Panel bonding adhesive vs welding: Which is the best method?
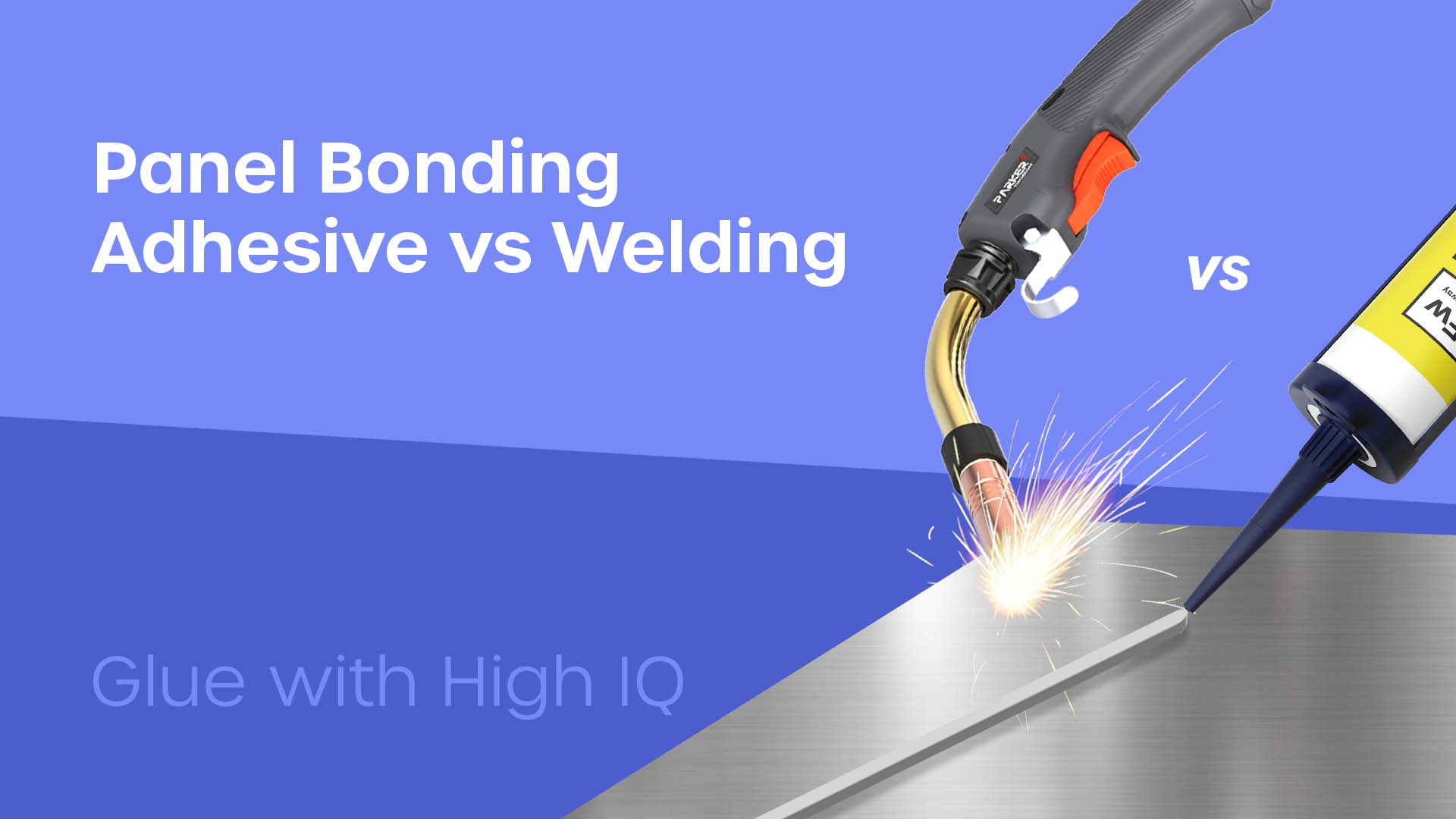
So you’ve reached the point where you are deciding which method is best for joining panels. You’re a bit stuck. You don’t know how to decide the best method.
Here at Forgeway, we often get asked which method is best for joining panels. We’ve been manufacturing industrial adhesives for over 25 years. We know that no method is the perfect solution.
When industrial manufacturers ask us this question, we always say the same thing. It comes down to what you want from the application.
This article will help you break it down into each category so you can decide which method is best for you. By the end of the article, you will have a good idea of whether you should use a panel bonding adhesive or welding.
What’s the difference between a panel bonding adhesive and welding?
Before you can decide which method is best, you need to know what each method actually consists of.
As the name suggests, a panel bonding adhesive is a structural adhesive designed specifically for bonding panels. Although you can use it for other applications too, its main purpose will be for bonding panels.
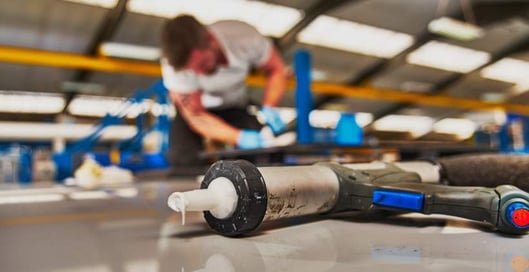
It will come as a two-component structural adhesive. You will need to ensure you have the right application equipment and ensure you have prepared the surface properly.
Whilst the bonding process isn’t simple, most operatives will be able to pick it up with the right training.
Welding is a method which consists of heating the metal to the point it melts and fuses the surfaces together. Whilst it sounds simple, the art of welding is very difficult and a specialist welder will be required.
Which method has more strength and durability?
Whilst some structural adhesives are fast catching up, welding is the strongest method when joining panels. A panel bonding adhesive isn’t going to have the same strength as welding.
However, when it comes to durability, you have to consider more than just strength. A panel joint will have to withstand external factors in order to maintain its strength over time.
Factors such as dynamic load (joint movement), weathering, and chemicals are all typical examples of factors a panel joint will need to withstand.
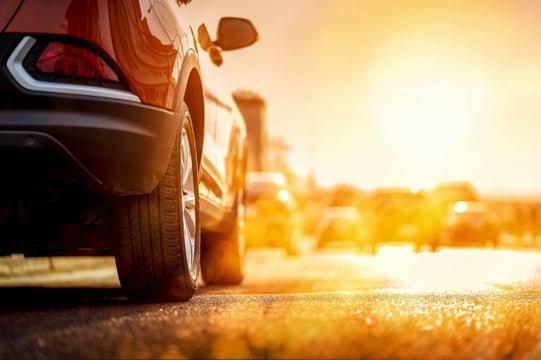
Typically, a welded joint may not have as much resistance to these factors as a panel-bonding adhesive. Panel bonding adhesives can be formulated to withstand these factors.
So if you know the joint is likely to experience a lot of salt-water exposure (such as coastal roads), you could use a panel-bonding adhesive with good chemical resistance.
Welding doesn’t have this level of adjustability. This is why we’d say that whilst welding does create a higher-strength joint, a panel-bonding adhesive is likely to be more durable.
Which method is easier to use?
Using structural adhesives isn’t easy. Two-component systems are particularly difficult. You will also need to ensure the operative has the right equipment (applicator, surface prep tools).
Knowing which tools you require can be a problem too. However, with the right training and equipment, any operative can become a skilled adhesive bonder.
You cannot say the same about welding. For industrial manufacturers, finding a coded welder is becoming increasingly difficult. You can’t train existing operatives to weld as easily as using a panel bonding adhesive.
So if you have access to a coded welder, then welding would be the easiest method. However, using a panel bonding adhesive is usually the easiest method as you won’t need a qualified bonder to use it.
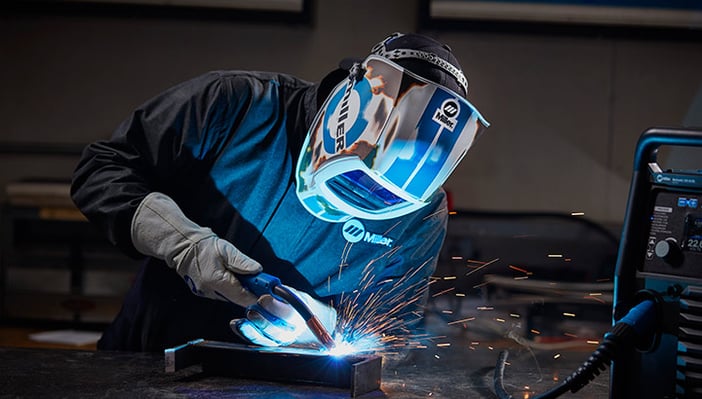
Welding or panel bonding adhesive; which has a better appearance?
Better appearance is of course subjective. However, this likely means ‘least visible’ as the adhesive or weld isn’t what you want to be visible.
In this case, it’s difficult to say which will have a better appearance. Both methods can make themselves quite visible if not undertaken correctly. A skilled welder will be able to make the weld seam barely noticeable.
Equally, a skilled bonder will be able to make the adhesive blend into the joint making it look seamless. But, sometimes excess adhesive can spill out and becomes difficult to remove once cured. This will damage the aesthetics.
The other thing you have to consider is the effect of the heat. Welding distortion can damage metals, leaving marks and even bending the panels.
So, a better appearance is subjective but welding will be less visible if performed correctly. As welding is a more difficult method, it is harder to get a good finish.
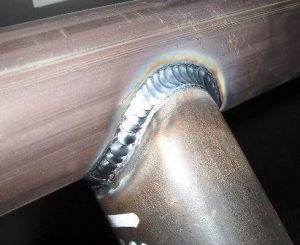
Are panel bonding adhesives less or more expensive than welding?
Panel bonding adhesives aren’t cheap. Welding also isn’t cheap. However, when evaluating cost, you need to take a holistic view of the project. There is more to the cost than just the tubes of adhesive and the cost of the welder.
The reason we have put cost last on this list is that everyone always puts price as the highest priority. Whilst we know this, it’s often difficult to understand why safety isn’t prioritised as high as cost.
You need to be sure that the joining method you use is going to keep the end-user safe. If you aren’t sure about the safety of the joint, but still use that joining method because it is a cheaper method, you put life at risk.
Having said that, a panel bonding adhesive is always going to be cheaper. Even once you have factored in the cost of the equipment and training, panel bonding adhesives will cost less than welding.
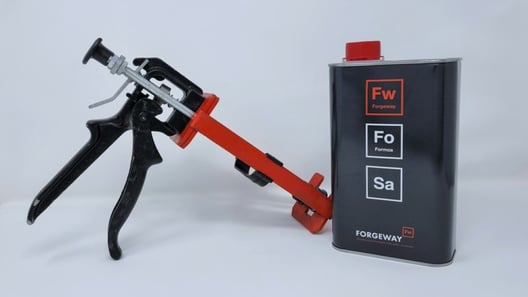
Panel bonding adhesive or welding: Which method should you choose?
Now that you understand the qualities of each method, it’s time to decide which method could be the best choice for you. But we know it’s often not as easy as that.
As adhesive manufacturers, we help companies choose the best method for their application. And no, adhesives aren’t always the best choice. Sometimes, welding is a much better method when joining panels.
It all comes down to you and what you need for your specific application. As we have shown you above, each method will stand out for certain requirements.
For example, if you want a joining method that is more durable, you will likely find a panel bonding adhesive is a better choice. This is because panel bonding adhesives are more versatile.
However, you will have to decide what is most important for your application. From that, you can decide which method is going to be a better option for your application.
You might be stuck though. You might still be struggling to decide which method is best for your application. You can reach out to an expert who will help you discover which method is best for you.
Or, if you’d like to do some more research yourself, read the article below which discusses structural adhesives in detail. It will give you the information you need to get a better understanding of each method and make the choice.
Thomas is the Content Manager here at Forgeway. Thomas' job is to translate the technical jargon from the ivory tower of academia into easy-to-read content that everyone can understand. Forgeway's mission is to answer every question our customers and prospective clients ask, or are apprehensive to ask.