The Role of Durability in Adhesive Selection: A Guide for Manufacturers and Engineers
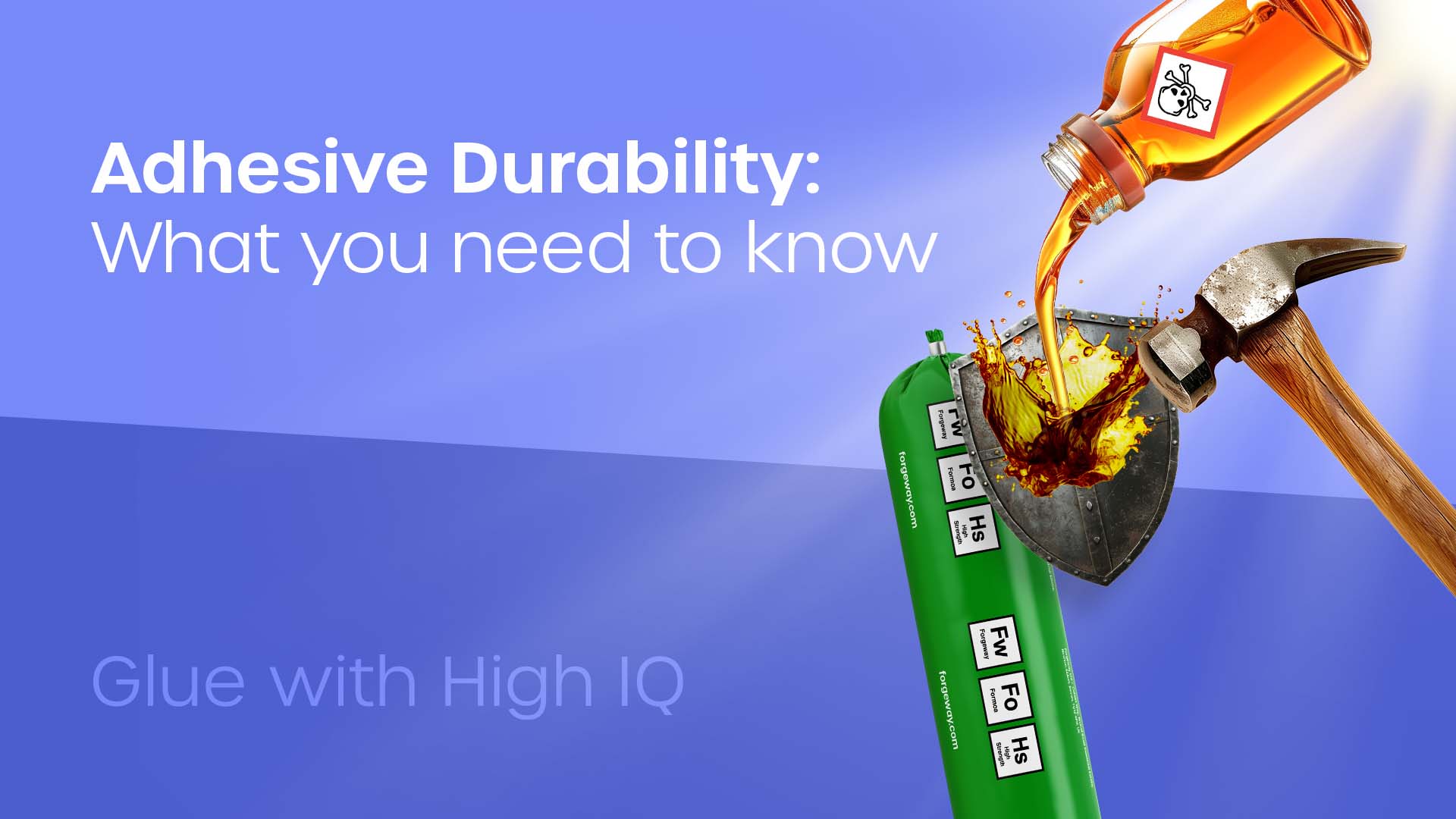
You’re going through the adhesive selection process. You think you know what you’re looking for, but you keep hearing the term ‘durability’. You know that the strength of your adhesive selection is important. But you want how to ensure it has the right durability.
Here at Forgeway, we manufacture industrial adhesives. We have helped engineers and manufacturing companies choose the perfect adhesive for their bond. We believe an adhesive should outlast the total lifetime of the structure it is bonding. That’s adhesive durability.
In this article, we are going to explain why durability is so important and what it means. By the end of the article, you will know why we consider durability to be one of the most fundamental characteristics of an adhesive.
What does durability mean in an adhesive?
Before describing adhesive durability, you should understand the difference between strength and durability. Strength gives you the assurance that the adhesive is strong enough to hold the substrates in place.
If you don’t fully understand adhesive strength, we wrote an article that explains adhesive strength in great detail.
So strength refers to how much force that adhesive can withstand. But durability is different. Adhesive durability refers to an adhesive’s ability to maintain its strength over time.
A lot of people don’t realise that a strong bond isn’t necessarily a durable bond.
An adhesive could face exposure to several things that affect its strength and performance over its lifetime like environmental factors and the substrates in the bond.
Here at Forgeway, we say that an adhesive should outlast the lifetime of the structure it is bonding to.

Why is adhesive durability so important?
Without effectively analysing the requirements of your bond and selecting a durable adhesive, you could be:
- Putting the quality of your products at risk
- Putting the profitability of your company at risk
- Putting lives at risk.
That’s why it’s so important to choose a durable adhesive solution.
Each bond is different. Therefore, it’s important to analyse the specific requirements of your bond before deciding what characteristics you’ll need from your adhesive to ensure it is ‘durable’.
A typical example of this is when a bond requires impact resistance.
Vehicles, boats, and other moving structures will often experience impact throughout their day-to-day lives so will require the bond to withstand that impact and remain durable.
When a bond experiences impact (also known as movement or “dynamic load”), you will need to ensure the adhesive you use has enough flexibility to withstand that impact.
Elongation (aka flexibility) is one of the main adhesive features to judge its impact resistance. When an adhesive has an elongation-at-break score lower than 15%, it will likely not be able to withstand impact and movement and therefore will not have enough durability.
Bonds with heavy movement (like in some vehicles) may require an adhesive to have more than 100% elongation.

The amount of impact resistance required will depend on the application. And you must remember that impact resistance is not the only characteristic that determines an adhesive’s durability.
The next section will discuss the different factors that usually have an effect on adhesive durability.
What factors will impact adhesive durability?
Several factors affect adhesive durability. We’ve already used environmental conditions as an example of how they can affect durability. Now we will describe the factors in more detail.
Environmental conditions can impact adhesive durability
Temperature and humidity are two examples of environmental conditions that can cause adhesive degradation over time. When the adhesive degrades, its performance will degrade too.
For example, high temperatures can cause the adhesive to soften whereas low temperatures can make the adhesive brittle. This makes it more likely for bond failure to occur.
Humidity is a significant cause of degradation as the adhesive absorbs moisture, leading to a loss of strength.
Other conditions such as Chemicals, UV, and Movement can have a large impact on adhesive durability.
With these environmental conditions in mind, you must consider the different climatic conditions the bond will experience in its end use.
Here is an example to help demonstrate the point. After conducting testing, we found that the different climates had a drastic impact on the bond’s durability.
We put the same adhesive with the same application in three different climates.
- In England and Scotland, the adhesive lasted more than 5 years.
- In Northern Ireland, the adhesive lasted around 2 years.
- In China, the adhesive lasted just 6 months.
The moisture and humidity levels in England and Scotland were sufficient for the adhesive to outlast the test. We only conducted the trials for 5 years.
The increased moisture levels in Northern Ireland more than halved the performance of the adhesive. Yes, it’s that much more rainy in Northern Ireland.
The results from the adhesive in China were the most surprising though. The increased humidity and moisture levels meant that it dramatically affected the performance.
This test just demonstrated how much of an impact environmental factors can have on an adhesive’s durability.

Can the substrate affect bond durability too?
The simple answer is yes, the substrate’s properties may also affect the adhesive’s durability. Surface roughness, cleanliness, and surface energy are all examples of properties that could affect durability.
A rough or highly contaminated surface can reduce the bond strength. Even though abrasion is a technique commonly used to improve adhesive, over-abrasion can weaken the bond.
Some substrates (like polypropylene) have low surface energy. When the surface energy of an adhesive is higher than that of a substrate, it will struggle to adhere effectively.
It’s not about the surface of the substrate. The type of substrate material can also affect the adhesive’s performance. For example, plastics and composites have different thermal expansion coefficients than metals.
This can cause differential movement due to the plastic expanding but the metal or composite maintaining its shape. This movement can put stress on the adhesive joint causing it to fail.
Why correct application is critical to ensuring a durable bond
The application method can also affect the adhesive’s durability. For example, if the adhesive is not applied uniformly, it can lead to stress concentration and premature failure.
It’s important to ensure the operator has applied the adhesive to the correct bondline thickness.
Similarly, if the adhesive has not allowed the adhesive to reach handling strength, it can result in reduced strength and durability.
How can you evaluate an adhesive’s durability?
Testing is the best way to evaluate an adhesive’s durability. However, testing isn’t always straightforward. You can either conduct real-life testing (that often takes years). Or you can replicate the bond in a lab.
This decision will be down to you. We always recommend replicating the bond in a lab as this gives the greatest chance to test the bond in multiple situations at a lower cost.
However, you should read our article on adhesive testing to decide which method would be best for you.
Top tip: Before you conduct any testing, you must establish what good looks like. If you don’t, you may enter the ‘forever land’ of ‘testing’.
Establishing what good looks like will ensure you have a goal in mind. It will help you easily establish whether the adhesive has enough durability or not.

What does it mean to replicate the bond in a lab?
When it comes to replicating the bond, there are several tests you can use to evaluate an adhesive’s durability. Lap shear, fatigue resistance, and accelerated weathering are the most common test methods.
Whilst each method is thorough, they won’t always be able to replicate the exact real-life conditions. And you may find that conducting these test methods is time-consuming and expensive.
However, we would say that these testing methods will give you the best chance to evaluate an adhesive’s durability without putting the end product out to test.

What does real-life testing mean?
Real-life testing is much more time-consuming. The criteria for a ‘successful result’ is often that the adhesive outlives the structure it is bonding.
And as some adhesives are used in applications where the expected lifetime of the structure is up to 25 years, waiting to see if you get a ‘successful result’ would be too time-consuming.
Obviously, twenty-five years is not always the expected lifetime of a structure. We know that. But even if the expected lifetime of the structure is six months, it’s still too long to wait.
Ultimately, whether you choose real-life testing or replicating the bond, you will need to conduct some form of testing to evaluate an adhesive’s durability.

What else should you consider after adhesive durability testing?
You now understand the importance of durability. You understand the different factors that can affect durability and you also know how you can evaluate the durability of an adhesive.
But what happens next?
Here at Forgeway, we manufacture industrial adhesives and help companies choose the best adhesive for their application. We know that ensuring an adhesive has enough durability is not easy.
If you are unsure if your adhesive has enough durability, we recommend you test the adhesive to evaluate its performance. You must remember to decide what ‘good’ looks like before starting any testing work.
Whereas, if you have done the testing and established the adhesive isn’t good enough, there are two things you could do.
- Assess whether you can tweak the formulation.
- Look for an alternative adhesive.
If the adhesive’s performance was just below the standards required, we recommend asking the manufacturer if they can tweak the formulation.
However, if the adhesive performed poorly, we recommend looking for an alternative solution.
Reaching out to an adhesive expert from Forgeway will help you find an alternative solution. We aim to provide a solution that exceeds the lifetime of the structure it is bonding.
Or you might not want to speak to anyone. If you’d prefer to find out for yourself, complete the quiz below to help you choose the perfect adhesive for your application.
Thomas is the Content Manager here at Forgeway. Thomas' job is to translate the technical jargon from the ivory tower of academia into easy-to-read content that everyone can understand. Forgeway's mission is to answer every question our customers and prospective clients ask, or are apprehensive to ask.