Adhesives: Driving Lighter Vehicles for a Sustainable Future
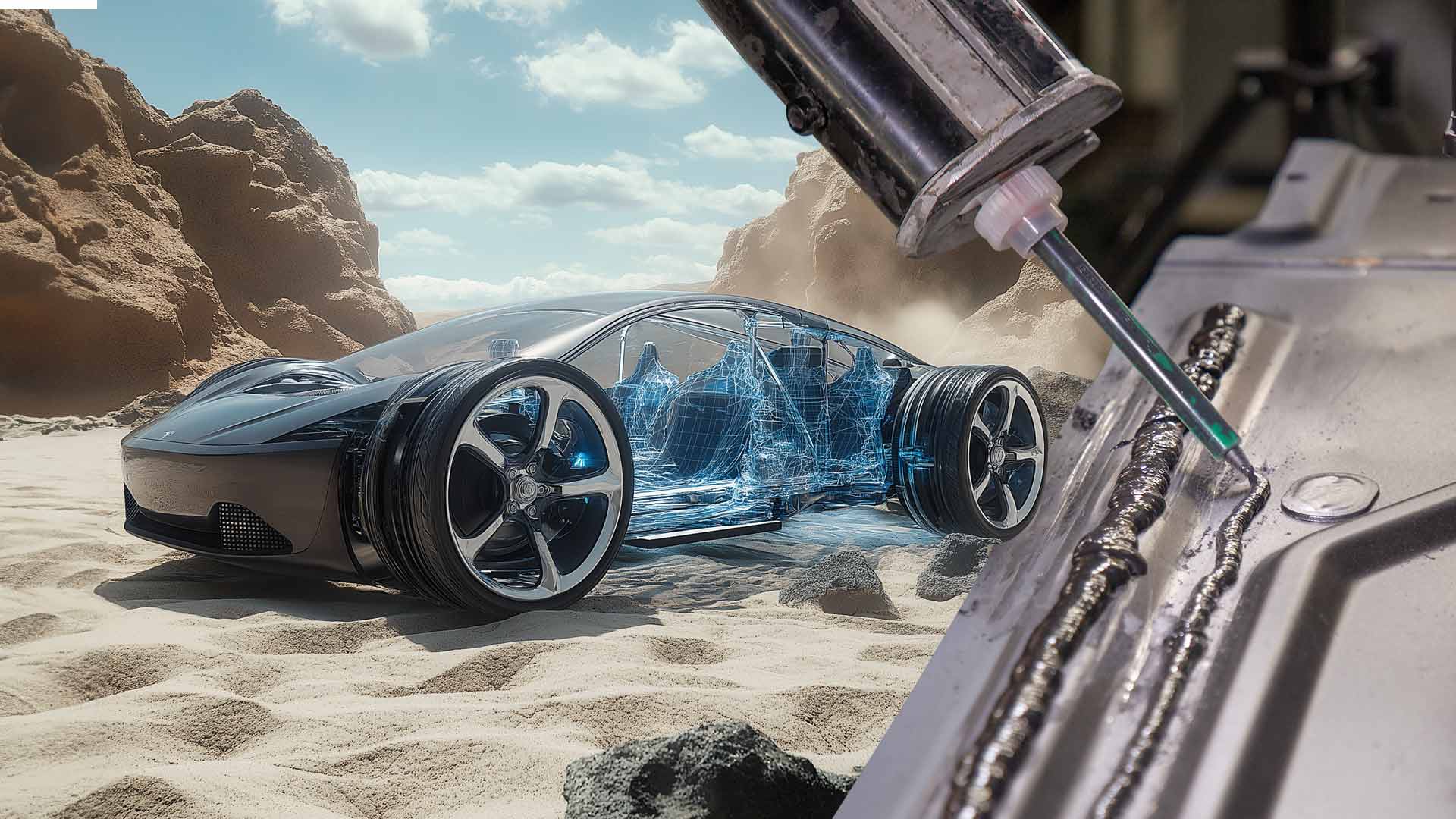
The world is shifting toward a sustainable future. A future that doesn't pump billions of tonnes of CO₂ into the atmosphere every year. Today, engineers, scientists, and manufacturers face a monumental challenge to reach Net Zero before 2050.
We believe adhesives are going to play a pivotal role in getting there. As an adhesive manufacturer, we may seem biased. But we want to explain why we hold this opinion.
At Forgeway, we've been manufacturing adhesives for over 25 years. Our customers are the driving force behind the necessary change to create a Net Zero future. We've seen some very impressive work in the vehicle industry to ensure electric vehicles are not only possible but a superior option to ICE vehicles.
In this article, we discuss how adhesives contribute to making electric vehicles possible, and desirable to buyers. We also were able to use the expertise of Lydon Sanders from Far-UK to help explain the topic.
By the end of the article, you will understand the number one reason why adhesives can contribute towards lighter-weight vehicles and a sustainable future.
Why do lightweight vehicles help towards a sustainable future?
Before we look at the bonding and adhesives used in lightweighting, we should first analyse why lighter-weight vehicles are so important in the first place.
Lighter vehicles will always be more efficient than heavier vehicles. That's basic physics. The Aerospace industry has always spent colossal amounts of time, resources, and money on reducing the weight of their planes.
Reducing 1 kg per aircraft can save up to $300 in fuel per 5000 flying hours. Larger-scale weight reductions will have an even greater impact on fuel use.
So for Internal Combustion Engine (ICE) vehicles, less weight means less CO₂ produced.
But we all know that ICE vehicles aren't the future. They don't have a place in a sustainable society. Even if they did, most countries are banning them. The UK will ban new ICE vehicle sales from 2035. In other regions, that date is more like 2030.
In their place, electric vehicles are looking likely to be the most affordable and convenient replacement. However, a lot of people are hesitant to change to an electric vehicle.
Safety, residual value, and most importantly range anxiety contribute towards buyer hesitancy. The weight of these electric vehicles certainly doesn't help. Sometimes, they can be twice as heavy as their direct ICE alternatives.
That increased weight doesn't help with efficiency. It also contributes towards the issues with safety and range. It's important to remember that increased weight isn't the only factor in these challenges.
Most people agree EVs need to become lighter.
Batteries are the largest contributor to that weight. They are also the most fundamental part of the electric vehicle making it difficult to make weight savings with the battery. Advances in technology will see batteries reduce in weight going forward, but it's not available yet.
Nonetheless, manufacturers need to find ways to reduce the weight of their vehicles. The batteries available today mean that weight reduction needs to come from other areas.
Electric vehicles are key pieces of the puzzle in creating a sustainable future. But to increase widespread adoption, we have to qualm the fears of potential buyers.
Manufacturers have demonstrated that it's not possible to place an electric drivetrain in the design of an ICE vehicle. It's too heavy.
There's a lot of work to do. And finding ways to reduce the overall weight is essential.
How can adhesives help with lightweighting?
With the future in mind, let's take a look back at the past to see what we can learn. To provide context to the answer, we should use some real-life examples. The electric vehicle many consider to have led the way in the market was the Telsa Model S.
No, it wasn't the first electric vehicle on the scene. Neither was it the 'best'. But it did become very popular very quickly.
Early on in the development, Tesla realised that they couldn't just take the chassis and frame of an ICE vehicle and put an electric drivetrain and battery pack. It was too heavy.
So they developed an almost entirely aluminium frame to reduce the weight. The car went on to be the most popular EV for years. The design is largely shared with the most popular EV today, the Tesla Model Y.
During that period, there were other fascinating developments in the EV market. BMW was showcasing equally impressive innovation in their i3 model.
The use of Carbon Fibre Reinforced Plastic (CFRP) in the body and aluminium in the chassis enabled BMW to significantly reduce the weight of the i3.
Many other automotive manufacturers are following suit. They are increasing the use of lighter materials in their vehicle design to reduce weight.
So what does all this have to do with adhesives? As adhesive manufacturers, we see the very close link between these necessary material changes and adhesives.
Previous vehicle designs would have primarily used steel. Steel to steel is traditionally easy to join by welding or mechanical fixings.
However, with the inclusion of lightweight materials like the CFRP of the i3 and the aluminium of the Model S, traditional joining methods are no longer suitable.
Composite materials and thermoplastics are becoming increasingly common in vehicle design. However, you will struggle to weld these to metal frames.
You also typically wouldn't want to use mechanical fasteners for joining composites. The damage caused by the drilled holes, coupled with increased point loading and holding torque make it an undesirable joining method for composites.
So you're left with adhesives as the most effective joining method. Effective, yes. But not just effective. Adhesives can provide significant advantages over other methods of joining.
One reason is that they vary massively. The different chemistries and formulations mean you can usually find an adhesive that has characteristics to suit your application. Not every application is the same. The versatility of adhesives means your application can find a suitable match.
Need faster curing? You can get that...
Has to withstand high temperatures? No problem...
Have a process with wider dimension tolerances? Adhesives can do that…
It doesn't end there. Adhesives can also provide additional structural support to the metal frames. Where mechanical fixings leave focal points of stress, adhesives can spread the load over the length of the bond.
We have seen instances where this has increased energy absorption by metals. Lyndon Sanders of Far-UK explained that this effect, combined with the versatility of adhesives, has enabled designers and engineers to create innovative crash structure designs for vehicles.
The same innovative designs that are going to drive the sustainable revolution.
There are instances where adhesives aren't ideal. We aren't painting them as the answer to all problems. Nonetheless, adhesives offer an easy way to join materials that are otherwise challenging.
They offer designers a way to incorporate lighter materials into their vehicles.
They enable an easier and more efficient transition to a sustainable future.
How else can adhesives contribute to a sustainable future?
The most significant contribution of adhesives is their ability to join dissimilar materials easily and effectively. In turn, allowing electric vehicles to use a combination of lighter-weight materials in their design.
As a result, electric vehicles are safer, more efficient, and more desirable.
But that's not the only way in which adhesives can contribute towards a sustainable future. They are crucial in developing technologies to tackle climate change.
Take wind turbines for example. Adhesives are critical to their design. Composite materials are the primary material in the design of the blades. As we already mentioned, you won't want to use mechanical fixings for joining composites.
It's why the blades are entirely bonded together. Wind energy would be very difficult to implement without the help of adhesives holding it all together.
Other renewable energy sources like solar panels use a lot of adhesives in their design too.
But what about the storage of that energy?
Batteries are going to be one of the most critical elements in a sustainable society. Battery manufacturers are increasingly using bonding in their battery designs.
Improvements in technology are constantly relying on adhesives in design. It's becoming increasingly clear that a sustainable society is going to rely heavily on adhesives and bonding.
Society, as we know it today, is a lot more dependent on the strong bonds formed by adhesives than most people realise. The foundations of the future are even more dependent again.
Why you need to make sure you have the right adhesive
You will have learned about adhesives' crucial role in lightweighting vehicles. You will then have learned that adhesives also play a big role in the much larger picture of a sustainable future.
But which adhesive can help you get set up for success? What is the right adhesive for your application?
These are all questions we regularly recieve here at Forgeway. We manufacture adhesives and help companies solve their bonding challenges.
There is no single answer to these questions. The answer will always be 'it depends'.
Should you want the help of an adhesive expert from Forgeway, you can get in touch with a member of our team. One of the experts will get in touch to assist you.
If you want to learn more about how you can choose the right adhesive, we have several resources available to help you. Click the button below to read about how you can find the right adhesive for you.