Welding polypropylene has its pros and cons; Is it the best method for joining polypropylene?
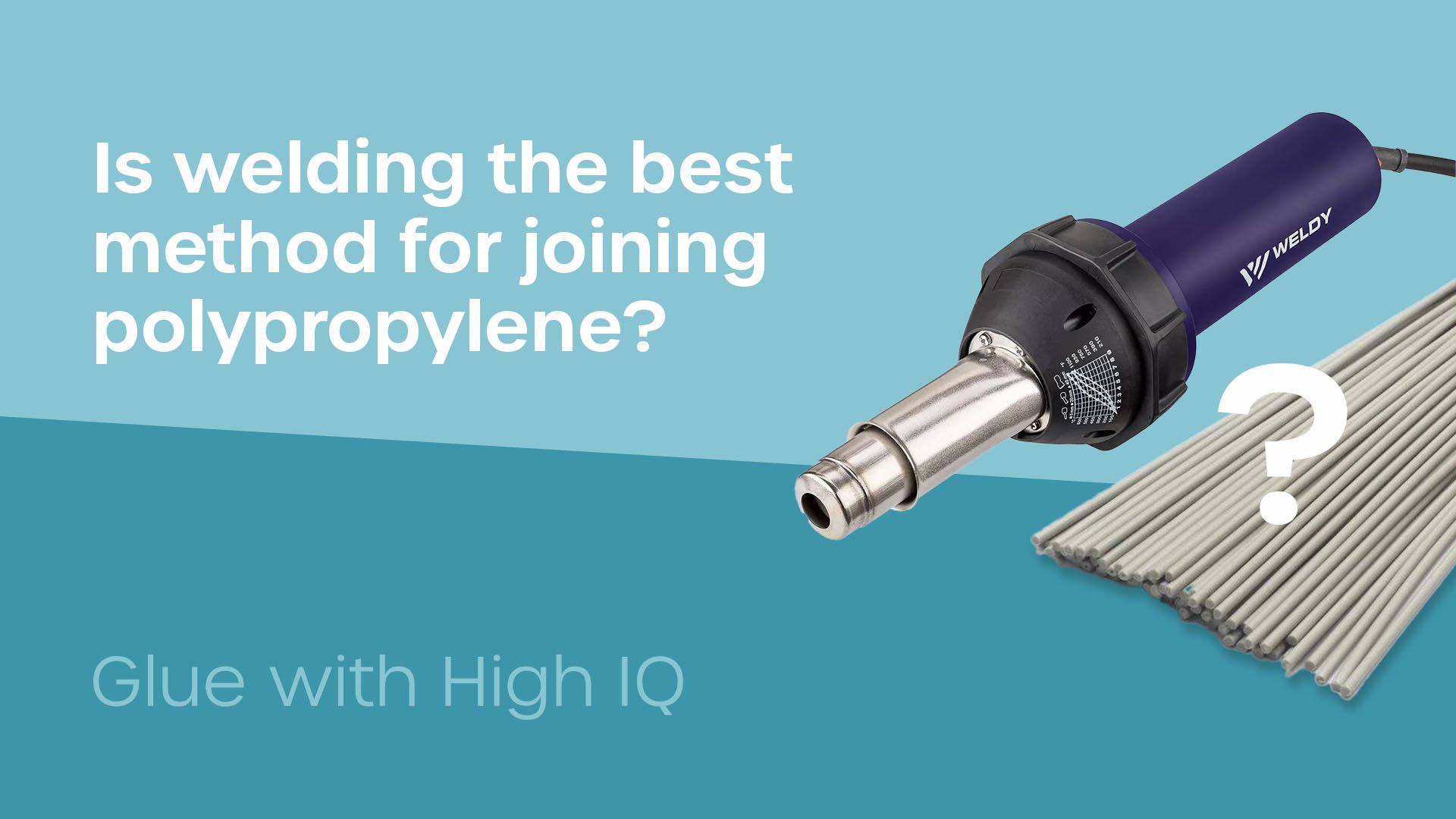
You are trying to join polypropylene and you’ve identified welding as a potential method. However, you aren’t sure where to look to find information that can help you assess whether welding is the best joining method for joining polypropylene.
Here at Forgeway, we manufacture industrial adhesives. We also help industrial manufacturers find the best joining method for their applications. As adhesive manufacturers, we believe adhesives are the best method of joining.
We also know that sometimes, welding is a much better method. That’s why we will give you the information you need to help you decide. It ultimately comes down to what you want from your application.
By the end of this article, you will have a better understanding of the advantages and disadvantages of welding polypropylene. You will be better placed to decide on the best joining method.
What are the advantages of welding polypropylene?
Welding polypropylene is one of the most popular joining methods for a reason. The main advantages of welding polypropylene are the high-strength, durable, and lightweight joints it can create at a low cost.
This section will go over those advantages in more detail.
Welding polypropylene creates high-strength and durable joints
One of the main advantages of welding polypropylene is its high strength and durability. This is because the joint is polypropylene plastic. The welded joint just brings over the qualities that make polypropylene so popular.
Polypropylene is also resistant to many chemicals. This means the welded joint can withstand the effect of chemicals, making it a good choice for projects that will be exposed to corrosive substances.
When properly welded, polypropylene can withstand harsh environments and heavy loads, meaning a welded joint will be strong and durable for a variety of applications.
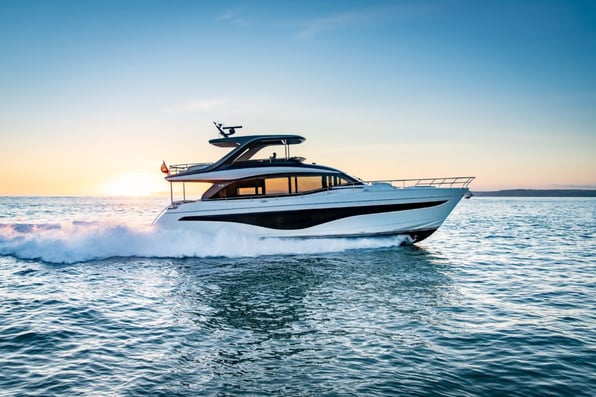
Welding polypropylene is lightweight
As we mentioned above, welding polypropylene carries over the existing characteristics of this popular plastic. One of the reasons polypropylene is the second most popular plastic is its high strength whilst remaining lightweight.
Welding polypropylene means you don’t have to worry about added weight. This is in contrast to joining methods like mechanical fasteners. This makes welded polypropylene joints easy to handle.
It also means that if you are trying to lightweight your product (like most vehicle manufacturers), polypropylene welding can help you save weight.
Polypropylene welding is low cost
Polypropylene isn’t just lightweight, it’s also low-cost. When it comes to welding, you don’t need a lot of high-cost parts (like mechanical fasteners and structural adhesives).
You will need the welder, any accessories (like scraper tools, and sandpaper), and a skilled welder. Welding polypropylene is often the most cost-effective joining method.
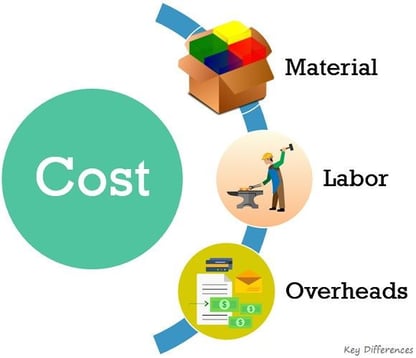
What are the disadvantages of welding polypropylene?
Welding polypropylene isn’t perfect, there are a few disadvantages you should be aware of. The main disadvantages of welding as a joining method include its inability to join dissimilar materials, its difficulty, and its tendency to shrink the plastic.
We will discuss these disadvantages in more detail in this section.
Polypropylene welding cannot join dissimilar materials
One of the main disadvantages of welding any material is its inability to join dissimilar materials. Welding polypropylene is no different. You can only weld polypropylene to other polypropylene parts.
So, if you are trying to join the plastic to other materials (such as metals or GRP), you will have to rule out welding as a potential joining method.
It is never advised to weld different types of plastics together. The plastics aren’t compatible and the joint will not have sufficient strength.
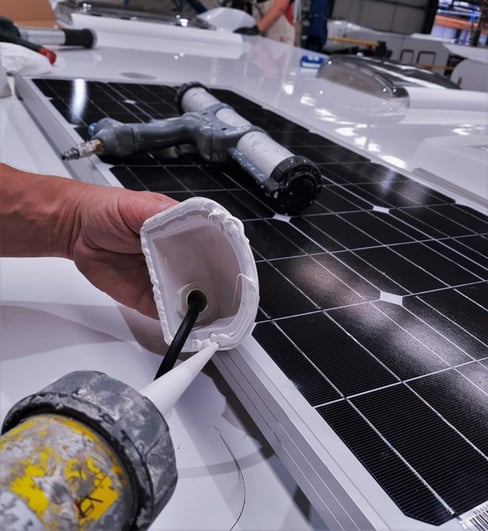
Polypropylene welding can be difficult to master
Any joining method requires skill. Welding is a particularly difficult skill. If not welded correctly, the joint can become brittle or can damage the integrity of the plastic itself.
There are a few steps you can take to help you ensure the welds are high-quality. But, the only way you can be sure the weld is going to be high quality is to have a high-quality welder.
However, these are difficult to find. You may have to risk using an inexperienced welder.
Welding polypropylene can damage the plastic
If the temperature is too high during the welding process, the material can become distorted or even melt. This can make it difficult to achieve strong and consistent welds.
Polypropylene also tends to shrink during the welding process, which can lead to warping and other problems. This can be especially challenging when welding large pieces or when trying to achieve a precise fit.
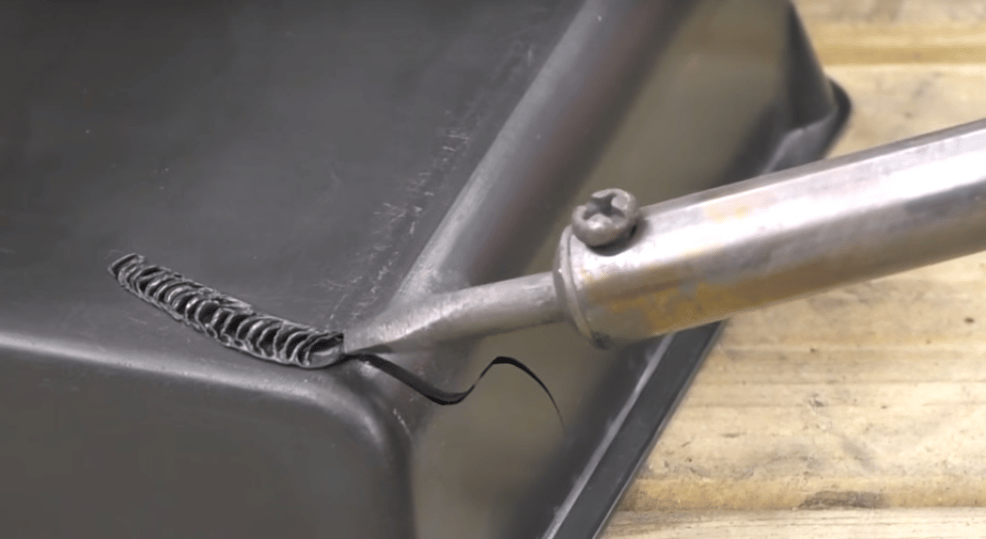
Is welding the best method for joining polypropylene?
This question is impossible to answer without knowing the exact details of the project. Now you know the advantages and disadvantages of this joining method, it’s up to you to make the decision.
As industrial adhesive manufacturers, we often advise companies on how to join polypropylene. Welding is a very popular method due to its high strength and durability, chemical resistance, and low cost.
But the challenges of heat sensitivity and shrinkage can be difficult to overcome. And you may struggle to find a skilled welder who will produce quality welds. You also cannot use welding to join dissimilar materials.
So, if you are joining dissimilar materials or you are concerned about damaging the plastic, you will need to look at alternatives. We suggest you read our article about how to bond polypropylene with glue.
Or, if you would like to take a step back and compare the alternatives, read our article which discusses the difference between adhesives and mechanical fasteners.
Still not sure? You can join our webinar on bonding plastics which will help you understand everything you need to know about this topic. Click on the button below.
Thomas is the Content Manager here at Forgeway. Thomas' job is to translate the technical jargon from the ivory tower of academia into easy-to-read content that everyone can understand. Forgeway's mission is to answer every question our customers and prospective clients ask, or are apprehensive to ask.
Topics: