Understanding and Mitigating the Effects of Corrosion in Electric Vehicles

An electric delivery van delivers your parcel. An electric bus takes you around town. An electric car takes you to and from work. Pretty much everywhere you go these days, you will see an electric vehicle of some sort.
But as technology advances, new problems arise. The electric vehicle (or EV) industry has experienced this and it may be affecting you too. Corrosion.
Several EV manufacturers have asked us to help them with their corrosion problems. As industrial adhesive manufacturers, we manufacture adhesives and specialist sealants that can help prevent corrosion.
We didn’t write this article to sell our products though. We want to educate you on this topic so you know how best to prevent corrosion from affecting your EV products.
By the end of the article, you will have a good idea of what corrosion is, why it is happening, and what you can do to prevent it from happening.
What is happening to electric vehicles?
For various reasons (which we explain later), electric vehicles can experience corrosion where ‘normal’ vehicles do not.
This corrosion is the gradual degradation of a material (usually metal) due to electrochemical reactions. Battery, wiring, and other electrical components in particular can experience this corrosion.
Rust is the most common form of corrosion, but it can appear in other forms too (such as filiform corrosion).
Ultimately, electric vehicles are at greater risk of corrosion than combustion engine vehicles.
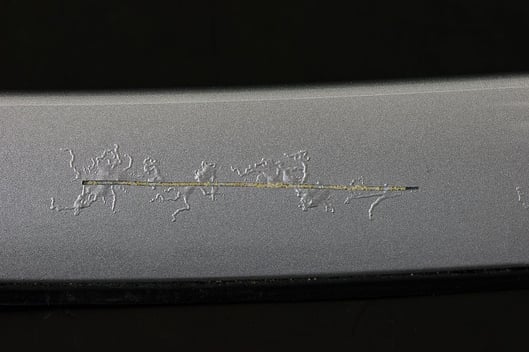
Why do electric vehicles experience corrosion?
You may be wondering why this is all happening to electric vehicles in particular. There is a combination of factors that are responsible for the increased likelihood of corrosion.
The electrification of vehicles means that manufacturers are using more materials that are prone to corrosion. For example, batteries (fundamental to electric vehicles) are increasingly likely to experience corrosion.
Not only does an EV contain more parts (like batteries and wiring) that are prone to corrosion, but the electrification of vehicles has also seen a push to reduce weight. One of the main weight reduction strategies has been to replace the traditional steel body with hybrid structures.
A common replacement is a combination of aluminium and magnesium alloy. This hybrid will cause a difference in electrode potentials, ultimately increasing the likelihood of galvanic corrosion.
As if all that wasn’t enough, these vulnerable components tend to be much more exposed in electric vehicles too.
EV batteries (let’s pick on them again) that would usually be smaller and placed higher up in the engine bay of a combustion engine vehicle, are now much larger and placed closer to the wheels.
This causes the battery to face increased exposure to moisture, salt, and extreme temperature changes; all factors that help contribute to corrosion.
Remember that there are other components (like wiring etc) that are also experiencing this exposure, it’s not just batteries.
In summary, electric vehicles have a perfect storm of contributing factors causing them to be more prone to corrosion.
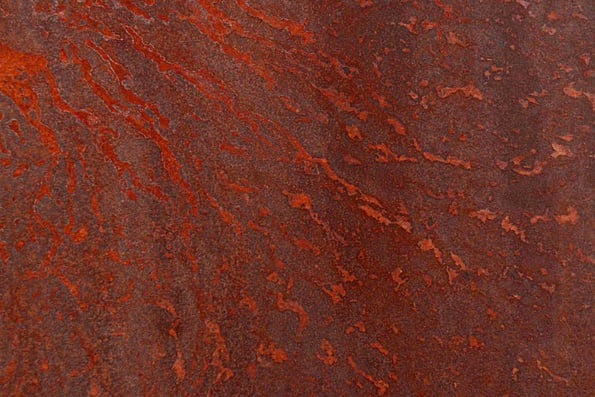
Why is corrosion in electric vehicles a problem?
Apart from the obvious reasons, there are several significant reasons why corrosion in electric vehicles is a problem.
It’s obvious that as an electric vehicle manufacturer, you want your products to be of the highest quality. Higher quality products will increase your company’s reputation and ultimately boost profits.
You’ve also got to consider warranty. If your vehicles keep having to come back in for rework and repairs, it’s going to end up wasting a lot of time, money, and resources.
However, it’s not just about the vehicle. This increased likelihood of corrosion can also affect infrastructure.
For example, Light Rail Transit Systems (similar to trams) can generate stray currents. Underground metallic structures can develop corrosion from these stray currents as the uncontrolled stray current is transmitted through the ground into pipework.
Iron ions are discharged at the point of exit from the pipe causing corrosion of the pipe.
This is just one example. The effect of corrosion from electric vehicles extends further than just the vehicles themselves.
But perhaps the biggest problem with EV corrosion is much broader than just the vehicle and its immediate surroundings.
Corrosion problems will only add to existing concerns about the reliability of EVs. And at a time when EVs are needed to replace one of the leading contributors to global warming, trust cannot be eroded any further.
The future of the planet is at stake.
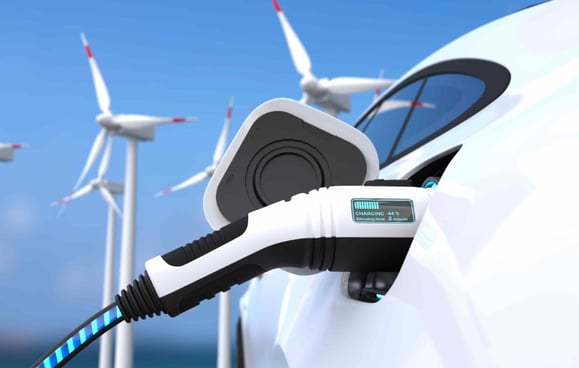
What can you do to prevent electric vehicles from corroding?
You know why the corrosion happens, and you know why it’s a problem. Now you need to know what you can do about it.
Luckily, there are several solutions to this problem.
Regular maintenance and inspections can help identify potential issues and address them before they cause significant damage.
Improving manufacturing processes can also help to minimize the risk of corrosion.
But perhaps the biggest solution is the effective design and material selection. These two factors are critical in preventing corrosion.
As we mentioned earlier in the article, newer, lighter materials contribute towards the corrosion problem. Ensuring the materials you use are not prone to corrosion will drastically help reduce the likelihood of it happening.
You can also use surface treatment methods or protective sealants to help protect any vulnerable surfaces. In our experience, a combination of these methods is the best approach.
Using materials less prone to corrosion as well as using protective sealants (like Formoa 760) is the best way to minimise the threat of corrosion in electric vehicles.
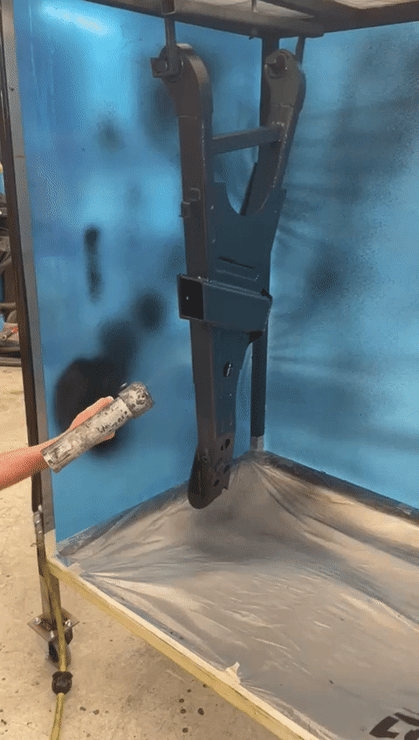
Finding the right corrosion prevention method for your application
Now you have a greater understanding of the corrosion problem in electric vehicles, it’s time to do something about it. But there’s never an easy solution.
Here at Forgeway, we manufacture industrial adhesives and sealants. The reason we know so much about the EV corrosion problem is that we have researched it and come up with a solution; Formoa 760.
However, we didn’t write this article to sell you our product. We wanted to educate you on this subject so you can do your job and produce high-quality electric vehicles that are much less likely to experience corrosion.
If you want more help on this topic, you can get in touch with an expert who can help with your specific challenge.
Alternatively, you can download the eBook called ‘The Fundamentals of Adhesives’. It goes into detail about adhesives and the bonding process to help you eliminate challenges like corrosion, stress cracking, and much more.
Click the button below to unlock bonding secrets.
Thomas is the Content Manager here at Forgeway. Thomas' job is to translate the technical jargon from the ivory tower of academia into easy-to-read content that everyone can understand. Forgeway's mission is to answer every question our customers and prospective clients ask, or are apprehensive to ask.