What is environmental stress cracking? And how you can prevent it
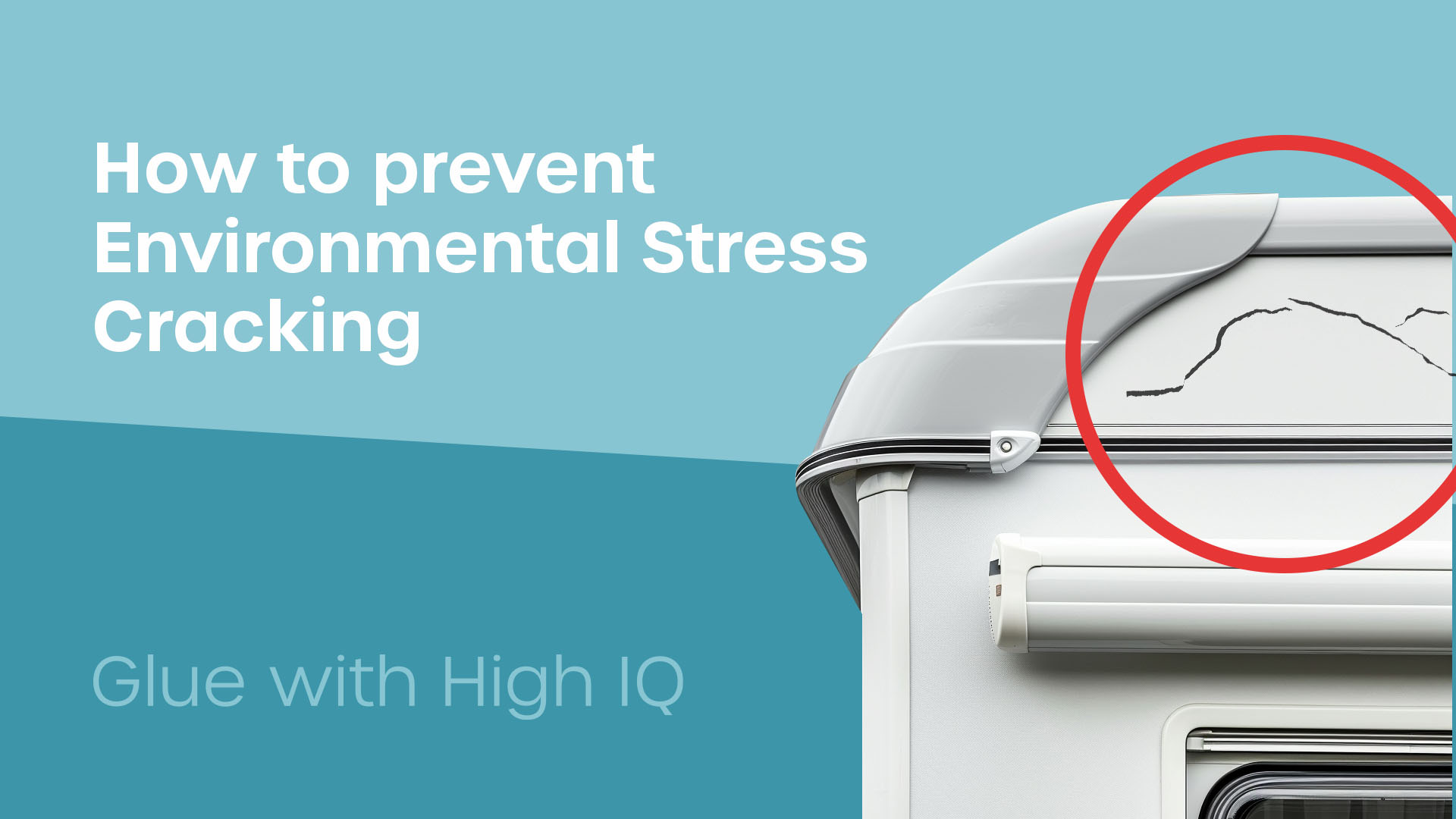
If you are bonding plastic to a structure that will be under stress, you will likely have considered the threat of environmental stress cracking (ESC).
Some people are seriously concerned about the impact ESC could have on their structure. Others not so much. Nonetheless, whether you are concerned or not, you are probably wanting to know what environmental stress cracking is and how you can prevent it.
Here at Forgeway, we regularly come across this issue as we are adhesive specialists. Adhesives (and the bonding process) can sometimes speed up environmental stress cracking. In response to this, we created a product to reduce the threat posed by adhesives.
The purpose of this article is not to promote our product though. We created this article to educate you on what ESC is, and highlight some potential solutions to prevent it from happening.
We will also discuss an experiment we undertook which tested what else can affect environmental stress cracking.
What is environmental stress cracking (ESC)?
Environmental stress cracking is where the force caused by the plastic being under stress or tension, travels along the polymer chains. These polymer chains then creep toward the pull (where the force is being applied). However, the molecules along the polymer chain have to strain to keep in contact with each other.
This is where the stress cracking starts to appear. The molecules along the chain start to deform and eventually separate, causing the stress cracking you see.
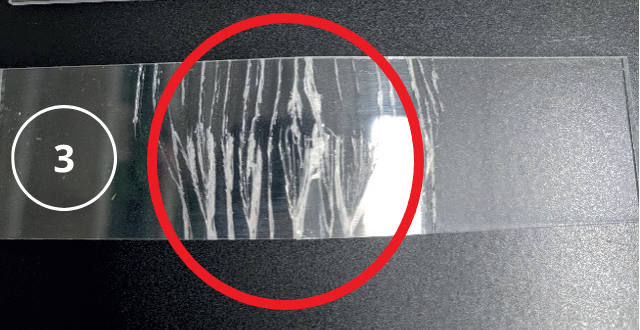
You should also be aware that environmental stress cracking is a problem. Perhaps an even bigger problem than you might have realised. ESC is accountable for 25% of plastic failure in commercial usage. Some refer to it as the ‘plastic killer’.
There are a few things that can speed up the stress cracking process too. Chemicals and heat are the two main culprits, but there is limited research on stress cracking and what other factors affect it. Effectively, any plastic under stress could result in environmental stress cracking.
Which plastics are affected by environmental stress cracking?
As I just mentioned, any plastic under stress could result in ESC taking place. However, three plastics are more susceptible to environmental stress cracking than others; ABS, polypropylene, and Polycarbonate.
It also doesn’t help that these plastics are amongst the most commonly used in the transportation and construction industry. These industries regard them as having some of the much-needed qualities (like impact/chemical resistance) to perform for their structure.
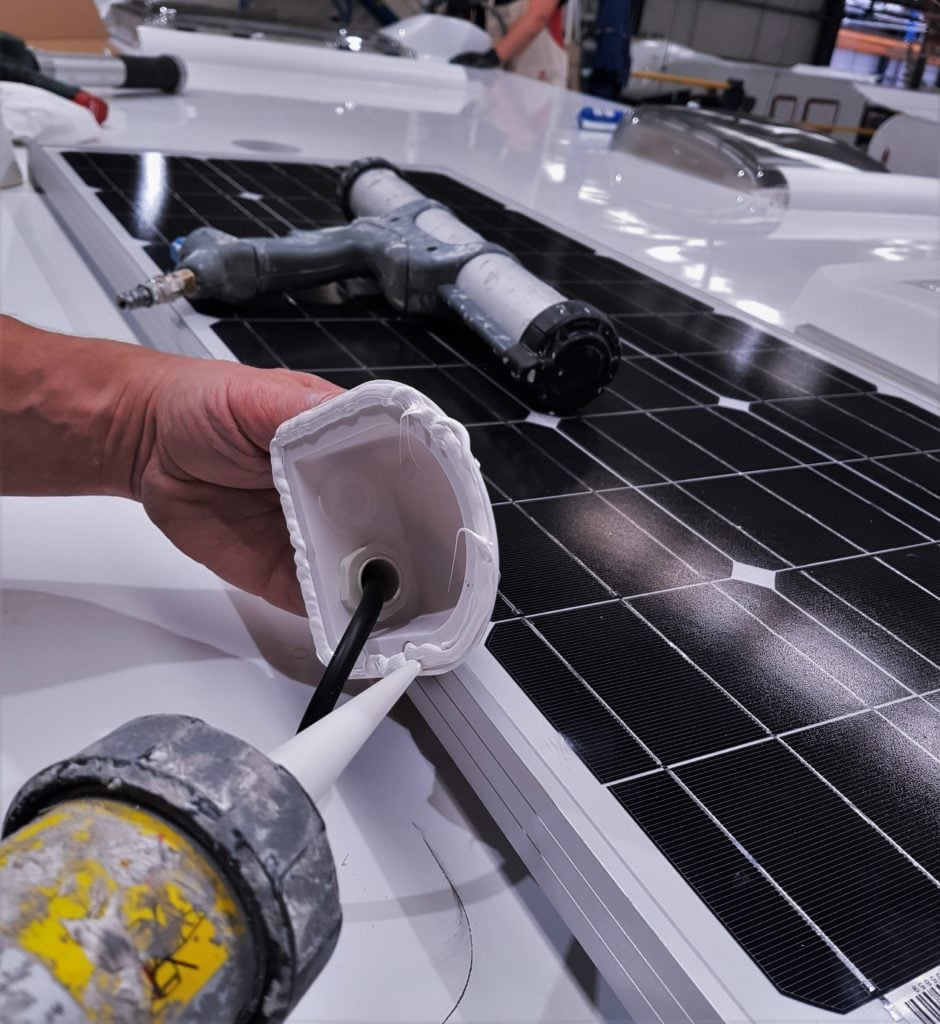
However, the problem doesn’t necessarily lie in the type of plastic being used as environmental stress cracking can affect any type of plastic.
Why does the joining method matter?
The problem arises when the plastic comes under stress. Let’s take a caravan as an example. When the manufacturer needs to join the plastic roof to the body, the area in which it is joined is putting the plastic under stress because it needs to flex to fit in place. The caravan manufacturer would typically use mechanical fasteners or adhesives for this joint.
Some people often say that mechanical fasteners exacerbate the ESC problem, which is true. That’s not to say mechanical fasteners are worse for this situation though.
Often there is a dilemma about whether to use mechanical fasteners or adhesives. But in this situation, it’s difficult to say which one is better as they are both prone to increasing the threat of environmental stress cracking.
Nonetheless, mechanical fasteners are consistently going to pose the threat of increasing the likelihood of ESC. This is because the mechanical fastener is a small focal point in the plastic which means the stress is focused on one area.
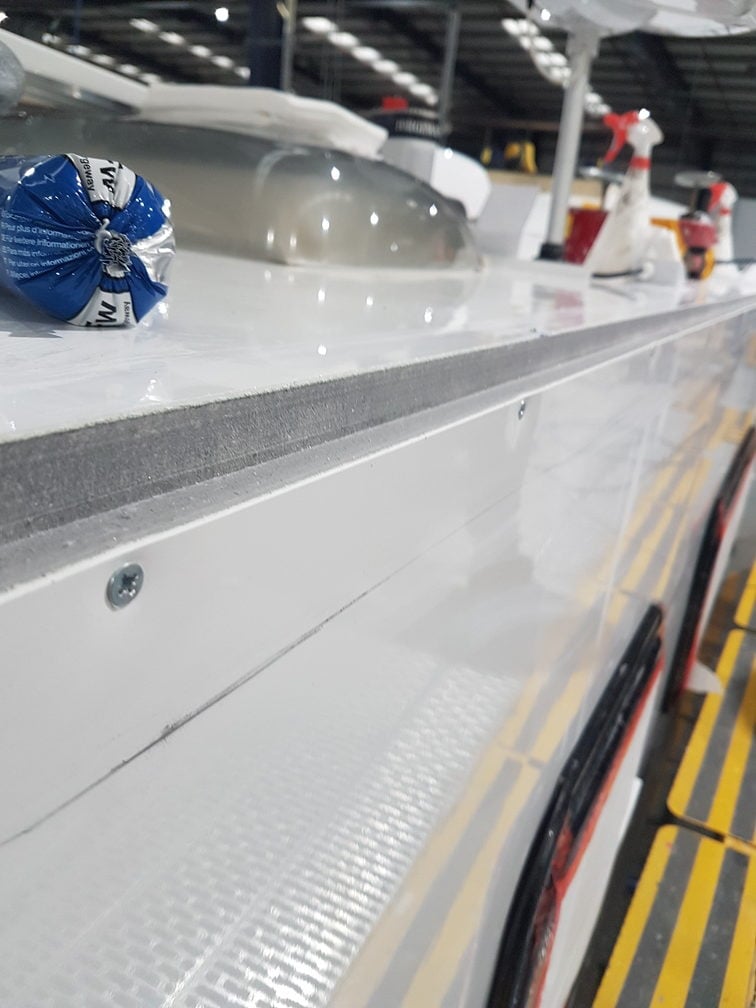
Adhesives will spread that stress across a much wider area so they will not cause stress cracking in that sense. But, adhesives do pose a different sort of risk. As I mentioned earlier, aggressive chemicals can sometimes speed up the environmental stress cracking process.
Some sealants (and adhesives) contain these aggressive chemicals and therefore speed up the ESC process. But that’s not all. The surface treatment methods that are sometimes required can contain these chemicals too. The prime example of this is isopropyl alcohol (IPA) cleaners. We would say that IPA cleaners are one of the worst offenders of attacking plastics under stress.
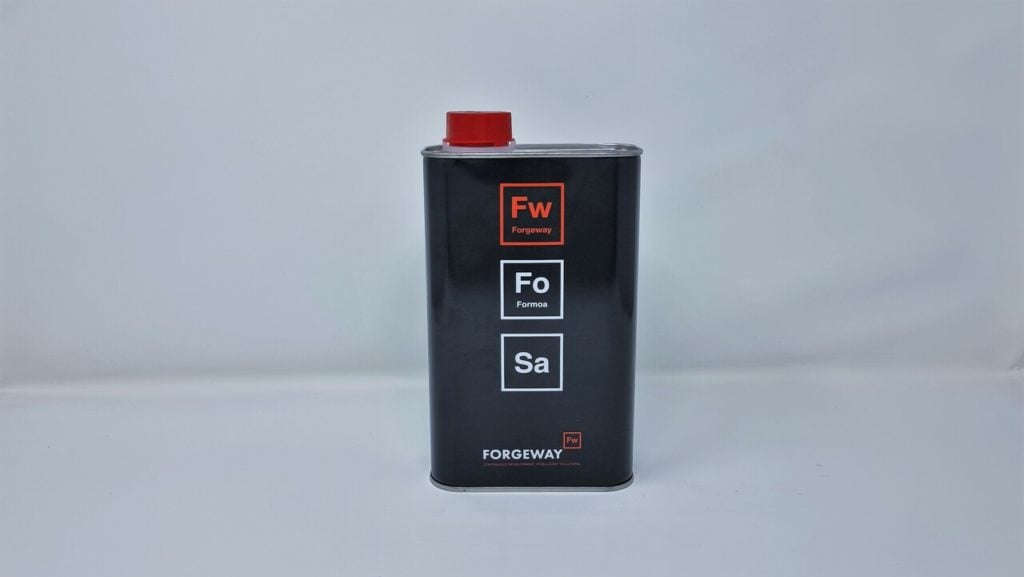
This means that the adhesive application process can pose just as much of a threat as mechanical fasteners. As adhesive specialists here at Forgeway, we will focus on the chemical effect for the rest of this article because this is what we regularly come across.
How much of an effect will chemicals have on stress cracking?
To demonstrate the effect of chemicals on plastics under stress, we conducted our own experiment.
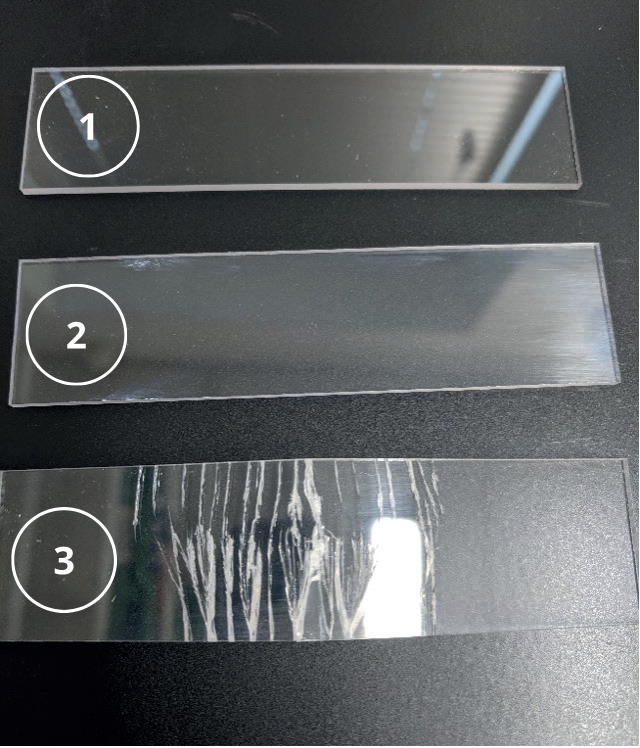
As this picture shows, we used three pieces of polycarbonate. We will call them number one, number two, and number three. Number one and number three were put under an equal amount of strain. We also put an equal amount of chemicals on the bottom two pieces (two & three) but none on number one. The chemical we used is sometimes used in sealants and surface preparators.
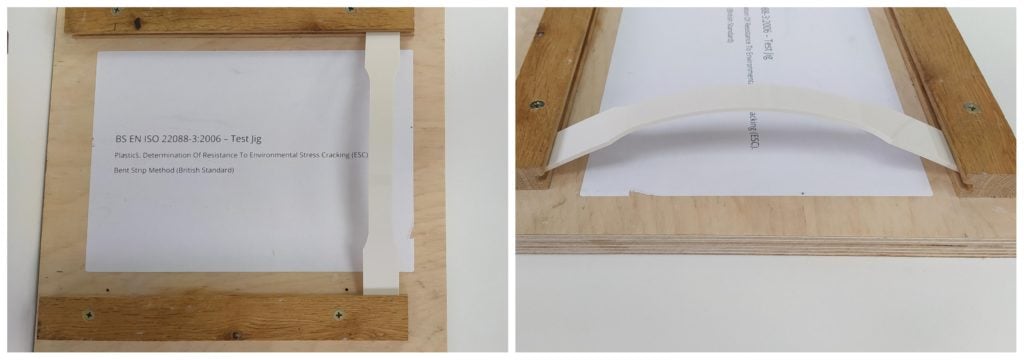
The purpose of this experiment was to see which strip of plastic would experience ESC.
As you can see, piece number three (which was under stress and had a chemical agent on the surface) experienced ESC. Incidentally, it took just 10 minutes for this to happen. However, the first and the second strip of polycarbonate did not experience any form of stress cracking even though number one was under the same amount of stress, and number two had the same amount and type of chemical as number three.
So what can we take away from this experiment? First and foremost, polycarbonate is susceptible to stress cracking, but we knew that already. The plastic also has to be under strain and have a chemical agent applied to experience stress cracking straight away. The final takeaway was perhaps the most interesting. Despite the first polycarbonate strip being under strain for more than 8 hours, no visible signs of stress cracking showed.
This means that you may not see any signs of stress cracking straight away. It can take up to one year before you see any visible signs of stress cracking.
What can you do to help prevent environmental stress cracking?
So, you now know that mechanical fasteners and adhesives can cause the ESC process to speed up. You may be thinking “well what joining method can I use that won’t cause ESC?” and it may seem like there’s no hope.
There are things you could consider to help prevent the threat of ESC from taking place though. We’ve listed the top three recommendations if you are worried about the threat of environmental stress cracking:
- The best way we would suggest is to reduce the stress on your plastic. We know this is easier said than done, but if you can reduce the stress, the threat of ESC will be significantly reduced.
- Stay away from using mechanical fasteners where possible. Use chemicals that have been tested and are not likely to increase the chance of ESC taking place.
- Steer clear of using IPA cleaners. As mentioned earlier, these are very likely to attack plastics under stress and cause ESC. Heptane-based cleaners do not present this problem. But they are potentially hazardous, and some companies are hesitant to use them. Acetone cleaners are also aggressive cleaners that will attack plastics under stress.
You can eliminate the fear of stress cracking through testing. There are several testing methods available to test whether the chemical is likely to attack the plastic under stress.
Chapter seven of our Ebook goes through some of the different test methods for testing your plastic as well as many other test methods. You can download the entire Ebook with the link below if you want to find out even more about adhesives and sealants.
Alternatively, if the prospect of environmental stress cracking is a massive concern still, you can reach out to one of our experts. They will help you through your particular situation and provide advice on the next steps.
Thomas is the Content Manager here at Forgeway. Thomas' job is to translate the technical jargon from the ivory tower of academia into easy-to-read content that everyone can understand. Forgeway's mission is to answer every question our customers and prospective clients ask, or are apprehensive to ask.
Topics: