Your guide to understanding Forgeway’s Auditing service
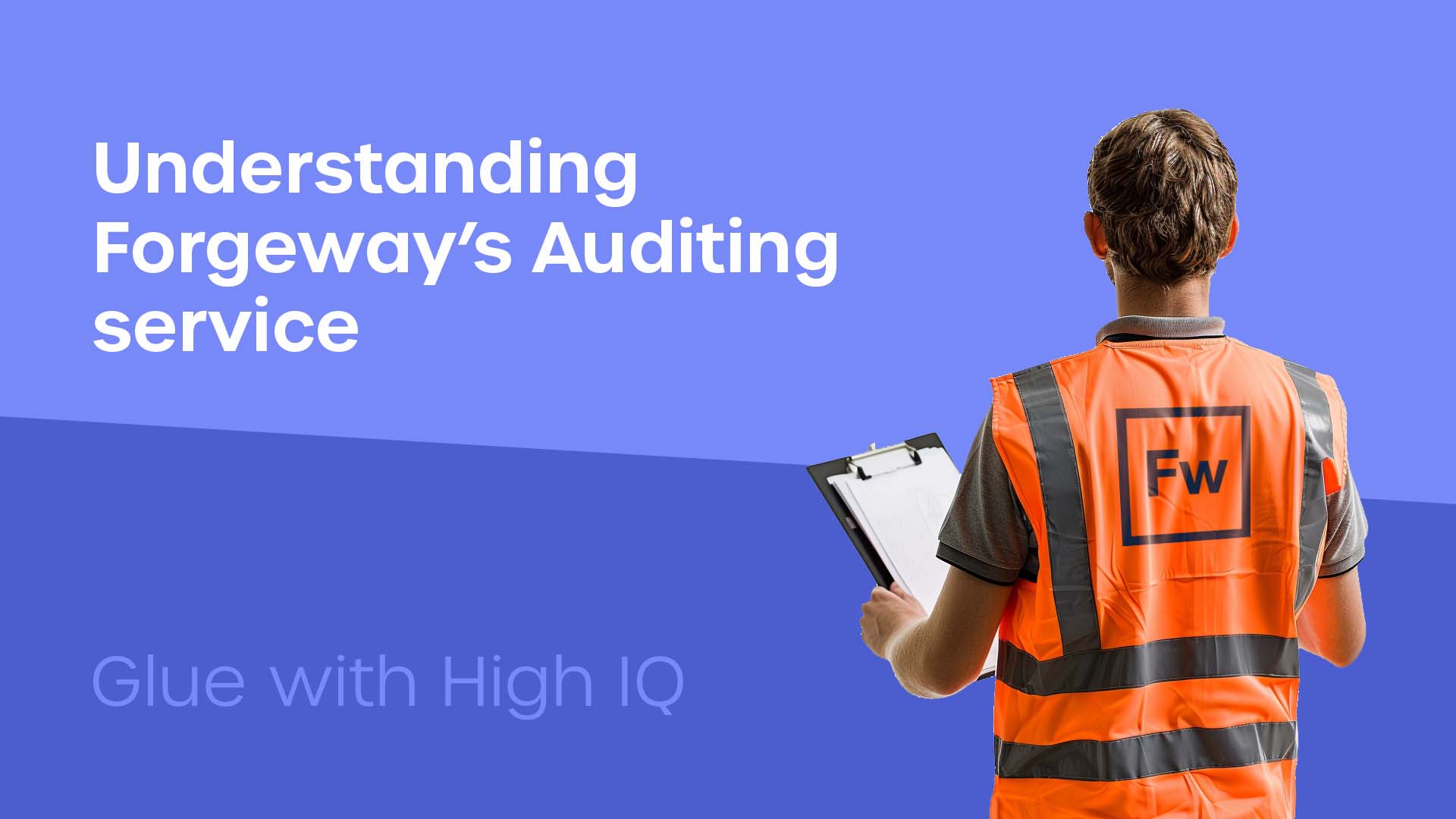
You’ve heard about Forgeway’s auditing service and you’re interested to find out more. But what actually is it? And why should you consider using this service?
As industrial adhesive manufacturers, we help our customers ensure they avoid failure. We believe it isn’t just about the adhesive you are using, it’s ensuring you use that adhesive properly.
This article will give you all the information you need to know about our auditing service here at Forgeway. We will discuss what an audit is, what we look for during audits, and how we score audits.
By the end of the article, you will have a better understanding of Forgeway’s auditing service. You will know what to expect.
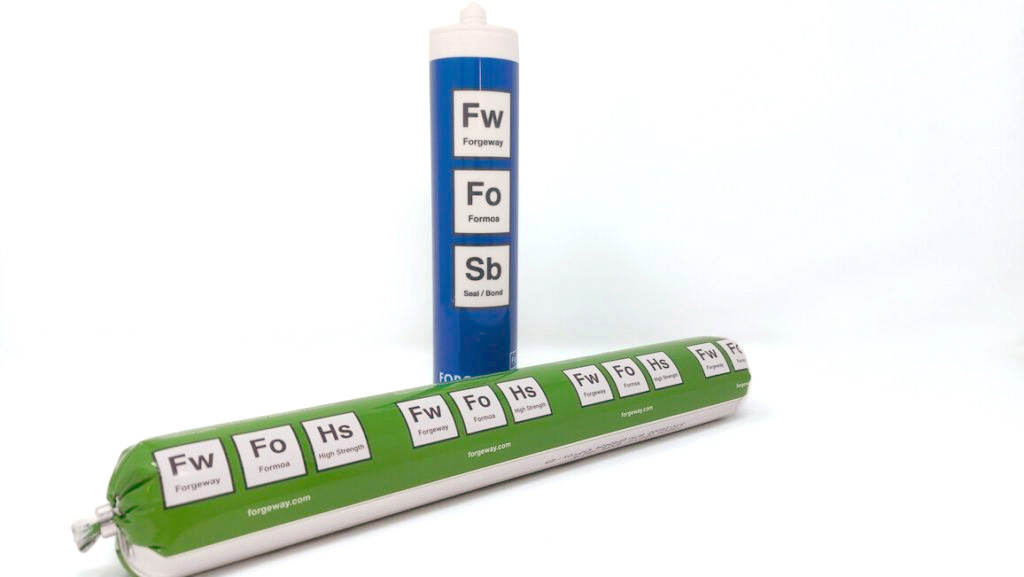
What is an audit?
An audit is an inspection of the entire bonding process. As we have said, avoiding failure isn’t just down to the adhesive product. We evaluate the bonding process holistically.
An audit will highlight any areas where the bonding process isn’t performed to a satisfactory level and suggest ways to improve.
The audit checks to see if standard operating procedures (SOPs) are being followed. This catches any future problems from becoming a crisis further down the line.
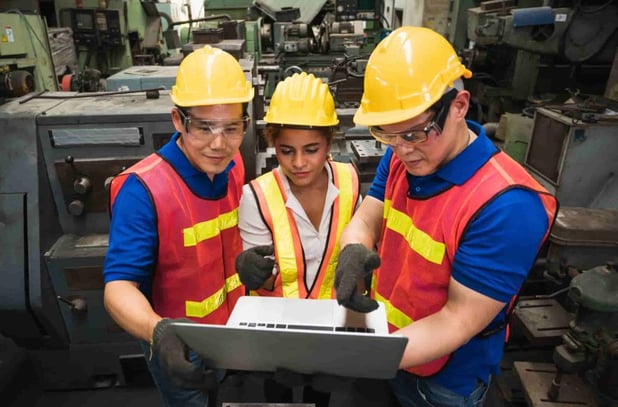
Why do we audit our customers?
We thoroughly believe that selling a quality product is just part of helping our customers avoid failure. Sometimes, we have seen a poor-quality bond cause failure in the field within just one month.
We also know that adhesives and bonds are mostly hidden.
Unlike mechanical fasteners and welding, a bonded joint will not be visible. This makes it harder to tell whether the joint is of sufficient quality.
So that’s why we offer this auditing service. It helps you ensure operatives are following the bonding process correctly.
If operatives are following the bonding process, you will not experience these failures.
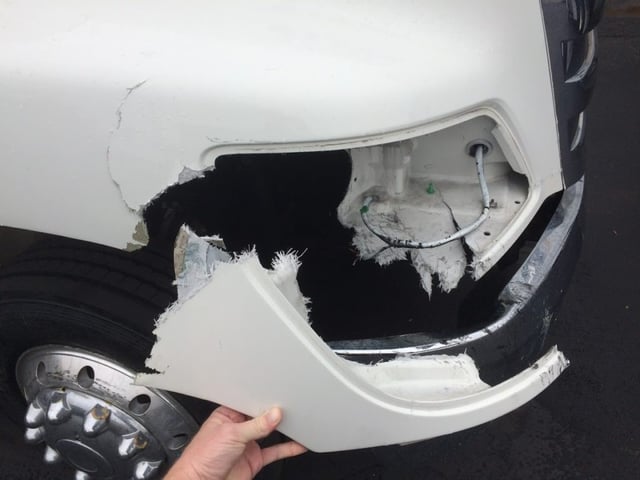
What do we inspect during an audit?
During an audit, we would typically inspect the following:
- Temperature – The temperature of the bonding environment and storage plays a massive part in the adhesive’s performance. We will check to see if the temperature is likely to affect performance. If the temperature is incorrect, we have tips on how to maintain the right temperature.
- Storage – The correct storage will ensure product performance isn’t affected. The three main areas of storage we check are; stock rotation, temperature, and labelling. There are rules you should follow when storing adhesives.
- Open time management – If you don’t manage the open time of the adhesive effectively, you will find that there is a much greater risk of bond failure.
- General housekeeping – It’s not uncommon for operatives to leave adhesives half-used or surface activator tins open. We will pick up any malpractices and highlight them in the report.
- Areas of improvement – Audits aren’t all doom and gloom. As adhesive experts, we constantly see ways we could improve the processes. This could be speeding up the surface preparation process, suggesting a faster curing adhesive, or even suggesting using a different joining method if we think it could improve your process.
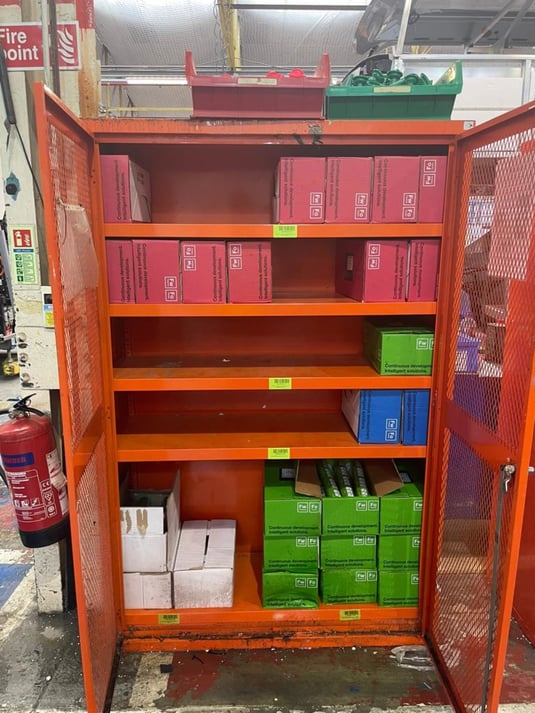
How would you be scored during these audits?
Unlike some other auditing services, we don’t follow the RAY (Red, Amber, Yellow) method. Instead, we follow the RAG (Red, Amber, Green) system.
- Red highlights areas that require immediate action.
- Amber highlights areas that need observation
- Green highlights areas of excellence
So why this RAG method?
Simple. You are likely performing the majority of your bonding process to a high standard already. The green marker indicates these areas so that others can follow that good example.
An audit is not all about handing your company a load of actions to follow up on after we have gone. But we also love to see where our customers are performing to a high standard.
However, that doesn’t mean we aren’t thorough. We would always alert you to any problem we see.
That’s why we follow the RAG method.
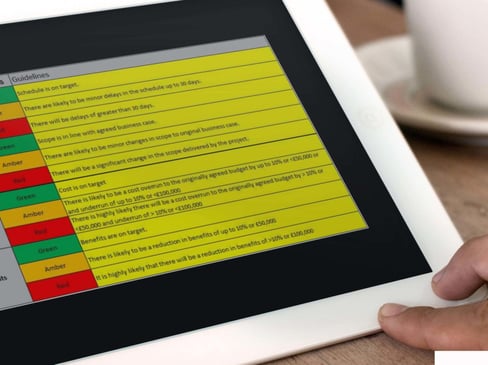
How often should you have an audit?
We expect most customers to conduct their own audits monthly. We would then follow up with an annual audit (if requested).
However, customers using a large quantity of our adhesives (over £100,000 annual spend), we would recommend an audit on a more frequent basis.
We understand that monthly auditing is not always viable, although we would recommend this where possible.
Each audit will start with a review of the previous audit to check the progress of the recommendations. Then the auditing process begins.
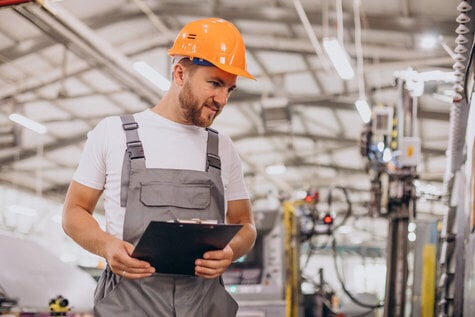
Should you be auditing your bonding processes?
Now that you know all about the auditing service and why it’s so important, it’s time to decide whether it’s the best way forward for your organisation.
As adhesive manufacturers, we always look to help our customers avoid failure. When it comes to adhesives, regular auditing is the best way to avoid the errors that cause failure.
That doesn’t mean you need to get an adhesive expert from Forgeway to audit your processes every month. We like to make things as simple as possible.
So we recommend you appoint a competent person to conduct a regular audit of your bonding process.
Competent simply means they know what to look out for (we will offer training and guidance on who qualifies as competent). Regular means that audits should never be more than two months apart.
If you have some more questions about the auditing process or would like to talk to an adhesive expert about this further, get in touch. We would be happy to assist you further.
In the meantime, our eBook – The Fundamentals of Adhesives – will help you gain knowledge and expertise on adhesives and the bonding process. Download it by clicking on the banner below.
Thomas is the Content Manager here at Forgeway. Thomas' job is to translate the technical jargon from the ivory tower of academia into easy-to-read content that everyone can understand. Forgeway's mission is to answer every question our customers and prospective clients ask, or are apprehensive to ask.
Topics: