s not an easy decision. Both options will require work to ensure you are compliant with the restrictions.
However, as industrial adhesive manufacturers, we have helped many companies find the right solution for them. We are here to help you decide.
It often comes down to the two options we have shown above.
If you are happy with the polyurethane product and you don’t have a large number of staff, we recommend you look at polyurethane training. You just need to ensure the operatives receive training.
However, if you have a large number of staff (over 100 operatives) and you have been using polyurethane adhesives for years, we recommend you look at alternative adhesives products.
Either way, we suggest you look at alternative products as there may be an adhesive solution that can vastly improve your processes.
We have witnessed multiple companies reduce work in progress, increase throughput and ultimately increase profit just by moving away from polyurethane adhesives.
If you want the help of an adhesive expert to take a look at the requirements of your organisation, reach out and we will be happy to help.
If you want to research the topic yourself, take a look at our blog assessing alternative adhesives to polyurethane products.
Thomas is the Content Manager here at Forgeway. Thomas' job is to translate the technical jargon from the ivory tower of academia into easy-to-read content that everyone can understand. Forgeway's mission is to answer every question our customers and prospective clients ask, or are apprehensive to ask.
Topics: