Ensuring a new adhesive project doesn’t slip up at the testing stage; Tips and considerations
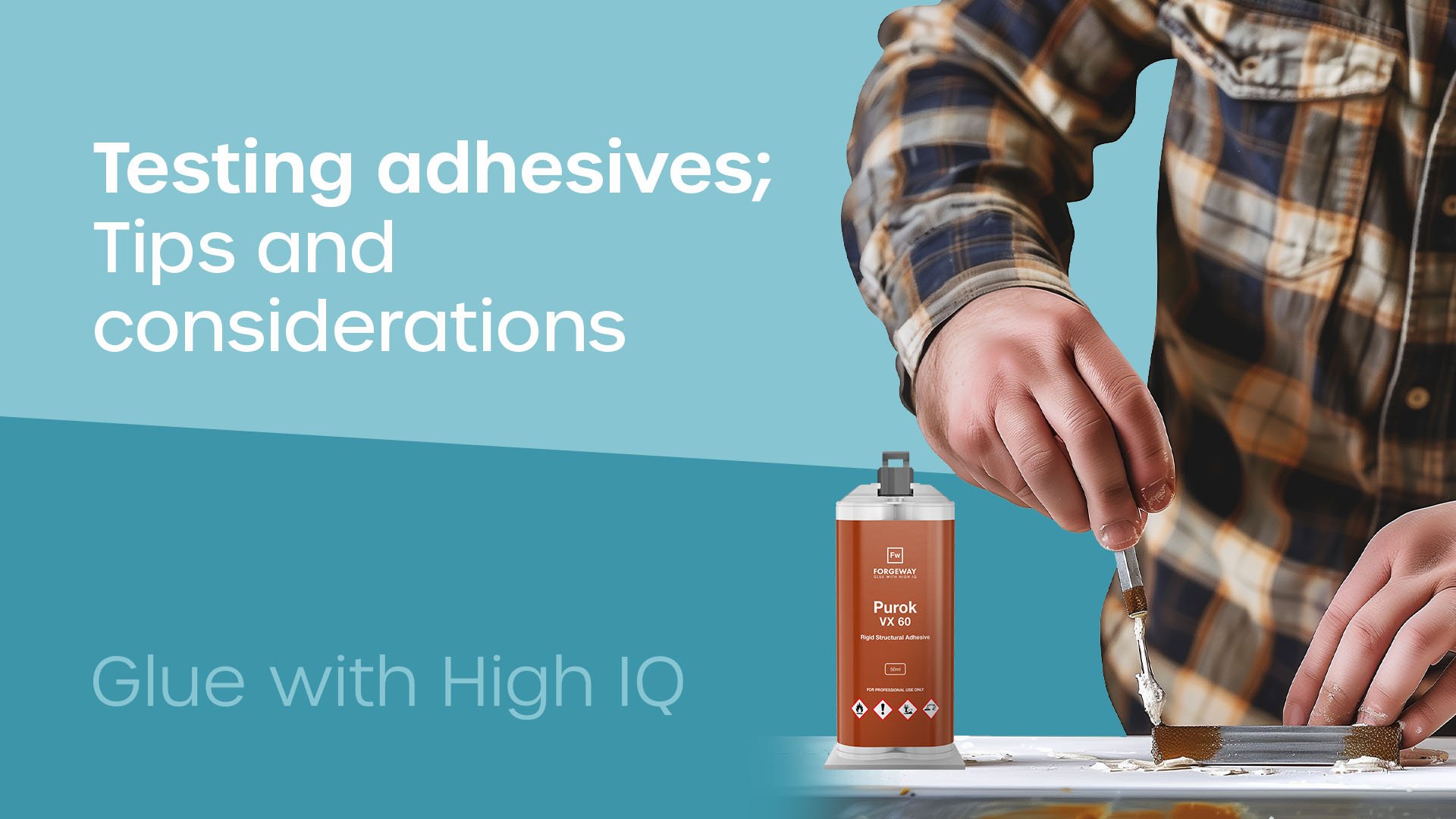
You have reached the point where you have established one (sometimes more) adhesive product as the ideal fit for your application. Now you need to conduct some testing to ensure the adhesive product is the right fit.
But this stage is often where a lot of new adhesive projects go off the rails. As an adhesive manufacturer here at Forgeway, we often see this happening.
Companies will choose an adhesive they think might be a good fit. They then go off to test that product. However, the new adhesive project often stalls at this point. No more progress is made.
So we wrote this article to go through the different factors that can derail the project. It will help you avoid common pitfalls. By the end of the article, you will know what you need to do to ensure the project keeps on track.
What to consider before starting your adhesive testing process
Establish what good looks like
Before starting the adhesive testing process, you must establish what ‘good’ looks like. We can’t tell you what a good test result looks like for your company. We can certainly help you though.
This is essential because if you don’t even know what the adhesive needs to do in order to pass, how is it ever going to pass the tests?
Establishing what good looks like will enable you to measure the adhesive against the criteria you set. You can easily see whether the adhesive meets the criteria or doesn’t. A pass or fail is simple to see.
Some examples of common characteristics that companies test adhesives for are:
- Strength (whether it is strong enough to hold the substrates in place)
- Flexibility (whether it can withstand shocks and vibrations)
- Viscosity (how easy it is to work with)
- Weathering resistance (will it hold its colour/maintain performance)
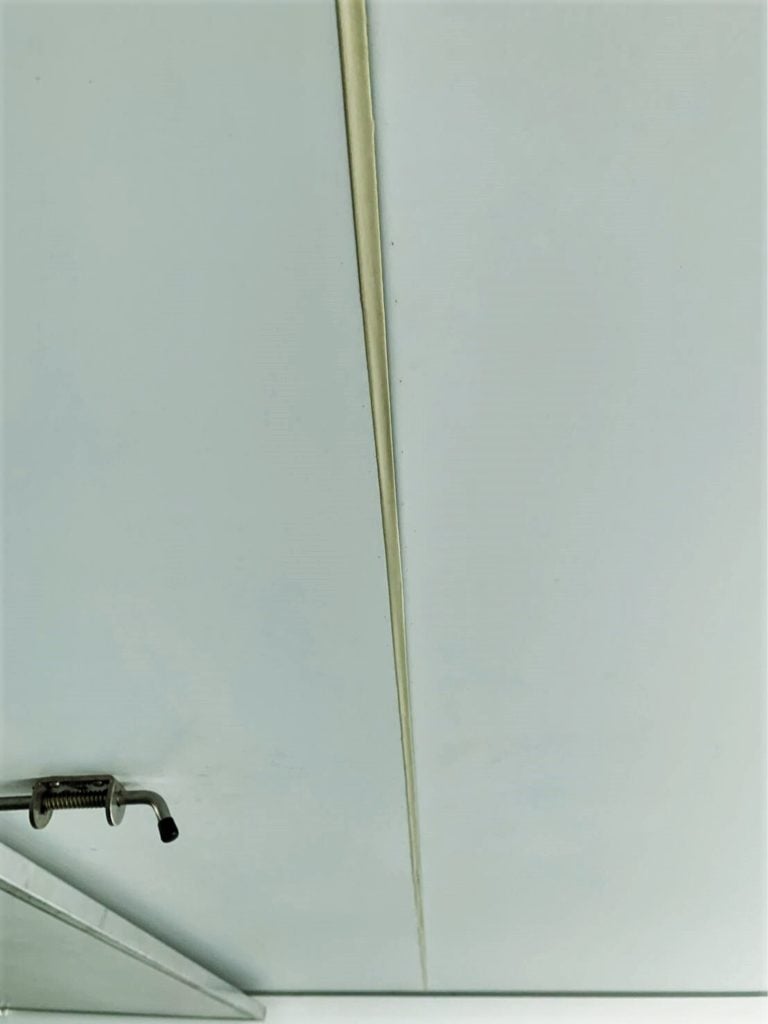
These characteristics are not all the characteristics you can test for. But once you have established the characteristics, you can determine the benchmark the adhesive needs to meet for that characteristic.
We will use an example where you are testing for strength and flexibility. A caravan manufacturer established that a ‘good’ test result was cohesive failure when they tried to destroy the caravan. Cohesive failure is where the substrates separate, but there is adhesive on both surfaces.
This basically means that the bond between the adhesive and the surface is stronger than the adhesive itself. If the adhesive hadn’t cohesively failed, the adhesive obviously doesn’t have enough strength and flexibility to pass the test.
The adhesive manufacturer found that they did get cohesive failure when they subjected their product to this test. Therefore, the adhesive passed the test.
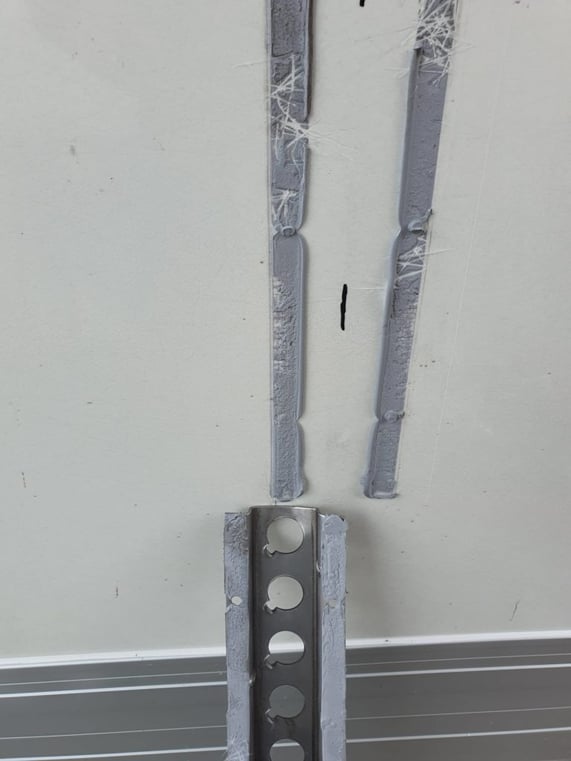
Agree on the pricing of the product before testing begins
This is nearly as essential as establishing what ‘good’ looks like. However, most companies will gloss over this part. You must (at least) discuss pricing before starting the testing process.
If you miss this step, you could waste a lot of time, resources, and – ultimately – money. You will go through the testing process and you establish that it is a good fit. But now that it comes to purchasing the product, you find out that the price is far outside your price range. It is not a feasible option.
Agreeing on pricing before the testing process means you don’t waste anyone’s time.
Agree on how to implement the product if it passes testing
When you don’t have a plan in place for the product’s implementation, it can dramatically slow the process. This is because you get to the end of the testing process, the adhesive is the ideal solution, but you don’t know what’s next.
There are a few different ways a plan for implementing the product could look. One is agreeing on how you will transition from the existing process to the new adhesive if it does pass the test. This will mean you know how much adhesive product you will need to order if it does pass.
When planning the testing process, you must know what the next steps look like if the product passes.
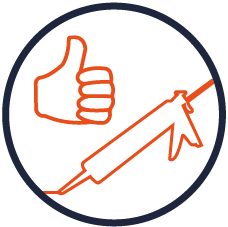
Ensure everyone is fully invested in the change
Whenever we start working with new companies, there is one thing we absolutely have to make clear; the need for change is greater than the resistance to change.
Sometimes, companies will make it to the testing stage, but they still don’t have full stakeholder buy-in. This means you may get to the point where you have tested the new product and it is a suitable fit, but some stakeholders aren’t convinced. The project derails.
The other common situation is where a company is experiencing supply issues. They desperately look for alternative adhesive solutions. They test the new product(s) to see if it meets the criteria, but the original supply issues are sorted. The project derails.
Whatever the situation, you must be 100% certain that your company is ready and committed to the change.
Ensure all health and safety concerns are ironed out
Sometimes, the adhesive testing process highlights health and safety concerns. Whilst you can mitigate most health and safety concerns, it is often an arduous process.
You are best off making sure you have the relevant health and safety requirements in place before you start the adhesive testing process.
Establish what regular communication looks like
Regular communication is key during the testing process. It means you have a set time when you can bring any questions you have about the testing process or the adhesive product. This means that we work together to resolve any issues quickly and effectively.
We recommend meeting at a set time every week to discuss any questions or concerns.

Are you ready to start the adhesive testing process?
Now that you know the different things you need to consider before the adhesive testing process, you now want to know the best way to stop your new adhesive project from derailing.
As we manufacture a range of adhesives here at Forgeway, we often see new projects stalling. That’s why the above tips will give you the best chance of stopping this from happening to you.
To summarise, to ensure your new adhesive project doesn’t stall, you should consider the following before starting the testing process:
- Establish what good looks like
- Agree on pricing
- Agree on implementation and next steps
- Ensure you are fully invested
- Deal with any health and safety concerns
- Set up regular communication
If you have gone through the above steps and are still unsure if you are ready to begin testing, you can reach out to us and we would be happy to help you.
However, if you feel as though you are ready, we recommend reading our article on the different adhesive testing methods. It will help you establish which testing method is right for you.
Thomas is the Content Manager here at Forgeway. Thomas' job is to translate the technical jargon from the ivory tower of academia into easy-to-read content that everyone can understand. Forgeway's mission is to answer every question our customers and prospective clients ask, or are apprehensive to ask.