Bonding Powdercoated Materials: Tips and tricks to achieving a high strength bond
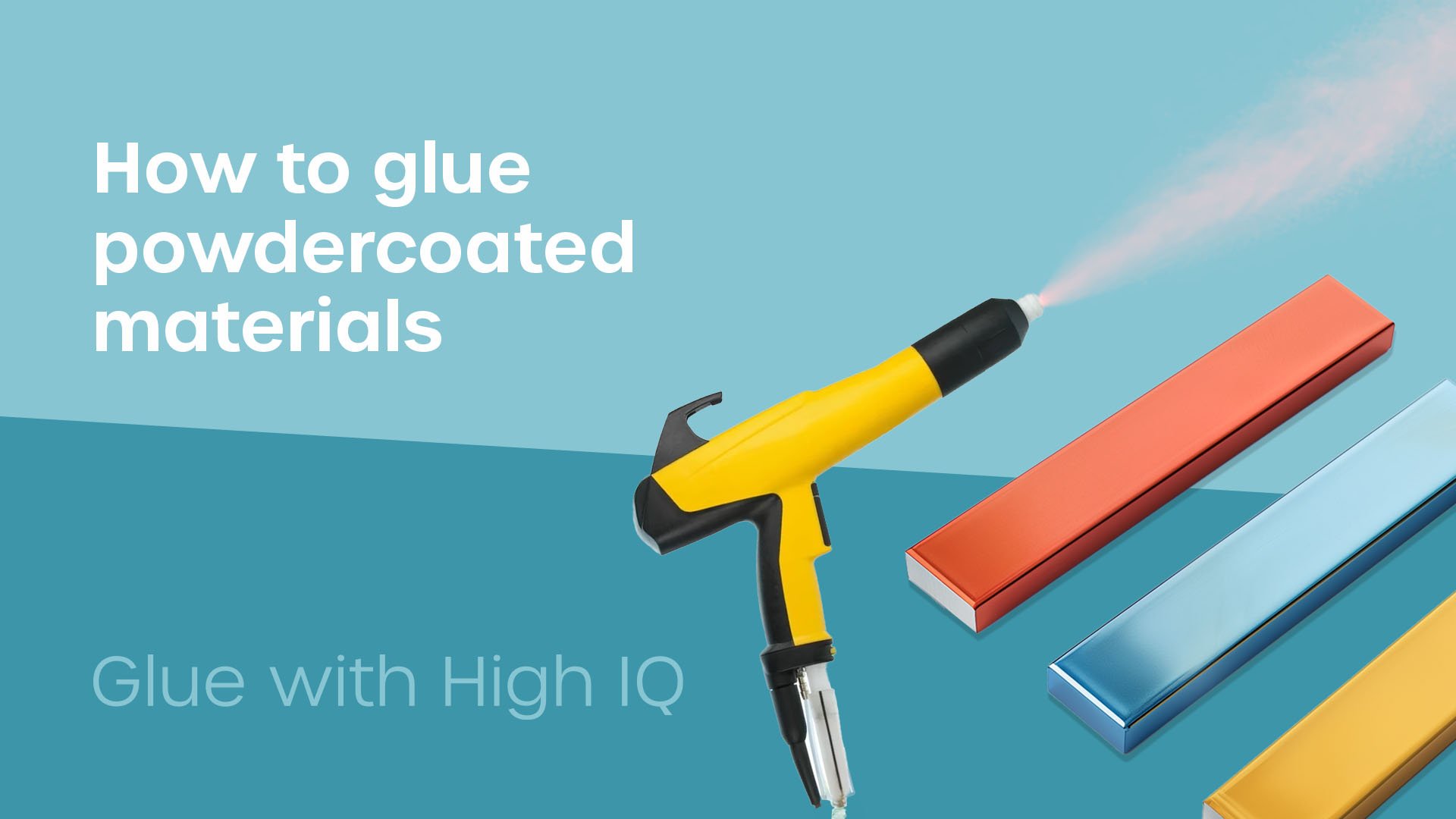
Bonding powder-coated materials is no simple task. Industrial manufacturers who use powder coating in their processes often struggle when it comes to bonding. As they are reliant on the powder coating process, they can’t remove it for the sake of bonding. They need to find a solution.
Here at Forgeway, we manufacture industrial adhesives. We’ve had over 25 years of experience helping solve complex challenges like bonding powder-coated materials. We also know that ‘powder coating’ is broad. The process will differ from manufacturer to manufacturer.
So we wrote this article to help you ensure the powder coating process won’t affect your bond. By the end of the article, you’ll be the expert. You’ll know why powder coating causes problems. You’ll also know what you can do to create a strong bond with powder-coated materials.
Can I bond powder-coated materials?
Yes, you absolutely can bond powder-coated materials with adhesives. Whether you are looking to bond the material before or after the powder coating process makes no difference. It is possible and many of our customers have successfully achieved a strong bond to powder-coated material.
Ironically, the primary problem with bonding powder-coated materials arises because of the benefits of powder-coating itself. These benefits include:
- Corrosion resistance
- Heat and chemical resistance
- Non-wetting (hydrophobic)
But some of these benefits can hinder the bonding process. The additives incorporated in the powder coat usually contain polytetrafluoroethylene (PTFE). This is what makes the powder coat hydrophobic. It reduces the surface energy and creates a hydrophobic surface.
Coincidentally, Low surface energy materials are very difficult to bond. Therefore, powder coating a surface will reduce the surface energy and increase the likelihood of bond failure.
When bonding powder-coated materials, you have to consider the stage at which you’re going to bond. Are you trying to bond the substrate before, or after you have powder-coated it?
The answer will massively impact what you must do to ensure a strong bond. If you’re bonding before, you must make sure the adhesive can withstand the powder-coating process. If you’re bonding after, you must make sure the adhesive will create a strong bond to the powder-coated surface.
Nonetheless, don’t let that put you off. Despite what some ‘experts’ will tell you, it is totally possible to bond powder-coated materials. You just need to know how.
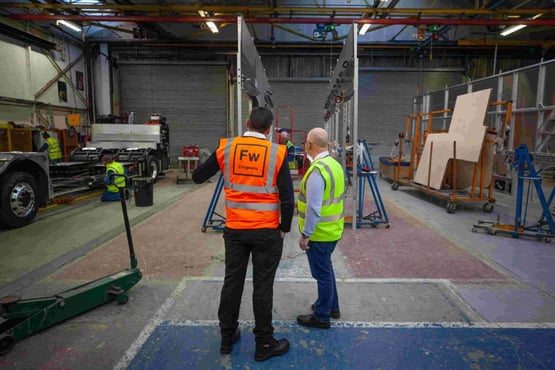
How can I ensure a strong bond before putting the material through the powder coating process?
When bonding substrates before they go through the powder-coating process, we’d usually say that you need to find an adhesive that doesn’t drop below handling strength (0.3MPa) when exposed to the temperatures of the powder coat oven (usually 200℃) for the entire length it will be in the oven (usually 30 minutes).
Simple? All you need to do is find an adhesive that doesn’t drop below 0.3 MPa when exposed to 200℃ for more than 30 minutes. Now your bond will remain intact through the powder coat process. Right?
If only it was that simple.
Those specifications will massively depend on your specific powder coating process. Each powder coating process is different. You’ll have to evaluate your specific application to come up with the correct specifications.
There are three main things you need to consider:
- Can the adhesive withstand the temperatures in the powder-coat oven?
- How long will the adhesive be in the powder-coat oven?
- How much stress is on the adhesively bonded joint?
It’s vitally important that you consider each point carefully. You run the risk of bond failure if you don’t consider these three points. We’ll now break these down to help you ensure your bond will not fail.
Can the adhesive withstand the temperatures in the powder-coat oven?
Most powder coating processes require post-application heat-curing. Typically, the material will face exposure to temperatures between 200℃ – 250℃ for 30 minutes.
(Some applications can see lower or high temperatures or longer periods.)
Nonetheless, powder-coat curing ovens usually need to face exposure to temperatures around the 200℃-250℃ mark for around 30 minutes. So if you’re bonding the materials before the powder coating process, you’ll need to ensure the adhesive can withstand the temperatures in the curing oven.
But what does ‘withstand’ really mean?
Disclaimer: We’ve conducted a deep dive on adhesive temperature resistance in a separate article. It breaks down what adhesive temperature resistance really means.
Companies often don’t do enough research at this point. They’ll do the work and get to the point where they know the adhesive needs to have temperature resistance.
They’ll even analyse the adhesive’s technical data to determine its maximum temperature resistance. In theory, if the adhesive’s maximum temperature resistance is lower than the temperatures in the powder coating oven, the adhesive will fail. Right? Not necessarily.
Companies will need to conduct further analysis. Typically, just analysing the adhesive’s maximum temperature resistance will not give you an accurate idea of an adhesive’s performance in a powder-coating oven.
How long will the adhesive be in the powder-coat oven?
The adhesive’s maximum temperature resistance doesn’t give an accurate idea of its performance when putting it through a powder coat. It’s also important to remember how long it will face exposure to elevated temperatures.
As we mentioned, powder-coat ovens will typically last around 30 minutes at around 200℃. Nonetheless, this time can vary. Your powder-coating process may be different.
The length of the powder-coat process is important to evaluate because the amount of time an adhesive can withstand elevated temperatures will also vary.
An adhesive’s strength will drop over time. When exposed to elevated temperatures, the adhesive will lose that strength faster. But how fast it loses strength will again vary depending on the adhesive type.
So, if you know how long the powder-coat process lasts and you know how long your adhesive’s max temperature resistance lasts, you can evaluate whether your adhesive will be able to survive the powder-coating process.
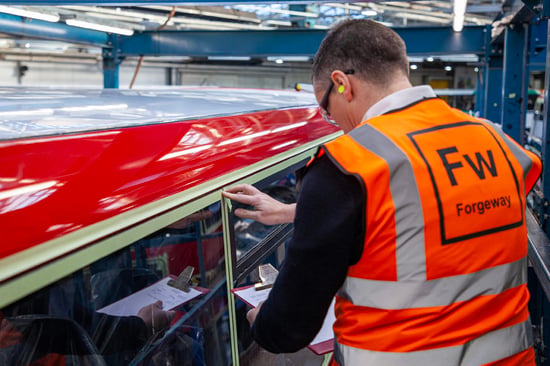
Let’s use an example to help explain this.
You’re using an adhesive that has a maximum temperature resistance of 200℃. Your powder-coating oven also reaches temperatures of 200℃. On paper, this means your adhesive will withstand the powder-coating process. However, your powder-coating process lasts 45 minutes. The adhesive was only tested for 15 minutes.
Therefore, the data fails to show whether the adhesive can withstand 200℃ for 45 minutes. It is entirely possible that the adhesive will not retain its strength for that length of time.
In summary, it’s not enough to just evaluate an adhesive’s maximum temperature resistance. You also need to evaluate how long it can last when exposed to elevated temperatures.
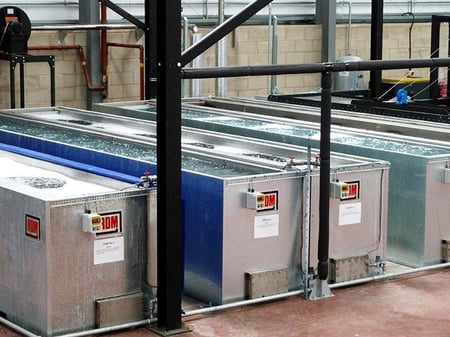
How much stress is on the adhesively bonded joint?
When evaluating an adhesive’s suitability for powder-coating, the most important thing to remember is the absolute minimum strength required of the adhesive to avoid failure. This may seem a strange way to look at it. But don’t worry, we’ll explain what we mean.
You should know the minimum strength required before you can analyse temperature resistance. This will help you determine whether your adhesive can withstand the heat-curing process.
Let’s use an example to help explain. Let’s say your bond needs an adhesive that has a minimum strength of 1 MPa to hold the materials in place. This means you must ensure the adhesive’s strength doesn’t drop below 1 MPa when exposed to the temperatures of the powder oven (usually 200℃) for the length of time it will experience those temperatures (usually 30 minutes). If the adhesive’s strength drops below 1 MPa when exposed to temperatures of 200℃ for 30 minutes, it’s likely the bond will fail.
Usually, we recommend ensuring the adhesive doesn’t drop below handling strength when exposed to powder coat ovens. We’d say that an adhesive’s handling strength is 0.3 MPa. Obviously, some applications will require the adhesive to be of higher strength. Typically, 0.3 MPa is sufficient.
So that’s why we recommend finding an adhesive that has greater strength than 0.3 MPa when exposed to temperatures above 200℃ for more than 30 minutes. But the actual numbers for your application may fluctuate depending on the strength required.
If your adhesive doesn’t meet these requirements, it’s still possible to clamp or ‘peg’ the substrates in place during the powder-coat process. This will ensure the bond will remain intact while exposed to high temperatures. And as the adhesive’s strength will return when it reaches ‘normal’ temperatures, you can remove the clamps after the powder coating process.
Click the button below to read more about determining the strength required of an adhesive. It will help you establish how strong your adhesive needs to be.
How can I ensure a strong bond after putting the material through the powder coating process?
You’ve already applied the powder coat. You’ve put the material through the curing oven. The powder coat is now firmly applied onto the material’s surface.
Now you want to bond that material. As we mentioned earlier in the article, a powder coat usually contains ingredients that create a hydrophobic surface.
The hydrophobic surface will often repel the adhesive. This is because the surface energy is usually lower than the surface energy of adhesives; preventing the adhesive from wetting out. We’ve written a separate article on why surface energy affects adhesion. Or you can watch the video below explaining how to tell if your substrate is bondable.
To put it simply, you’ll often struggle to achieve a high strength bond straight onto a powder-coated surface.
There are two main ways to overcome these adhesion issues:
- Prepare the surface extensively. This involves abrading, priming or solvent-cleaning (or all three) the powder-coated surface. After you have effectively removed the hydrophobic powder coat, you will be left with a bondable surface. We always advise at least abrading and solvent-cleaning if you are willing to prepare the surface.
- Use a specialist adhesive. This process involves using an adhesive that can ‘cut’ through any powder coat. Acrylic adhesives (aka methyl methacrylates) are the most common adhesive types that can cut through powder coat. In some cases, you may require a specialist adhesive (like Purok VX90) which is designed for bonding difficult surfaces. Make sure that you properly test the bond to ensure it is strong enough before you use it in the end application.
Whichever method you choose, we thoroughly recommend conducting testing to ensure the bond is strong and durable. The testing should highlight if the bond will remain strong over the lifespan of the structure it is bonding.
For example, if you’re bonding a commercial vehicle, you’ll want to test the bond in accelerated weathering testing to see if it can withstand real-life conditions and retain its strength.
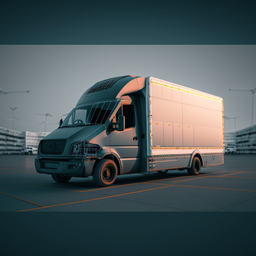
How can I be sure the powder coat bond is strong and durable?
You’ve read the article. You understand the challenges associated with bonding powder-coated materials. Now you want to put it into practice. But how?
As adhesive manufacturers, we often get asked for help with this exact application. We find the best way to solve this problem is by continuous testing. Whatever solution you decide to explore, thorough testing throughout will help you evaluate whether the bond is strong enough.
If you’re looking for a solution that will bond the materials before powder coating, we recommend reading our articles on strength and temperature resistance to understand what adhesive you’ll need.
In our opinion, one of the best solutions is to simply clamp the substrates in place while it goes through the powder coating process. Or, if you don’t want to use clamps, we recommend finding an adhesive that doesn’t drop below 0.3MPa when exposed to 200℃ for more than 30 minutes.
That sounds complicated. If you’re looking for a quick answer, we recommend you take a look at Formoa 017FE. A lot of companies have achieved a strong bond through the powder coating process with this product.
Or, maybe you want to find an adhesive product that can bond after the powder coating process. In this case, you’ll want to explore acrylic adhesives and the benefits they provide. You can read all about them in the articles we have published.
Nonetheless, if you want to get the help of an adhesive expert, click on the button below. After filling in your details, a member of our team will be in touch to help you solve your problem and achieve a strong and durable bond.
Thomas is the Content Manager here at Forgeway. Thomas' job is to translate the technical jargon from the ivory tower of academia into easy-to-read content that everyone can understand. Forgeway's mission is to answer every question our customers and prospective clients ask, or are apprehensive to ask.