Surface treatment for adhesive bonding: What is it and do you need it?
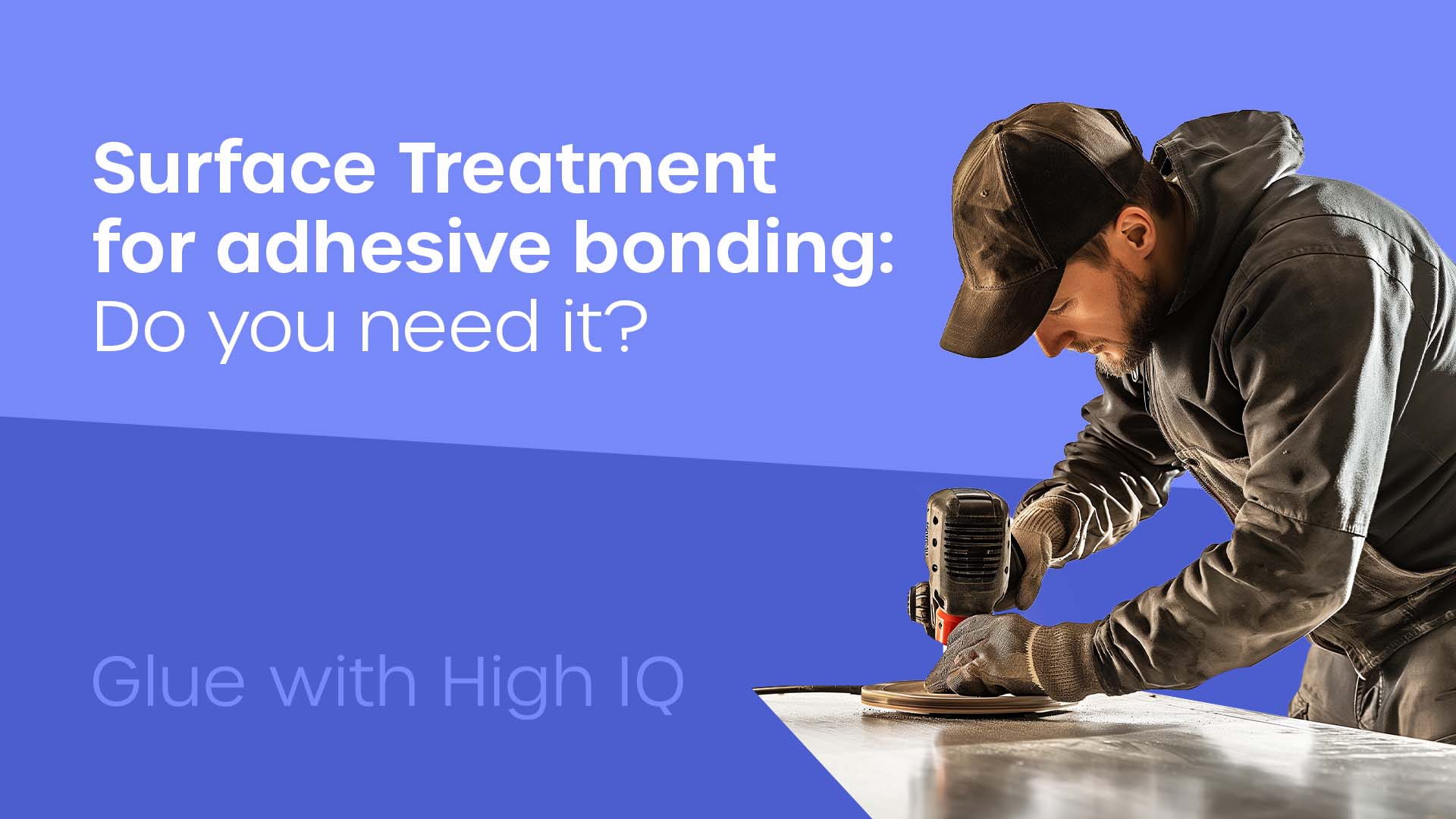
When it comes to bonding, you may need to prepare the surface to achieve optimum performance from the adhesive. But how can you tell what surface preparation is needed (if it is even needed at all)?
Here at Forgeway, we manufacture over 3000 tonnes of adhesives annually. We know the different surface preparation methods and when you need to use them.
In this article, we will go through why you might need to treat the surface. We will then discuss the different methods of surface treatment. By the end of the article, you will have a greater understanding of the surface treatment methods you need for your application.
Why do you need to treat the surface?
Before describing why you might need to treat the surface, we should explain what surface treatment actually means.
Surface treatment literally means altering the surface of a substrate so it can become a different state.
But what is the point in going to the effort of altering the surface of the substrate? The answer is pretty simple. Some adhesives will not perform effectively if you haven’t treated the surface(s) in some way.
We will list a few examples of where it is essential to treat the surface:
- When trying to achieve a very strong bond (such as with an epoxy adhesive)
- Bonding low surface energy (LSE) plastics (unless using a primerless adhesive)
- When bonding glass with some adhesives (unless using a primerless adhesive)
These are just a few examples of where you would need to treat the surface. But if you are wondering why you might need to treat the surface, it’s simply because the adhesive will almost always achieve a stronger bond with some form of surface treatment.
If you aren’t sure whether your surface is likely to cause bonding problems, watch the video below to find out.
What are the different methods of surface treatment?
So now that you have established that surface treatment will benefit your application, you want to know the different surface treatment methods. This section goes over the methods and why they are important.
Removing contaminants from the surface
Otherwise known as ‘degreasing’, this method involves wiping the surface clean to remove dirt and contamination from the surface.
The cleaning process typically involves using a lint-free cloth with a non-invasive cleaning solution (non-invasive means anything that doesn’t impact the adhesive’s performance).
When using MS polymer adhesives, you can use is surface activator to degrease the surface and promote adhesive performance.
The main issue with this preparation method is the fact that it isn’t very comprehensive. It will rarely clean all the contamination from the surface. You will not remove all types of contamination just by wiping the surface.
Wiping the surface also isn’t enough to prepare the surface for bonding problematic materials like LSE plastics unless you are using a primerless LSE bonding adhesive.
Whatever structural adhesive you are using, we would always recommend ‘degreasing’ the surface before bonding.
Methyl methacrylate adhesives are the only adhesives that don’t need this surface preparation method. However, wiping the surface clean will only help their adhesion.
Abrading the surface
Mechanical abrasion (mostly known as sanding) is a very common method of surface treatment. Abrasion kills two birds with one stone. It removes dirt and contamination from the surface, and it increases the bonding area resulting in increased adhesive performance.
The previous method of wiping the surface will remove some dirt and contamination. Abrading the surface will go to the next level and removes most contamination.
Some materials (like aluminium) have an oxide layer on the surface. This can interfere with some adhesives’ ability to form a strong bond.
Wiping the surface will not be enough to remove that oxide layer. Sanding is probably the most cost-effective method of removing any heavy contamination. If you have tried wiping the surface and it didn’t remove the contamination, sanding may the best option.
Abrading the surface is not always ideal though. You cannot use it on materials that are being used for aesthetic purposes. The abrasion will damage the aesthetics.
Most abrasion techniques are inconsistent too. Sanding – in particular – will never be consistent. For a start, humans are unable to apply a consistent amount of pressure at a consistent speed. This inconsistency means the surface will have an uneven amount of abrasion.
And even if you use a robot to remove human deficiencies, the sanding pad itself will wear. Once again, this means that some areas will have more abrasion than others.
Abrasion is cheap and effective, but inconsistent.
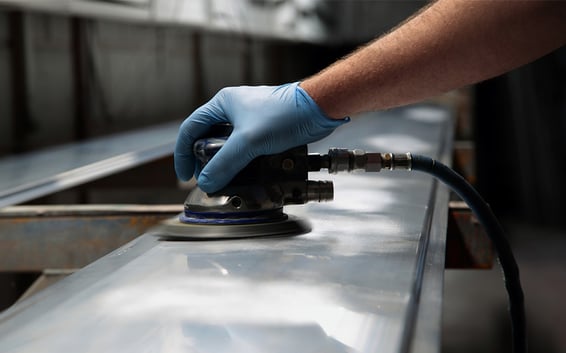
Chemical pretreatment
This surface preparation method takes things up a level further from abrasion. Chemicals (usually some form of acid) are used to change the physical and chemical properties of the surface.
One technique of chemical pretreatment is ‘chromic acid etching’. This is where the acid creates an oxide layer on the surface. This results in a larger surface area with increased surface energy. Ultimately, making the surface easier to bond to.
Most chemical pretreatment techniques leave some type of layer on the substrate’s surface. This added layer makes it easier for the adhesive to form a strong bond.
Typically you would use chemical pretreatment for metal bonding applications. But the chemical pretreatment process is often difficult, costly, and time-consuming. This is because you can only treat one substrate at a time which can take a long time if you have a large number of substrates to treat.

Mechanical pretreatment
There are a few different mechanical pretreatment techniques you can choose from. Nonetheless, they all share the same aim; to change the surface’s reactivity and modify it for better adhesion. The different techniques are:
- Flame treatment – The surface is exposed to a gas flame which oxidises the surface and increases surface energy. This can be problematic with some plastics as the flame can deform the surface.
- Corona treatment – The surface is exposed to an electric discharge (much like an electric shock). The heat oxidises the surface and increases surface energy much like flame treatment. The electric discharge can be inconsistent though.
- Plasma treatment – The plasma treatment machine compresses air into a vortex and discharges a high voltage creating a plasma jet. This plasma jet then cleans the surface and adds covalent points for the adhesive to bond to. Plasma treatment is widely regarded as the most consistent method of treating the surface.
All mechanical pretreatment methods clean the surface in a much more thorough way than most other methods of surface preparation. They also leave a surface for the adhesive to bond to.
Plasma treatment – in particular – has become one of the more popular methods of surface treatment. Particularly in the automotive industry, plasma treatment’s versatility and consistency are the cause behind its rise in popularity.
You would commonly use mechanical pretreatment methods for plastics and some metals that are difficult to bond.
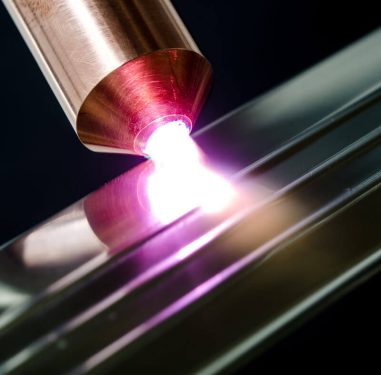
Priming the surface
Primers come in a liquid form and you would apply them by wiping them onto the surface of the substrate.
Priming the surface effectively creates a ‘new’ surface for the adhesive to bond to. The new surface is guaranteed to form a strong bond to the adhesive. You can get either solvent-based or solvent-free primers.
Primers are typically for situations where the surface is difficult to bond. Low surface energy (LSE) plastics and glass are two examples of where most people would use a primer to achieve a strong bond.
There are – of course – specialist adhesives that can bond to LSE plastics and glass without the need for a primer. However, these adhesives would be more expensive than if you were to use a primer and a ‘normal adhesive’.
So priming is a cheap and easy way to achieve a strong bond. However, it does have a few drawbacks. Inconsistency is once again a significant problem with this surface preparation method. It is difficult to ensure the primer has a consistent layer all over the surface.
You also need to be careful about whether the primer is compatible with the adhesive, and the substrate. You may find that the primer doesn’t form a bond with the adhesive or with the substrate. Testing the products before putting them into production will allow you to check compatibility.
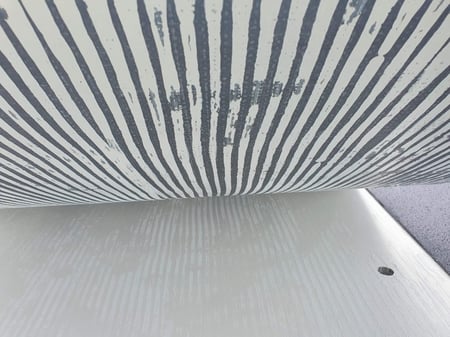
Which surface treatment method do you need?
So after reading through all the different methods, you need to determine which one is best for your application. And the answer is never simple. There is never one perfect method of treating the surface.
Here at Forgeway, we are specialists in adhesives. We will advise you on the best method of treating the surface before purchasing our adhesive. But without knowing your specific application, it’s difficult to know which method is best for you.
We would say that you should always thoroughly clean the surface before applying any adhesive at the very least.
If you aren’t prepared to fork out large sums for extensive surface preparation methods, but you still want to ensure the bond is strong, we would advise you to look at using a primer or abrading the surface.
If you want to spend even more money on ensuring consistent surface preparation, then we recommend you take a look at plasma treatment.
Nonetheless, recent technologies mean you can get adhesives that require minimal surface preparation. We would always recommend these as they mean you don’t have to worry about inconsistent surface preparation causing bond failure.
If you want more information about these adhesives, reach out to a bonding expert or click the banner below to read more about them.
Thomas is the Content Manager here at Forgeway. Thomas' job is to translate the technical jargon from the ivory tower of academia into easy-to-read content that everyone can understand. Forgeway's mission is to answer every question our customers and prospective clients ask, or are apprehensive to ask.