Repeatability in the bonding process: Tips on achieving consistent quality
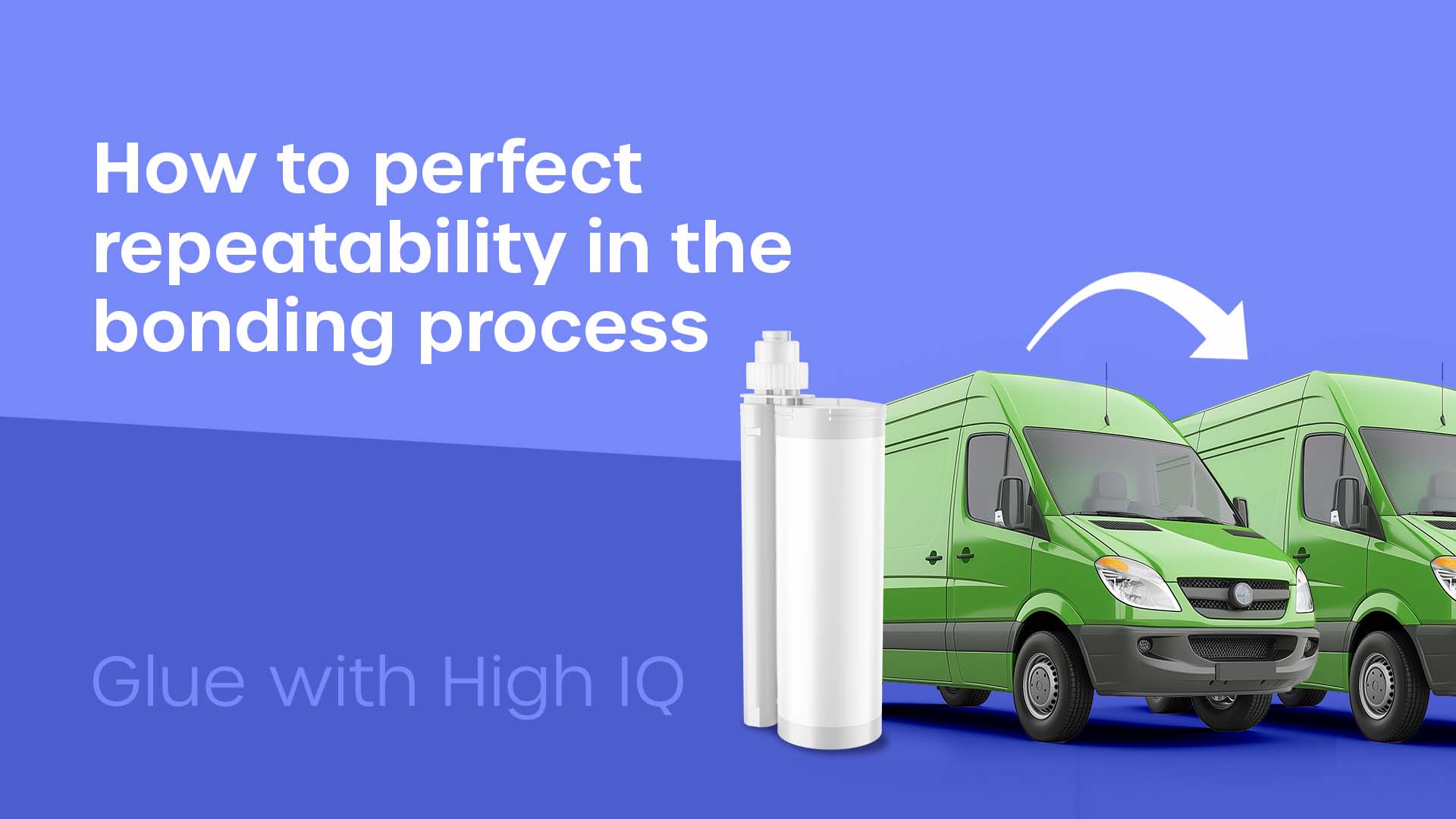
Choosing an adhesive is never easy. You need to consider so many different factors. The adhesive you choose needs to meet the performance expected of it.
But it needs to perform consistently. And consistency isn’t just down to the adhesive you choose. You need to ensure the entire bonding process is repeatable.
Here at Forgeway, we manufacture a range of adhesives. We help manufacturing companies improve the repeatability of their bonding processes.
That’s why we wrote this article. We are going to discuss the topic of repeatability. We want to help you overcome repeatability issues in your adhesive bonding process.
By the end of the article, you will know the five main tips we give our customers to help them create a repeatable bonding process.
The definition of repeatability in the bonding process
A repeatable bonding process is simply having a system in place so you can consistently achieve the same quality of bond. Whilst no two bonds will ever be the same, the ultimate aim of a repeatable process is to consistently make them as similar as possible.
Repeatability means making the bonding process as simple as possible. This article will discuss ways you can simplify your bonding process.
Why is repeatability so important in the bonding process?
Repeatability means you can consistently achieve a quality bond. But why else do you need to make sure your bonding process is simple and repeatable?
There are three main reasons:
- The quality of the end product is also consistent – Poor quality products will result in warranty claims and will damage the reputation of your company. A simple and repeatable bonding process will help you ensure that the quality of each bond is high quality. You will be comfortable knowing that the bond is not the reason for the end product being poor quality.
- You can easily scale up production – A defined bonding process means you can take that process and scale that up to the size you need. So if you wanted to increase the number of products you manufacture, you can take the established process and apply it to the additional products. This will ensure you aren’t reliant on a few employees knowing how things work. Ultimately, you won’t have to worry about the quality of the additional products being compromised.
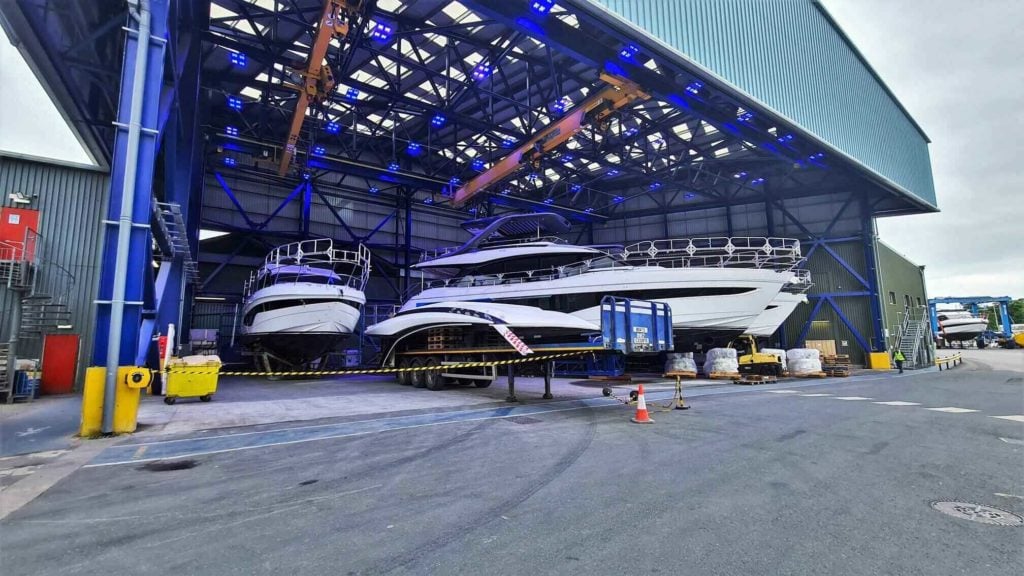
- It is easier to understand and automate – When you have a defined bonding process that is simple and repeatable, other people can pick it up easily. New starters won’t need extensive training to understand the process. And if you want to install machines to do the job instead, it will be easier to implement a pre-defined system than create a new one from scratch.
The factors hindering repeatability in the bonding process
Now you know why repeatability is important, you will want to know what can hinder your process from becoming repeatable. This section will go over the common factors that affect repeatability.
- Insufficient surface preparation – All adhesives require some form of surface preparation to ensure a strong bond is achieved. However, some adhesives require extensive surface preparation (like sanding or priming). The surface preparation process can often make the bonding process more complicated as it can easily go wrong.
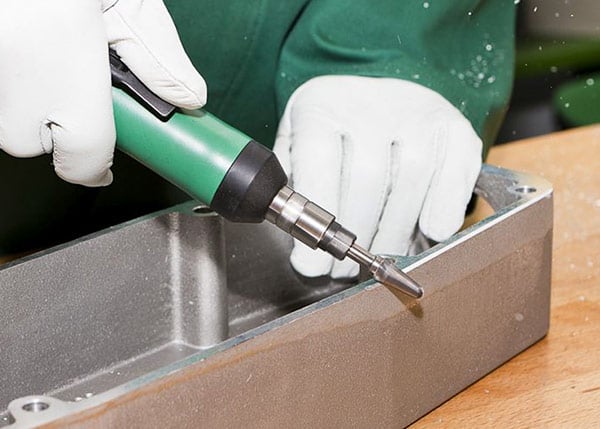
- Incorrect application of adhesive – You have to ensure you have applied the correct amount of adhesive. Too much or too little adhesive will impact the quality of the bond. Without establishing how much adhesive a joint needs, you will struggle to create a repeatable process.
- Inadequate adhesive product – The open time of an adhesive will have the biggest impact on the repeatability of the bonding process. When the open time is too short, you will struggle to put the substrates in place before the adhesive starts to cure. This makes it difficult in ensuring the bonding process is repeatable and simple.
- Poor supply chain – When you have a poor supply chain, you may have to replace products if they are in short supply. Changing substrates can affect the adhesive’s performance. This inconsistency in the adhesive’s performance (due to the changing substrates) will obviously impact the quality of the bond.
- Fluctuating temperatures – The temperature of the surrounding area always affects the cure time of adhesives. Both 1k and 2k adhesives are susceptible to fluctuating temperatures. 1K adhesives are usually more susceptible though. The temperature will affect repeatability as the adhesive will take longer to cure on some days than others if you don’t regulate the temperature.
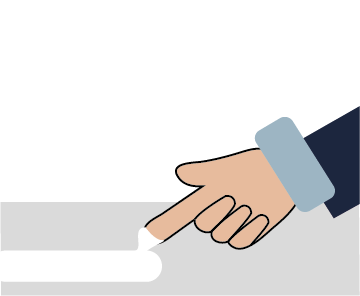
Tips on improving repeatability in your adhesive bonding process
All of the factors above become a problem when you don’t have control over them. But there are ways to control them. This section will go over how you can control those factors and improve repeatability.
Make sure the surface preparation is fool-proof
Whilst this is easier said than done, there are ways you can systematise this process. If you are using a primer or surface activator, some variations have UV ingredients included. This means you can shine a UV light on the substrate which will show up if there is sufficient coverage.
The other method is to use an effective and consistent surface preparation method. Some methods of surface treatment (like sanding) are inconsistent. The more time and money you spend on choosing the right surface preparation method, the more likely you will create a repeatable bonding process.
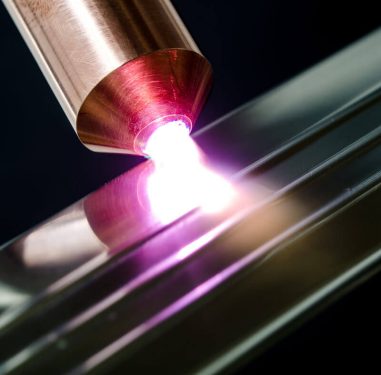
Establish a bond-line thickness
Establishing a bond-line thickness is the best way to control the amount of adhesive you use on the joint. The bondline thickness will ensure you know how much adhesive there should be in the joint. It will give you the ability to ensure each joint has the same amount of adhesive.
It is the most effective way of controlling how much adhesive you should apply.
Make sure you have the correct adhesive
You’ll want to have an adhesive that doesn’t have a very short or very long open time. An open time that is too short will not give you much time to put the substrates in place. When you are constantly rushing to put everything in place, you are more at risk of doing something wrong. Repeatability is more difficult.
Whilst an adhesive with a long open time will not affect repeatability, it can affect the throughput of your manufacturing process. It will take longer for your structure to reach handling strength. You will have more ‘work in progress’ when using an adhesive with a longer open time.
You need to choose an adhesive with the perfect length of open time.
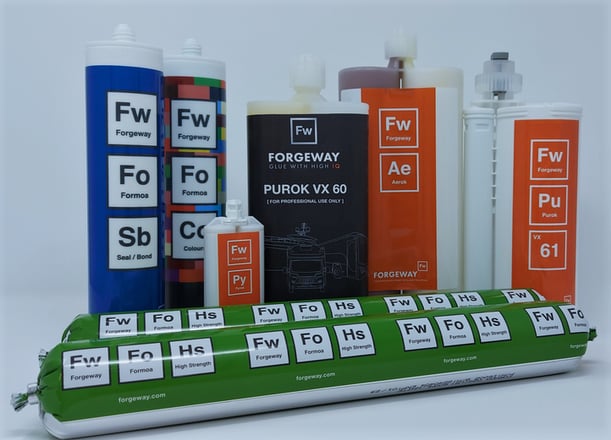
Ensure you have tested all new substrates
Because supply chains are so unstable, you will have to look at alternative substrates at some point. The key thing to remember here is to test the substrate before using it in production. If the adhesive still performs to its usual standard, the new substrate will not affect repeatability.
However if the adhesive doesn’t perform to its usual standard with the new substrate, you will need to look at alternative adhesive options.
Don’t expose the adhesive to harsh temperatures
We always recommend storing adhesives between 5℃ – 25℃ to maintain the performance. Having the temperature above 25℃ will dramatically speed up the cure. Whereas having the temperature below 5℃ will decrease the cure speed.
There are several different measures you can take to store the adhesive in the correct environment. But by ensuring the adhesive’s temperature remains stable (between 5℃ – 25℃), you will not have to worry about the adhesive’s performance. This will make the bonding process consistent and repeatable.
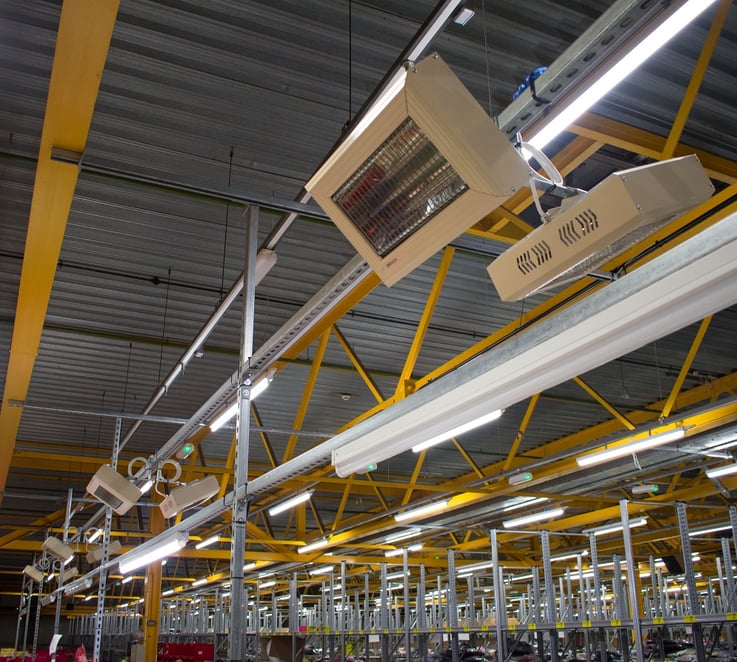
Introducing a standard procedure will give you control over your bonding process
With all of those tips above, you will have learned that you need to take control over the factors that can hinder repeatability. But the difficulty most companies face is implementing that control.
Here at Forgeway, we know the importance of implementing a repeatable process. But we also understand how difficult it is to take control of the factors hindering repeatability.
That’s why we always recommend implementing a standard procedure for your bonding process. There are several standards that you can follow which will give you guidance on how to take control.
DIN 6701/DIN 2304 are German standards for the bonding process. They will help you take control of your adhesive bonding process. We have organised a webinar that will help you understand these standards.
If you are looking to increase the repeatability in your bonding process, we thoroughly recommend you look at becoming DIN 6701/2304 accredited. Whilst the individual tips we outlined above will also help increase repeatability, they don’t take the hollistic approach required to ensure your bonding process is repeatable.
To find out more about the webinar, you can click the link below.
Thomas is the Content Manager here at Forgeway. Thomas' job is to translate the technical jargon from the ivory tower of academia into easy-to-read content that everyone can understand. Forgeway's mission is to answer every question our customers and prospective clients ask, or are apprehensive to ask.
Topics: