Is Saltwater an Adhesive Killer? What to Consider in a Marine Adhesive
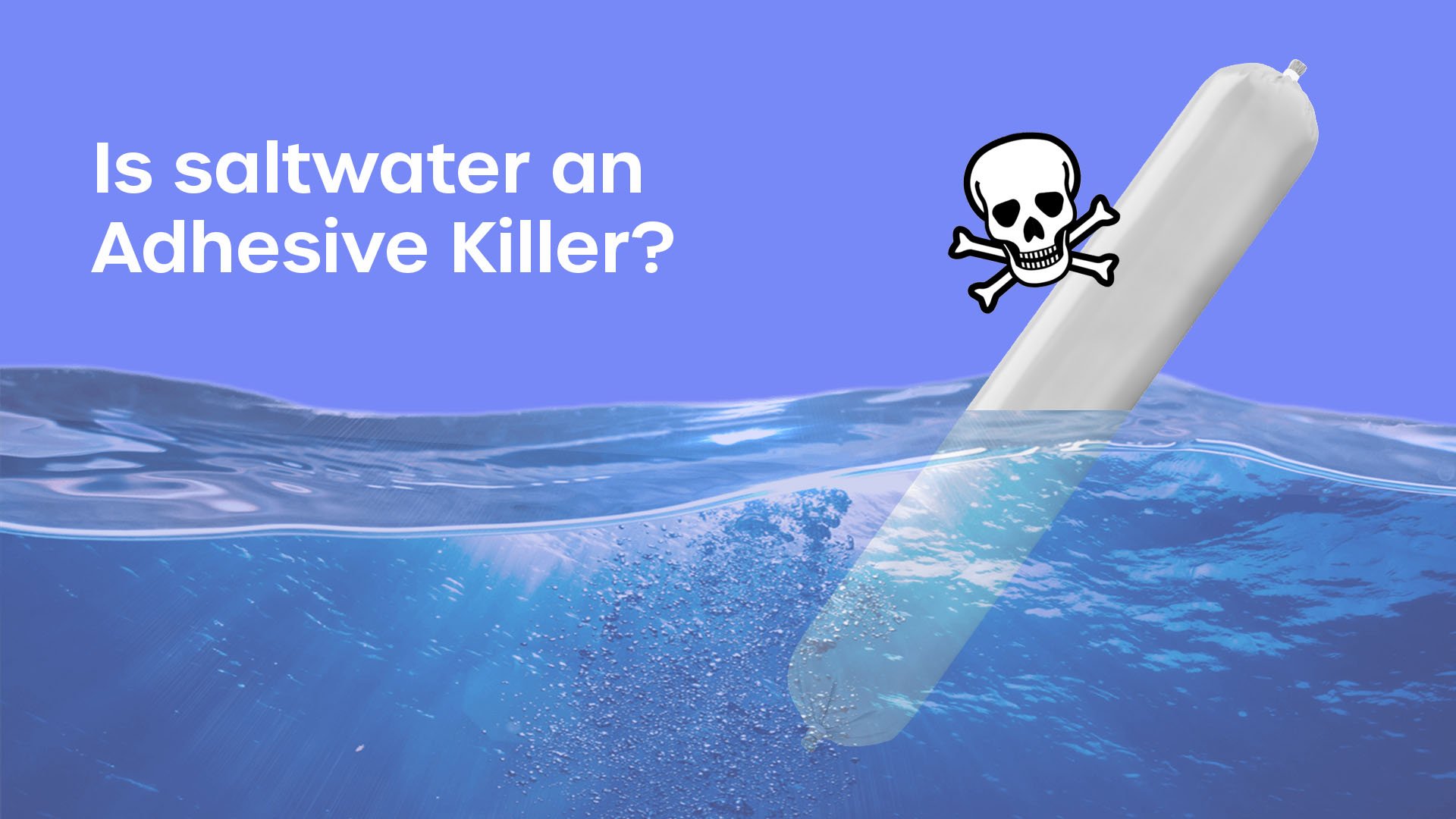
Selecting an adhesive is no walk in the park. There are so many different considerations, that it can feel overwhelming. Strength, flexibility, and durability are all essential characteristics to consider in an adhesive.
But marine applications add an extra complication; Saltwater. Most people know how corrosive it can be. So naturally, there is plenty of caution about the damage it can cause to a bonded joint.
At Forgeway we often get asked “Will Saltwater damage the adhesive and the bonded joint?”
Here at Forgeway, we manufacture industrial adhesives. We have been manufacturing marine-grade adhesives for over 25 years. We understand the effect saltwater can have on adhesives.
That’s why we are writing this article. We want to educate you. We are going to translate 25 years’ worth of testing and development to explain what happens to an adhesive when exposed to saltwater.
It’s also going to assess what factors can affect an adhesive in marine applications. By the end of this article, you will have a deeper understanding of what to consider when selecting a marine adhesive.
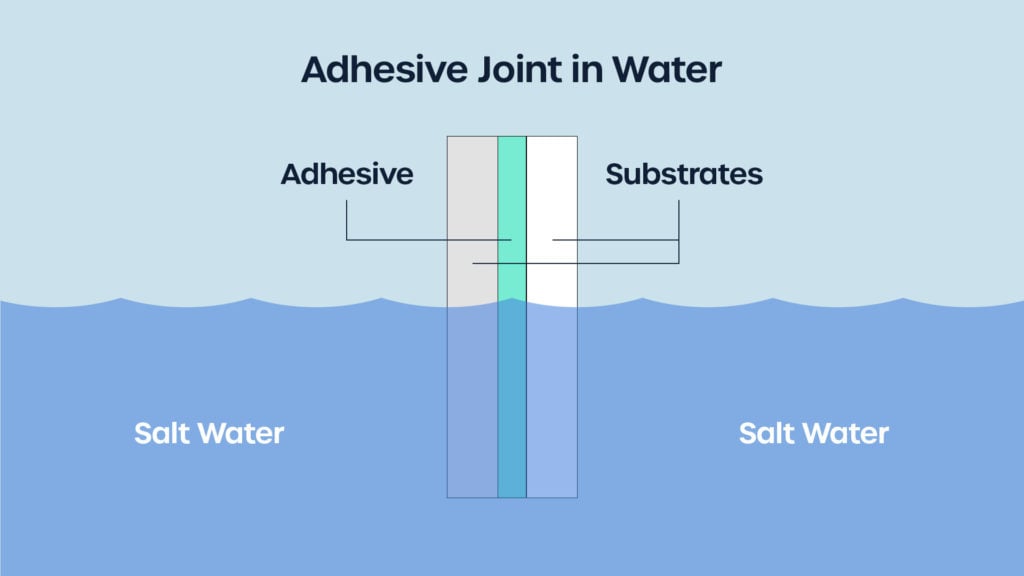
How Harmful is Saltwater on an Adhesive?
Perhaps surprisingly, saltwater has very little impact on an adhesive. In fact, we would go as far as saying saltwater will have no noticeable difference to an adhesive as opposed to freshwater.
Most people suspect saltwater is harmful due to its effect on some metals. Everyone knows that saltwater and metals aren’t a good mix. Rust ensues.
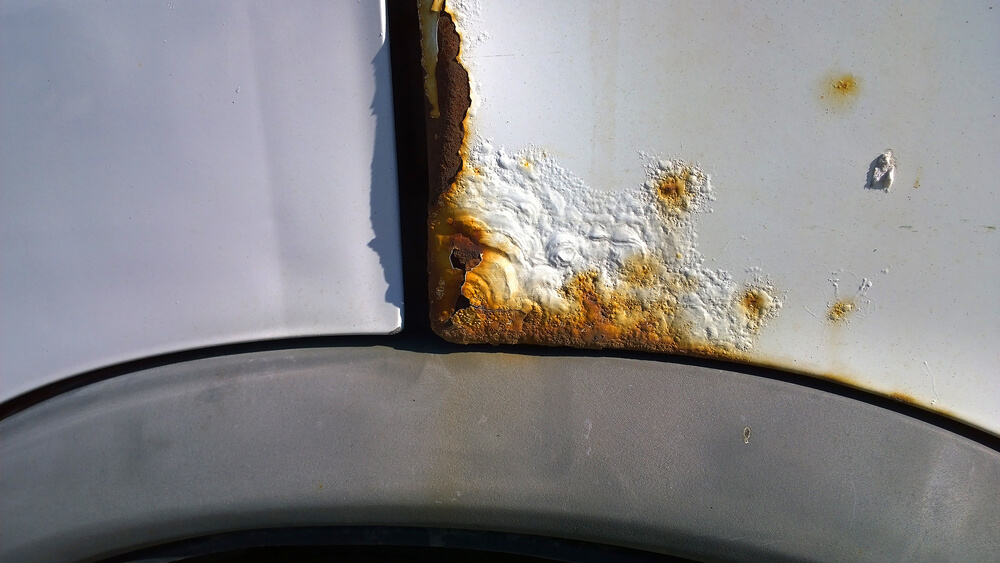
We should perhaps explain that saltwater doesn’t cause corrosion any more than saltwater. It simply speeds up the process.
So when it comes to adhesives, the salt in the water causes very little difference. The water itself is the real threat.
It’s not common knowledge that water is a solvent. Water (H2O) is a polar substance that can dissolve other polar molecules and ionic compounds. In simpler terms, water can dissolve most substances. It’s why salt dissolves into the water in the first place.
Water is a solvent. It will eventually degrade the adhesive. But that degradation process is usually over an extended period. You’ll usually experience the impact of water degradation after a few years (although this depends as we explain later).
Water can cause other issues too.
Adhesives, like most polymeric materials, will absorb water. They can also absorb water by cracks in the adhesive or through the bond interface. Water absorption in the adhesive can initiate several issues that can result in bond failure.
And as you can expect, there is plenty of water in a marine application. This makes it vitally important to consider the adhesive’s ability to withstand water.
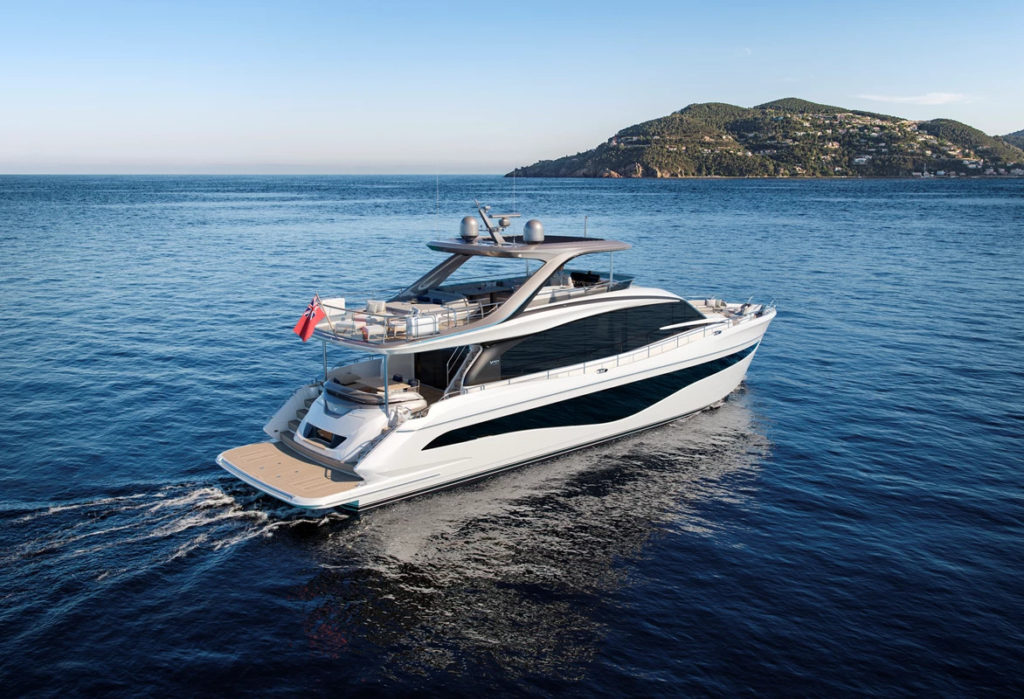
How does water affect a bonded joint?
Now we’ve established that water (H2O), as opposed to salt water, is the real issue. It’s time to understand why. Why does water increase the likelihood of bond failure?
Unfortunately, the answer isn’t very simple. Water can affect a bonded joint in several ways.
Water can degrade the adhesive
As we have already established, adhesives absorb water. Once the water starts permeating through the adhesive, it can begin to wreak havoc.
Interestingly, water vapour (like in humid climates) is more harmful than exposure to fluid water (like in marine applications). This is because water vapour can permeate the adhesive and travel along it more easily.
Swelling is a typical symptom as a result of water absorption. This swelling can lead to plasticization of the adhesive, making it more rubbery and flexible.
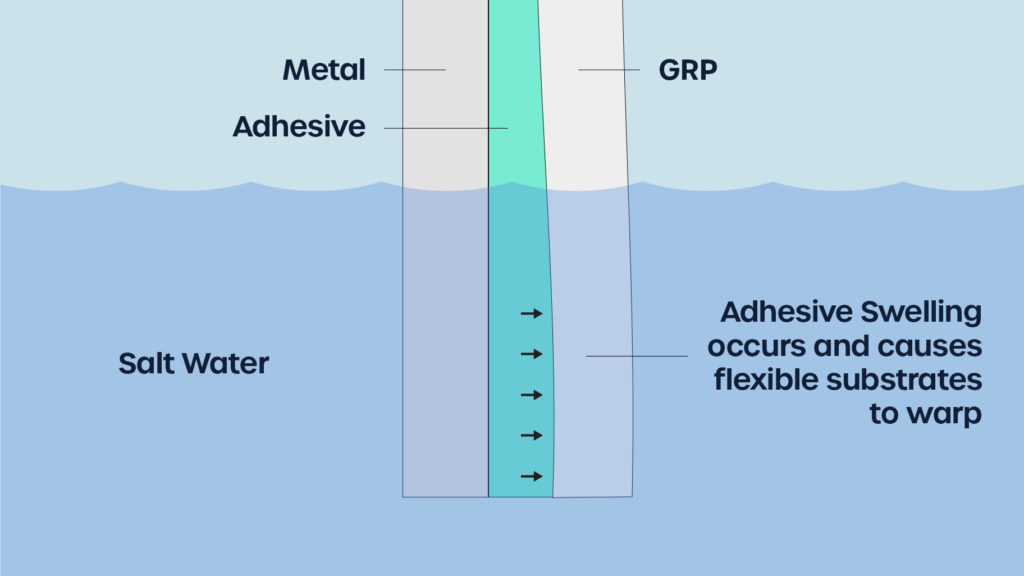
This, in turn, causes the adhesive to lose tensile strength but gain tensile elongation. The adhesive becomes less strong but more flexible. Consistent exposure to water will continue to weaken the adhesive.
Once the adhesive is no longer exposed to water (whether it is fluid or vapour) and allowed to dry, it generally returns to its previous state.
It’s also important to note that different grades of adhesives will have different rates of absorption. Epoxy adhesives generally have high crosslinking and are therefore more resistant to water absorption. Hybrid Polymer and Silicone-based products are generally more absorbent.
The raw materials used to make the product also play a part. Cheaper and less refined materials will absorb more water.
If the swelling hasn’t caused the bond to weaken (which it usually does), the water exposure can eventually degrade the adhesive entirely. This process of hydrolysation can chemically change the adhesive. It weakens the cohesive strength of the adhesive and reduces adhesion to the substrate.
All this sounds rather ominous and negative. We should note that both of these processes (absorption and hydrolysis) often take years to occur. However, this is dependent on the adhesive type, the grade of the adhesive, and the conditions it will face exposure to.
Some adhesives and applications may only take a few months to degrade. On average though, the process takes years to occur.
We have an excellent example to prove this, a global bus manufacturer used a Hybrid Polymer adhesive for a semi-structural application. The bus was going to be in use around the globe.
We needed to test the adhesive in the various climatic conditions it would experience in the real world.
We put the bond through accelerated weathering tests. This matches the climates of the different locations around the world. As the bus was going to be used in the UK, Ireland, and China, we matched these different climates.
The results were fascinating.
The adhesive would have lasted at least five years in the UK. The same adhesive would have lasted two years in Ireland. And shockingly, only six months in China. The adhesive failed ten times faster in China’s hot and humid climate.
There are also other interesting studies about adhesives’ resistance to water. One study found that adhesives’ tensile strength increased when they were under load and submerged in water. You can find the full report here.
In summary, water can have varying effects on adhesives and sealants. In most cases, water eventually degrades and weakens an adhesive. The different grades of adhesives and climatic conditions have varying effects on the adhesive’s durability in water. Testing is the only real way to understand the true effect of water.
For marine applications, it is critically important to test the adhesive’s ability to withstand water. Whether that is saltwater or freshwater, testing will give an accurate indication of the adhesive’s water resistance.
Water can degrade the substrate
It is common knowledge that water causes most metals to rust. Rust is every vehicle manufacturer’s nightmare. It’s also common knowledge that saltwater will worsen rust.
But as adhesive manufacturers, rust is also a concern for us. That’s because rust can cause a bond to fail. So when using metals for marine applications, it’s important to ensure the metal is capable of withstanding exposure to saltwater.
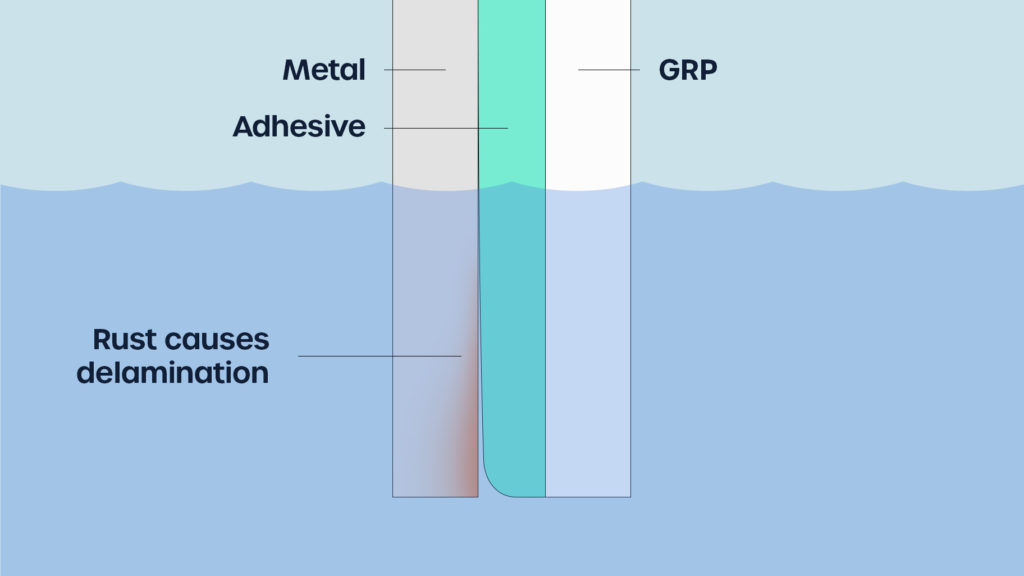
Nonetheless, water doesn’t only affect metals. Water also affects a very commonly used material in the marine industry; Composites.
Composite materials (like GRP or fibreglass) are very common in the marine industry and they aren’t immune to the threat of water.
A phenomenon called ‘blistering’ occurs as a result of osmosis and the permeability of composite materials. Blisters form on the surface of the composite when water and chemicals build up inside causing pressure to deform the material.
Often, the mix of water and chemicals inside the blister can degrade the material.
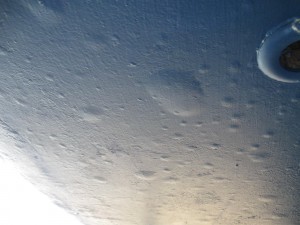
Interesting as it is, you’re likely wondering how blistering affects adhesives?
Well, in the same way that rust will severely weaken the bonded metal joint, blisters will also weaken the composite bonded joint. This is particularly the case if the blister forms close to or underneath the bondline.
In summary, water not only affects the adhesive, it also damages substrates used in marine applications.
Water damages the bond interface
Water doesn’t just damage the adhesive and the substrate. It can also damage the bond interface. This is where the adhesive’s molecules interact with the substrate’s molecules forming a bond.
Once water enters the adhesive, it travels along the interface wreaking havoc. Due to the polarity of water, it starts to form bonds with the substrate’s molecules instead of the adhesive’s molecules.
Eventually, this will travel along the polymer chain and the bond interface causing the entire bonded joint to delaminate.
This process is similar to the damage caused to the adhesive itself. It will affect some adhesives and materials faster than others.
The speed of this process will depend massively on the type of material and the adhesive type. Even different grades of metal can fail faster or slower.
On average, water travelling along a bond interface can take several years to take effect. Testing is the best way to understand how fast the adhesive is likely to fail.
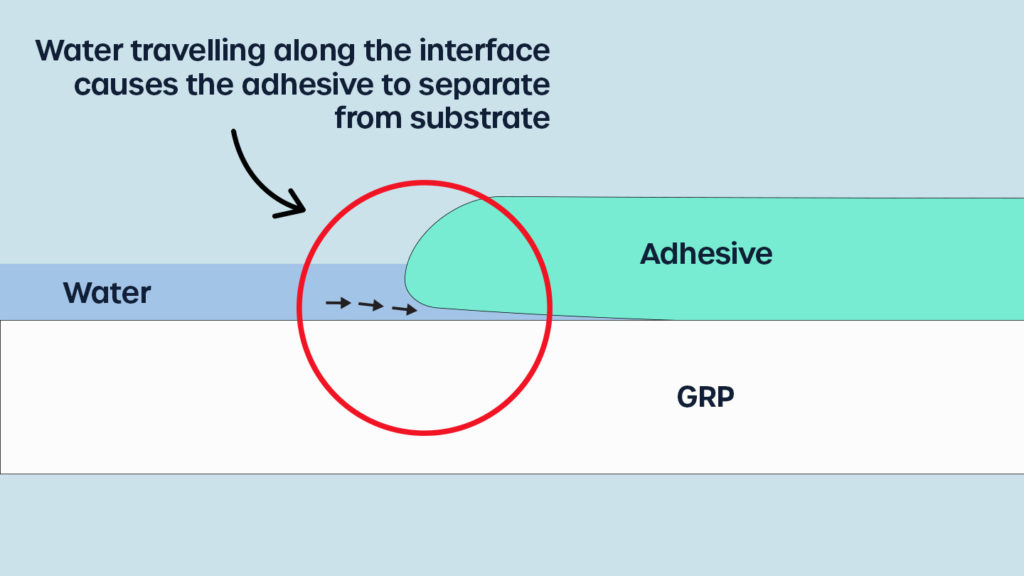
Summarising water’s impact on adhesives
To summarise the impact of water on adhesives, we should start by explaining that usually, this process of degradation takes years to occur. The two main things to consider are the grade of adhesive and the substrates you are using.
Adhesives like epoxies and acrylics often have much better performance when exposed to water. Their chemical structure and crosslink density generally help ensure they remain strong and durable.
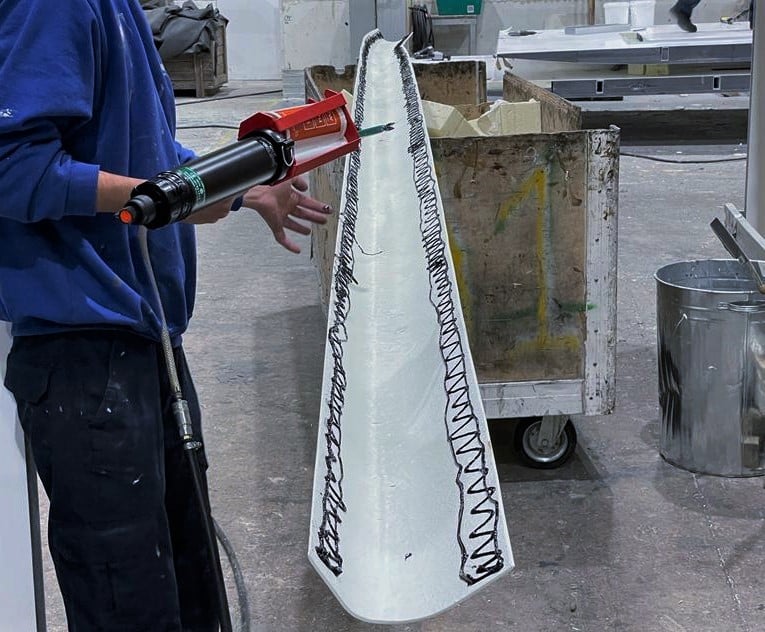
The substrate you are using will impact the quality of the bond too. Metals, in general, are more likely to rust and cause bond failure. GRP and fibreglass aren’t immune to water problems.
However, the quality of the GRP or fibreglass will severely affect the rate of degradation. Higher-quality composite materials are much less likely to experience blistering and degradation.
Nonetheless, it’s essential for marine manufacturers to understand that water (not just saltwater) can have a significant impact on the strength and durability of an adhesive. Even though water resistance isn’t the only characteristic of a marine adhesive, it is up there as one of the most important characteristics.
What are the important characteristics of a Marine Adhesive?
Now you understand water’s effect on adhesives. You’ll understand the importance of making sure the adhesive can withstand exposure to water.
But it doesn’t stop there. Several other characteristics are important from a marine adhesive. A strong and durable bond doesn’t end up ensuring water resistance.
Understanding the Marine Accreditations for Adhesives
As you will likely know, there are plenty of accreditations in the marine industry. The most prominent accreditation is the MED, often known as the Wheelmark.
It is a European Directive to ensure a baseline of quality and safety for equipment and products in the marine industry. It isn’t the only accreditation for marine adhesives.
Classification bodies like Lloyds Register, DNV, and RINA also have their own specifications for adhesives. Marine companies that wish to meet their criteria must ensure the adhesive meets the specifications.
If you’re supplying the marine industry or you’re in the marine industry, it’s important to consider whether the adhesive needs accreditations before going any further in the selection process.
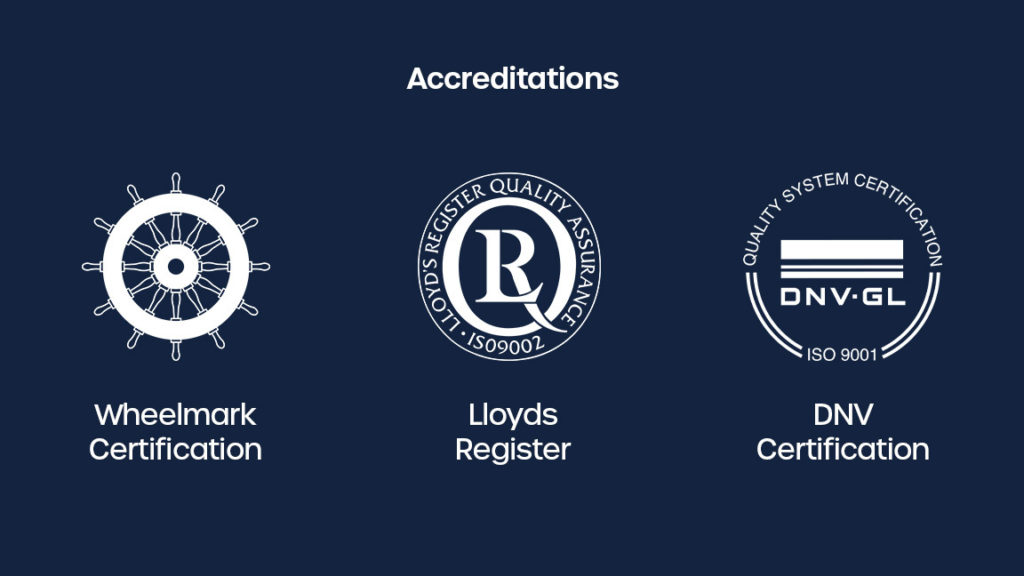
Make sure the marine adhesive is strong enough
Around a boat, there are several different types of adhesive applications. Some are structural (where the bond is essential to the structural integrity of the boat like a bulkhead or glass bonding).
Others are semi-structural (where the bond doesn’t affect the structural integrity of the boat but still needs to hold the materials in place).
Then there are purely sealant applications (the bond just needs to keep water in/out).
The type of application will dictate how strong you need the adhesive to be. For example, structural applications will often need very high-strength adhesives above 20 MPa. On the other hand, sealing applications won’t need so much strength.
The strength requirement depends entirely on the application.
Often though, ‘strong enough’ is a better target than ‘strong’. Searching for the strongest adhesive isn’t the best way to ensure a strong joint.
You must understand how much strength the joint needs before selecting an adhesive. This is more important than most marine manufacturers think.
Higher-strength adhesives often sacrifice other characteristics like flexibility and impact resistance which are critically important in marine applications.
Ensure the adhesive can cope with movement in marine applications
The sea is wild and unpredictable. On the rare occasion that the sea is ‘glassy’ flat and calm, a boat is still likely to flex and experience vibrations.
Usually though, a boat is in for a bumpy ride. It constantly deals with the impact of wind and waves. The whole vessel will need to flex and shift to accommodate the impact and stay intact.
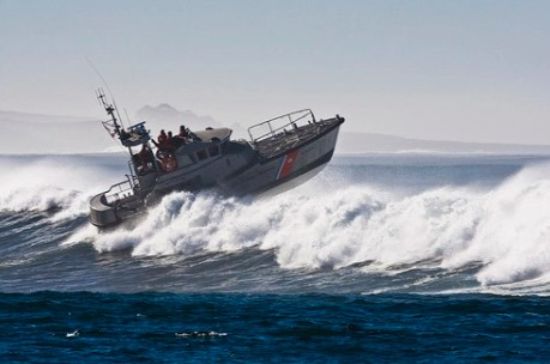
That’s when the debate around strength v flexibility arises. Most people don’t realise that flexibility is just as important as strength in an adhesive.
This is particularly the case in marine applications. Due to the movement a boat typically experiences, the adhesive must be able to accommodate and withstand that impact.
When the adhesive is high strength, it will often be rigid too making it brittle. It doesn’t take much impact for it to crack and fail. Even though it has very high strength, the adhesive likely can’t withstand impact.
Strength V Flexibility is a consequential scenario. As the strength of an adhesive increases, the flexibility decreases. And vice versa.
The importance is balancing strength and flexibility. Especially in marine applications where there is so much movement and impact.
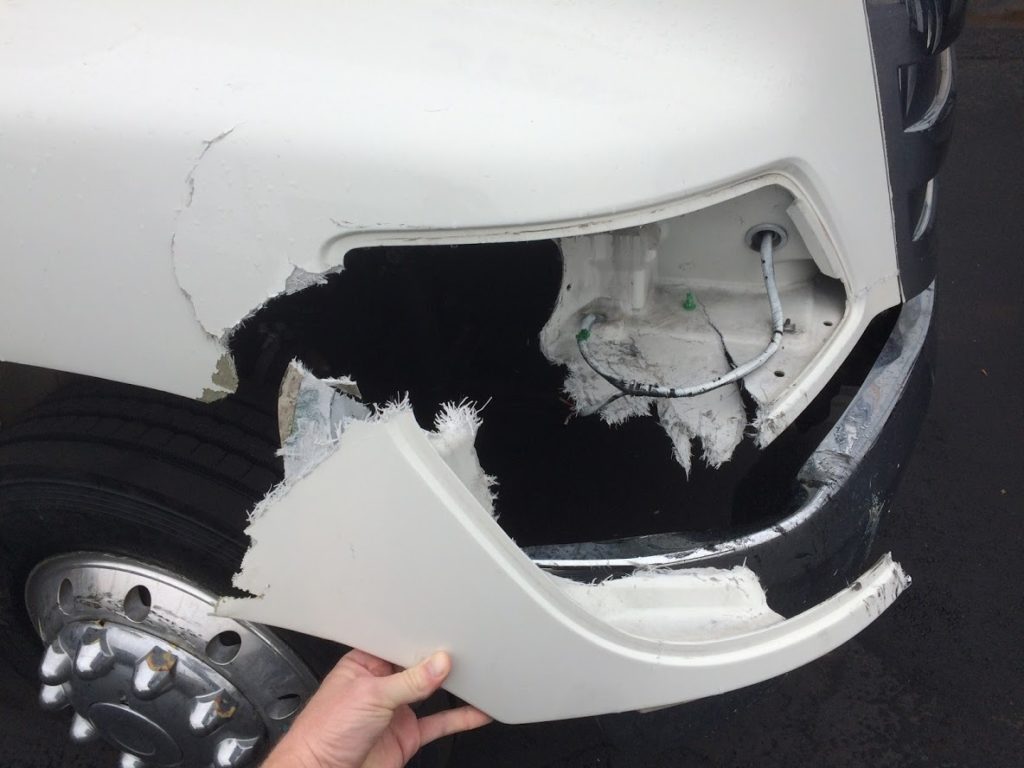
Ensuring the adhesive can withstand harsh conditions
We’ve discussed the effect of water at length in this article. You should understand by this point that water can be detrimental to the strength of a bonded joint.
However, other environmental factors can impact the durability of a bond. UV, chemicals, and temperature can all affect the durability of an adhesive.
Sealing and glass bonding are the two main applications that encounter exposure to UV. The effect of UV is similar to that of water. Except it can cause degradation much faster, particularly if the adhesive formulation is less capable of withstanding UV rays.
Polyurethane adhesives are typically less capable of withstanding exposure to UV rays. Polyurethane sealants will often go yellow and even start flaking after prolonged exposure to UV.
Exposure to chemicals and abnormal temperatures can severely affect adhesive performance. If the adhesive is in an engine room application, it is likely to come in contact with chemicals and raised temperatures.
It’s important to make sure the adhesive can withstand exposure to these conditions and remain durable.
Make sure to consider ease of production when selecting a Marine Adhesive
Production constraints often arise as a result of adhesive selection. Sometimes, the focus on performance takes over the thought put towards the effect on production.
Not only can the adhesive’s cure time cause a bottleneck in production. The surface preparation required to ensure a strong bond can also take up valuable time.
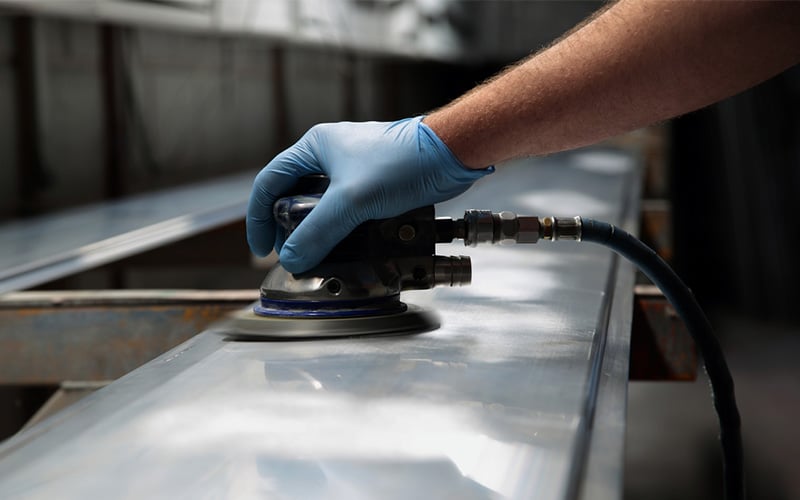
That’s why it’s essential to consider how much time is available in the production process to prepare the surface and allow the adhesive to reach handling strength.
Other considerations like storage, health and safety, and ease of use are also important as they can affect an adhesive’s impact on production.
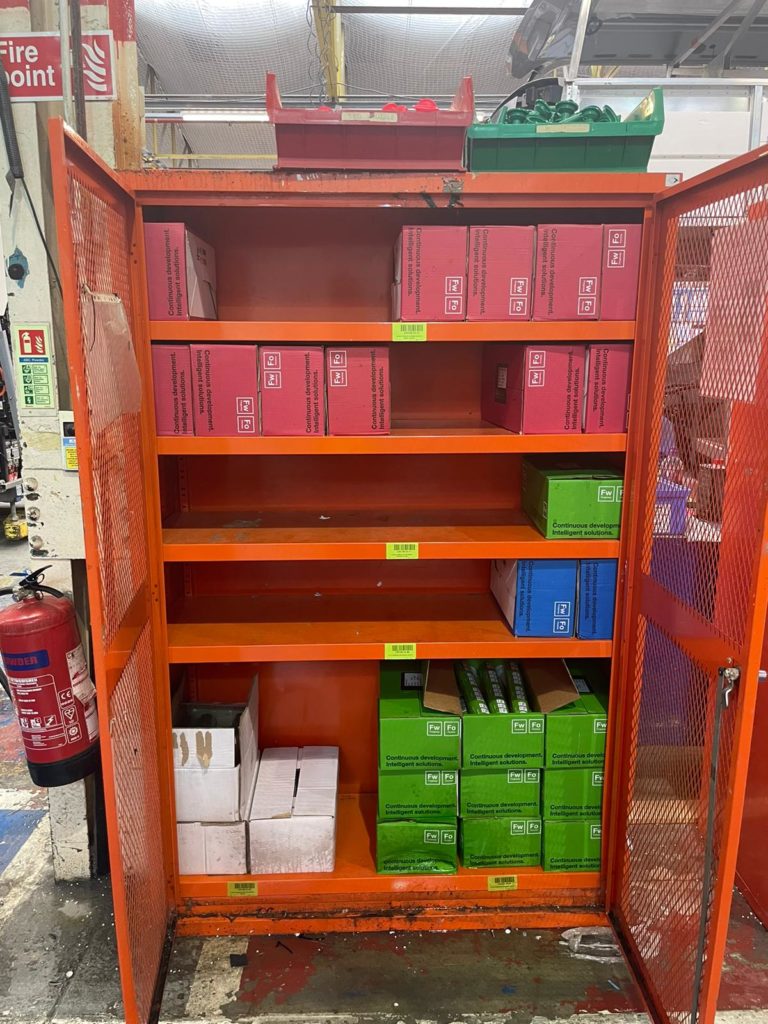
Ensuring strong and durable bonded joints in Marine Applications
So, you know that water (not necessarily saltwater) will have an impact on an adhesive. You also know that there are several factors to consider when selecting a marine adhesive.
You’re probably struggling to know where to start.
Here at Forgeway, we manufacture industrial adhesives. Our products have been bonding and sealing boats, planes, and vehicles for over 25 years.
The bonding challenges faced in the marine industry aren’t impossible to overcome. In fact, we likely have a solution that can solve the challenge you’re facing.
Nonetheless, you may want to research the solution yourself.
In that case, we suggest you read our article that discusses how to choose the right adhesive. It will guide you through the different things to consider in more detail.
Or, if you’d like to get in touch with a member of the Forgeway team, we suggest you click the button below. After explaining your application, the Forgeway expert can help suggest an exact solution to your challenge.
Thomas is the Content Manager here at Forgeway. Thomas' job is to translate the technical jargon from the ivory tower of academia into easy-to-read content that everyone can understand. Forgeway's mission is to answer every question our customers and prospective clients ask, or are apprehensive to ask.
Topics: