Why does sealant (like silicone) go yellow? Tips and methods to stop it from happening
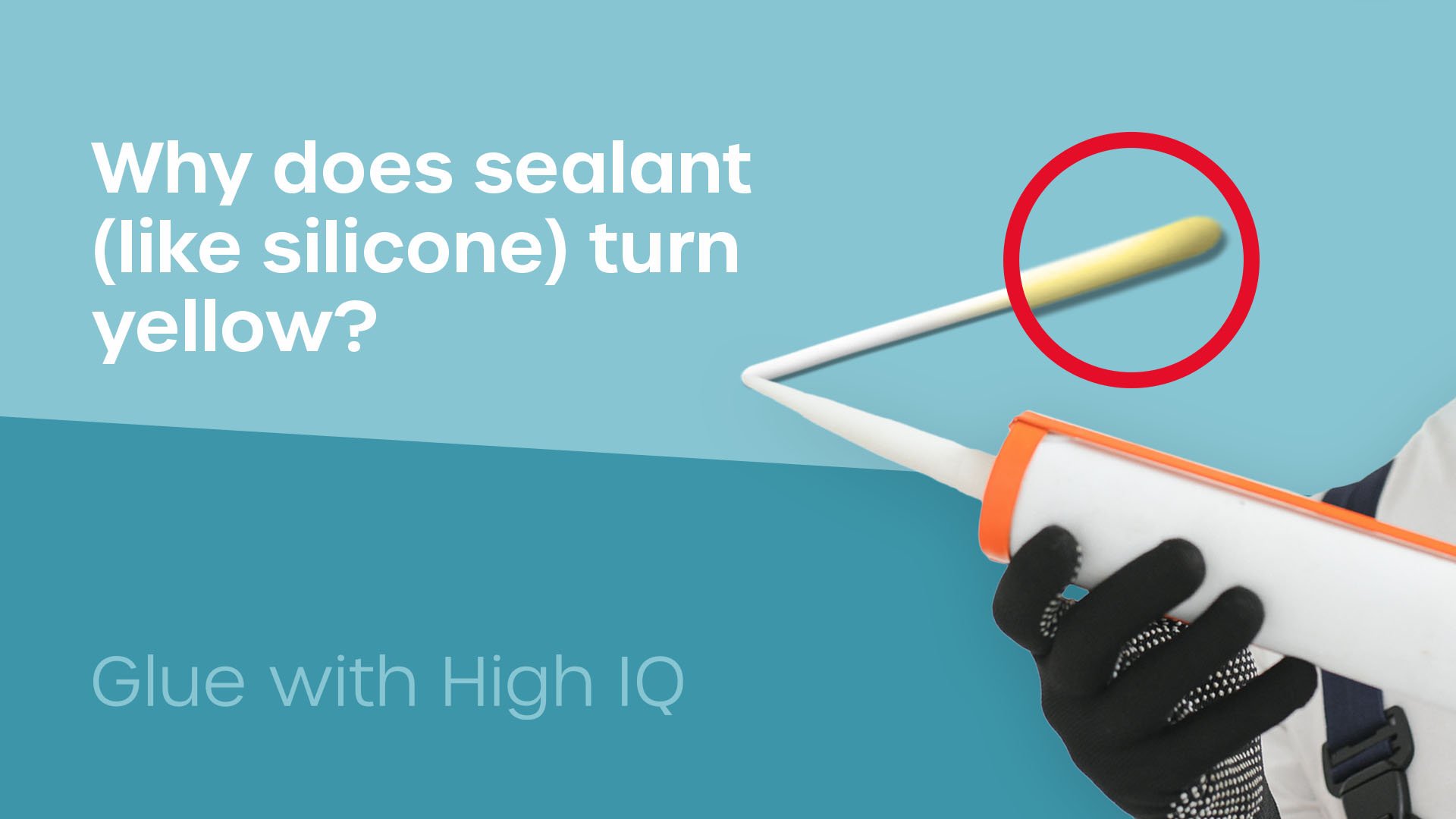
If your sealant or silicone has gone yellow or is in the process of going yellow, don’t worry. It is a common occurrence.
Your sealant is likely going yellow because of exposure to UV radiation. However, there are several other reasons why it could be happening too. There are also a few things you can do to reduce the likelihood of it happening again.
As adhesive specialists here at Forgeway, sealants going yellow is a familiar problem. We often get asked what is happening and whether it is something that should concern you.
In this article, we will discuss what is happening and whether it should be an area of concern.
Once you have finished reading the article, you will know why sealants go yellow and what you can do to stop it from happening.
What’s the difference between silicone and sealant?
Before we dive into the article, we should clarify what sealants actually mean. There is a common misconception that may be confusing.
As the name suggests, a sealant is a type of adhesive that a range of industries would use to ‘seal’ a gap.
Interestingly though, the words sealant and silicone are often used interchangeably and it can get confusing. This is because silicone has become the proprietary eponym for sealants.
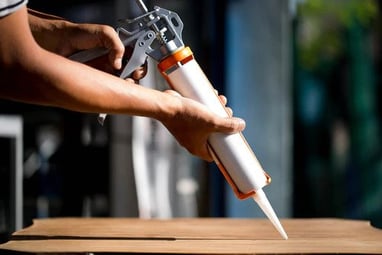
You are probably wondering what in the world ‘proprietary eponym’ means. Well, without getting into the specifics, it’s actually quite simple. Proprietary eponyms are for situations when a type or brand of product has become the household name for that product. A well-known example of this is Coca Cola. Most people would refer to cola-flavoured soda as ‘Coke’.
Silicone is much the same in this situation.
So when people say to use a ‘silicone’, they likely mean to use a sealant. There are three common chemistries that would be used to make a sealant. Silicone is one, hybrid polymer (like MS polymerTM) and polyurethanes are the other two. Sealants based on MS polymer™ are considered hybrids, taking some of the best parts of silicones and polyurethanes. For example, MS-based sealants/adhesives have the strength of polyurethanes with the weathering resistance of silicones.
In this article, we will be referring to them as sealants.
Are you using a sealant or an adhesive?
You may have heard the two terms; ‘adhesives’ and ‘sealants’ but are unsure what they actually mean.
You could consider most adhesives to have sealant properties in that they would be able to seal gaps/joints. However, we would say that something marketed as a sealant may not be strong enough to form a reliable bond between substrates.
So, you can use an adhesive to seal, but we would not recommend using a sealant in place of an adhesive for structural purposes.
.jpg?width=851&height=567&name=Formoa-High-Strength%20in%20Use%201%20(1).jpg)
Now, you’re probably wondering how this is relevant with the problem at hand – ‘why sealants go yellow’. The yellowing problem isn’t isolated to just sealants. Some adhesives are more prone to yellowing than most common sealants.
The reason sealants are typically highlighted in this discussion is because they are almost always visible. Whereas adhesives used for structural purposes are usually hidden.
For the purpose of answering the question around sealants yellowing, I will be using the word sealants. However, everything discussed in this article is relevant for all adhesives unless otherwise specified.
What causes sealant to go yellow?
There are four main culprits that cause the sealant to go yellow:
- UV radiation from the sun
- Heat
- Chemicals (humidity counts as chemical exposure)
- Contamination after application (while it is still wet)
However, of these Four, UV radiation is the most likely to be the cause. In fact, nine times out of 10, UV radiation will be the cause of sealant yellowing.
So what is actually happening for the UV radiation to cause yellowing? Buckle up because this is where it gets technical.
A sealant formulation is made up of various chemical components. Some of these components in the formulation can have chemical structures known as chromophores.
A chromophore is a part of a molecule or chemical structure that is capable of absorbing light and is responsible for an object’s colour.
Chromophores are also extremely susceptible to absorbing UV radiation. Once the chromophores have absorbed that UV radiation, they become ‘excited’ and then form what we would call ‘free radicals'.
Free radicals are extremely reactive species and can react with oxygen to form peroxy radicals. These peroxy radicals then attack the polymer structure and form even more radicals. Creating a vicious cycle.
We call this whole process ‘UV degradation’.
The more technical term is ‘autocatalytic degradation’. The main reason that most people wouldn’t refer to this process as ‘UV degradation’ is because UV radiation isn’t the sole factor causing the yellowing.
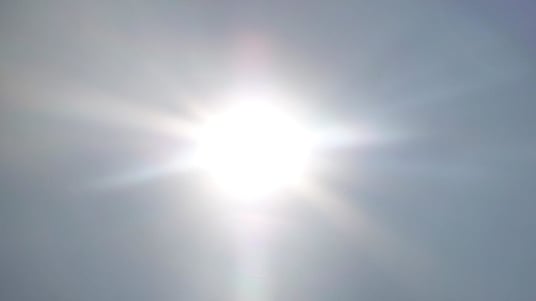
As shown above, there are two other causes. Chemical exposure and heat and both can lead to the degradation of the polymer in the sealant. Heat works in a similar way to UV degradation in that it can cause the formation of radicals. These radicals can then degrade the polymer structure and form smaller chemicals. Some of these smaller chemicals may be chromophores that absorb all colours of light, except for yellow light. This results in the sealant appearing yellow.
Which sealants are more likely to go yellow?
Now you understand what actually causes sealants to become yellow, you are probably not surprised to know that some sealants are more susceptible to yellowing than others.
Different base chemistries can absorb different levels of UV radiation. As an example, polyurethane-based sealants and adhesives that are made up of aromatic-based isocyanates are much more susceptible to yellowing.
This is because aromatic-based isocyanates have a strong chromophore that is more susceptible to autocatalytic degradation (and yellowing of course).
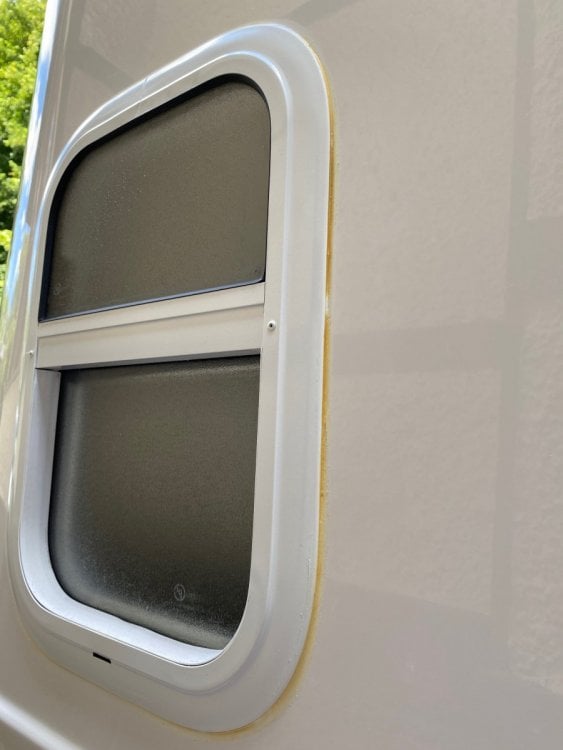
So polyurethane with this type of chemistry will become yellow a lot easier than other types of sealant. However, polyurethanes with aliphatic isocyanates will not be as susceptible to yellowing.
Another common adhesive type is epoxies. Although not often used as a sealant, they may be exposed to the environments that are likely to cause the degradation. Epoxies offer many benefits, including good adhesion, high strengths and good chemical resistance. However, they are very susceptible to UV degradation as their chemical structure contains many chromophores.
Generally speaking most silicones and MS based sealants have very good UV resistance and this is why they are used in so many different applications.
Is sealant going yellow a problem?
Yes, sealant going yellow can become a problem and it’s not just an aesthetic problem either.
The degradation can become so significant it can lead to the sealant chalking and cracking. This is a bigger issue if the sealant is also being used as an adhesive to bond two different substrates for structural purposes. The chalking and cracking could weaken the structural integrity of the bond and eventually lead to debonding of the adhesive/sealant from the substrate.
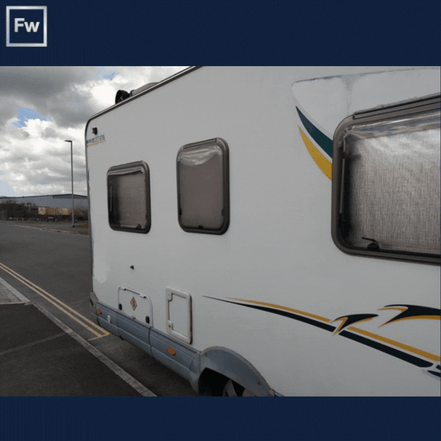
It is difficult to put a number on how long a sealant/adhesive will last. This is because the degradation and yellowing of sealants is a multi-factor issue. So many different climates and environments around the world that can have an effect on the amount/speed of the degradation.
For example, a sealant exposed to the hot, humid and high-intensity UV radiation in Brazil will experience far more stress than a sealant in the United Kingdom.
What can you do to stop sealant from going yellow?
Some good news, there are solutions. Although if your adhesive or sealant has already become yellow, there isn’t much you can do, other than removing and reapplying the sealant.
But if you are planning ahead and want to know how to stop it, you are in luck. Allow me to explain what you can do to proactively plan ahead and stop the sealant yellowing.
There is a simple way you can reduce the threat of sealants going yellow.
Don’t expose it to the harmful conditions that cause it to yellow. You can do this by protecting it. Covering the sealant and ensuring it won’t be exposed to harsh environments will reduce the amount of yellowing and degradation. However, we know that this is not always a feasible solution, particularly if you are using a silicone-based sealant. So, it is likely that the sealant or adhesive will be exposed to some form of harmful conditions.
It could be exposed to UV radiation (sun), heat, or chemical (humid climates count as chemical exposure).
Whatever harmful condition the sealant is at risk of being exposed to (could be all three), it is still possible to minimise the chance of it yellowing.
You may be thinking “how can I stop the sealant from going yellow even though it will be exposed to harmful conditions.”
That’s where specialist adhesives and sealants come into the equation. Most adhesive manufacturers will have incorporated additives into their formulations to minimise UV degradation and oxidation. They may even have test information about the UV resistance of their product.
From this information, you can tell whether the adhesive has the specifications to be UV resistant. Of course, this additional specification could play a considerable factor in the price of that product, but it will be worth the extra cost.
Specialist sealant or protection; which is the best solution for you?
It depends on what you mean by ‘best’. If ‘best’ is the most resistant to UV, then the answer is simple; both.
Using specialist UV-resistant sealants and taking measures to protect them, is the best way to ensure the sealant will not go yellow.
But, we understand you may not always find a way to protect the sealant. This is particularly the case if you are using it on the exterior of something that is regularly exposed to the elements, such as vehicles.
Here at Forgeway, we have helped many companies in different industries choose the correct sealant solution for them. There are always specific requirements and we understand there isn’t a one-size-fits-all solution.
If you would like to read a case study of a situation where we developed a product to help overcome this issue, you can read about it by downloading our e-book and finding the case study on page 159.
Or, if you would prefer to get in touch to discuss your needs, click the link below so an expert can help you through your requirements.
Thomas is the Content Manager here at Forgeway. Thomas' job is to translate the technical jargon from the ivory tower of academia into easy-to-read content that everyone can understand. Forgeway's mission is to answer every question our customers and prospective clients ask, or are apprehensive to ask.