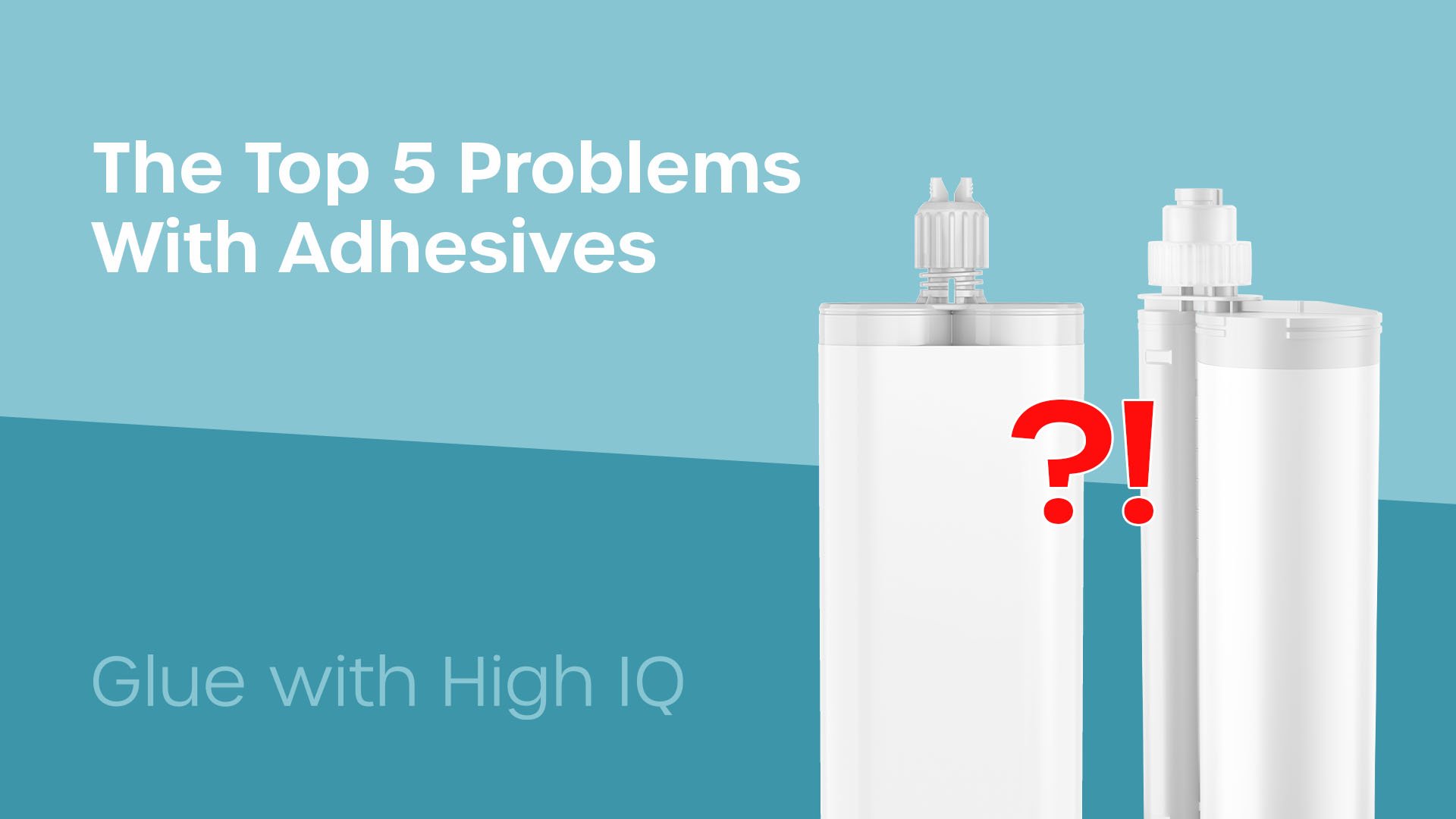
If you’re considering switching to bonding and have done any research on the web, you’ve probably encountered some discussion of the problems associated with bonding commercial vehicles.
The purpose of this article is to address, with full disclosure, five of the most common adhesive problems associated with commercial vehicles…but we won’t leave you there. We’ll also discuss the causes of these problems and how you, the consumer, can avoid them. But in the spirit of full disclosure, we must point out that these “problems” are both very rare and often completely avoidable.
We have helped commercial vehicle manufacturers from all around the world, so we have an intimate knowledge of the good, the bad, and the ugly of bonding commercial vehicles together.
The most common adhesive problems and solutions
- Adhesive failure from debonding (solution: a robust system)
- Slower than mechanical fastening (solution: adopt Forgeway principals to eliminate bottlenecks)
- Adhesives are not as strong as mechanical fasteners (solution: joint design)
- Bonded vehicles are harder to repair (solution: become the manufacturer that knows how to repair your bonded vehicles)
- More expensive than mechanical fasteners (solution: look at the overall cost)
Adhesive failure from debonding
This could be from lack of surface preparation, extension of open time or poor adhesion to substrates. This is a topic that many customers fear when looking at transitioning from mechanical fasteners to bonding. It is inevitable that the commercial vehicle market will evolve to a bonded design – just look at every other automotive/aerospace sector, or even some of the very large German RV manufacturers.
So, how do we eliminate the risk of adhesive failure? The first step is to look for a robust bonding system. All adhesive systems need a cleaning process – some require abrasion process whilst others require primers. Once you have identified a supplier who understands your requirements and has a suitable adhesive system, your team then needs training with written SOPs in place. Process control also needs to be in place – this can be in the form of UV traceable activators etc.
We have often been told that bonding is not as fast as mechanical fasteners. There’s a recent case study comparing the use of adhesives wherever possible and wherever necessary. It takes less than a quarter of the time to build the same vehicle, not only is it faster to build but it is a superior build with a better payload and simply looks better. So how do they do this? Simple – they bond the structural elements the day before (such as side raves, cant rails etc) so these sections have enough strength to be assembled. If you have a panel that needs to be held in place whilst the adhesive cures, consider using a sacrificial double sided tape to hold the panel in place. There may be times when you need to put some screws/bolts in place to allow immediate processing, but these fixings are just a temporary hold.
Adhesives are not as strong as mechanical fasteners.
There are many factors that determine whether this statement is true or not. You can put a hook bolt through a plywood sidewall to get a strong fixing, but in doing so you have drilled a hole in the sidewall, and therefore weakened it. This hook bolt is now a point loading, and any stress on that hook bolt is transferred directly to the sidewall. Had this joint been bonded, the load would be spread over a much wider area, any stress would be largely absorbed by the adhesive, there would be no holes drilled and therefore no weakening. Moreover, there has been a distinctive drive towards composite panels – these panels offer poor anchorage for mechanical fasteners and are designed to be bonded.
I was recently told by a customer that they wouldn’t bond LoadLok because sometimes they have to replace them. Their biggest concern was that if it was bonded, there would be no way to remove it.
So, I bonded a section to a sidewall and left it to cure, I then removed the section using windscreen wire – it took less than 2 minutes. There are tools and equipment designed to assist you in cutting away bonded components. They also may not have needed to replace the loadlok if it was bonded due to the strength being significantly higher.
Is bonding more expensive that mechanical fastening?
I have covered this in more depth within my costing blog, but to keep it short, bonding does not have to be more expensive than mechanical fastening. The choice of adhesive system, combined with joint design and substrates could give you a finished product with greater desirability therefore higher product value.
For more information regarding concerns with using adhesives, feel free to contact one of our experts for some non-biased advice.
Topics: