Accreditations for Marine Adhesives; How important are Marine Accreditations like Wheelmark?
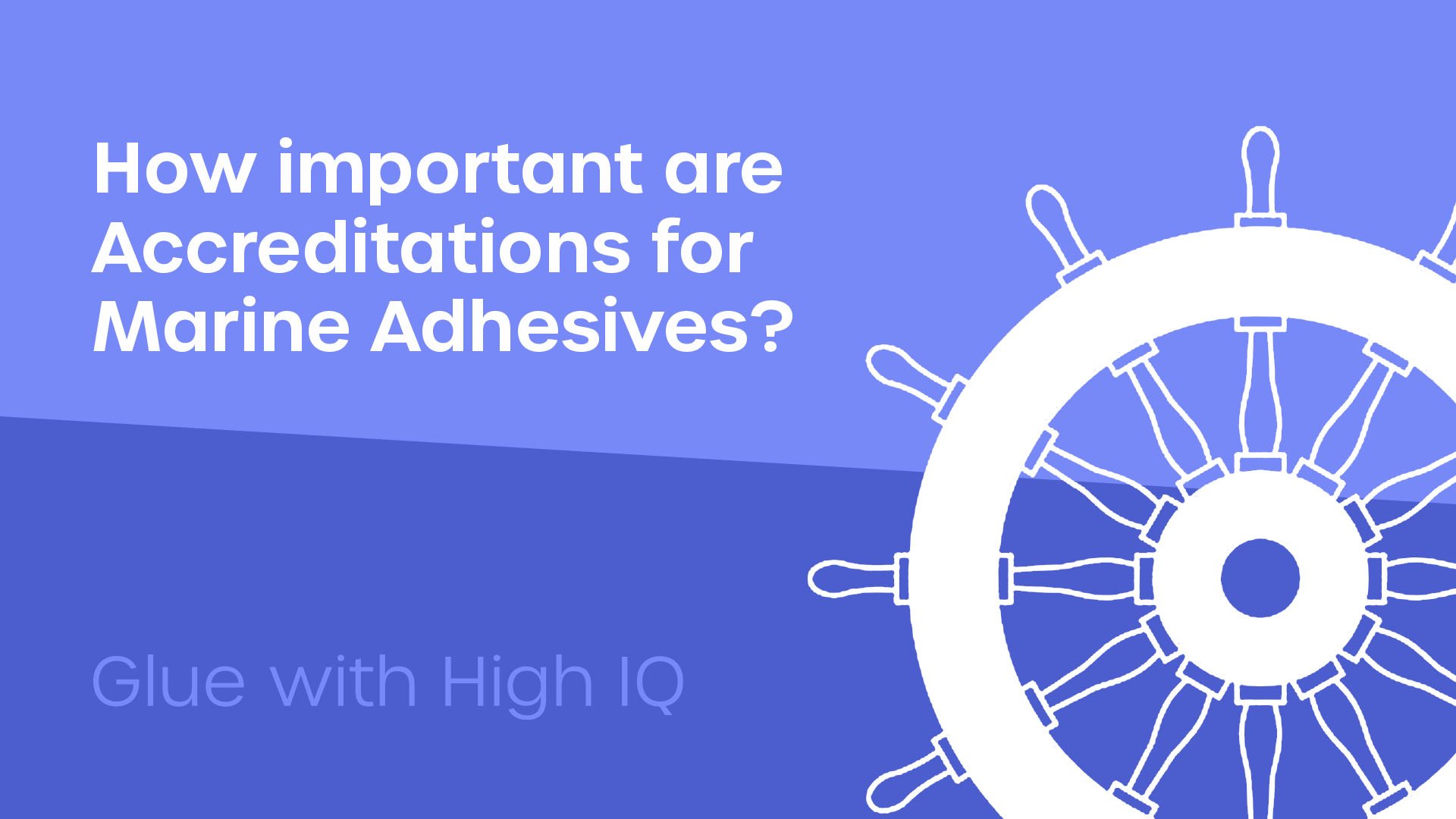
When it comes to choosing adhesives for the marine industry, there are countless options available. Maritime manufacturers have thousands of adhesive options from a vast array of suppliers. Some see this as a luxury. Others suffer from analysis paralysis.
That’s why accreditations like Wheelmark help narrow down the options. Accreditations seemingly make the adhesive choice easier as products without certification aren’t up to marine standards. Right?
Well, that’s what we want to analyse in this article.
Here at Forgeway, we manufacture industrial adhesives. Despite our products being common in the marine industry, they don’t have Wheelmark (or similar) certification.
So in this article, we are going to explain the different marine accreditations and assess if these accreditations are essential for marine applications. Then we want to explain how you can truly ensure adhesives are up to marine standards.
What are the different marine accreditations for adhesives?
In the marine industry, there are strict rules and regulations around the quality and safety of ships. There are international institutions and regulatory bodies responsible for the safety of the high seas.
The Safety of Life at Sea (SOLAS) convention was first created in 1914 in response to the Titanic disaster. It is one of the most important international treaties concerning the safety of merchant ships. SOLAS is an international convention from the International Maritime Organisation (IMO) which is responsible for regulating shipping.
There are other classification bodies too. Twelve organisations form part of the International Association of Classification Societies (IACS for short). This society helps with the development of maritime regulations and ensures classification remains a key part of self-regulation in the marine industry.
IACS provides technical support and unified interpretations of regulations developed by the IMO. In summary, the International Maritime Organisation is responsible for regulations and guidance to ensure the safety of merchant ships.
However, as a result of the amount of the various classification bodies, the Marine Equipment Directive (MED) was set up for members of the EU. It is a set of regulations established by the EU and helps provide a simplified approval process and reduce costs for the end user.
The MED provides approved products with a ‘Wheelmark’. This is why companies often refer to the MED as a Wheelmark approval.
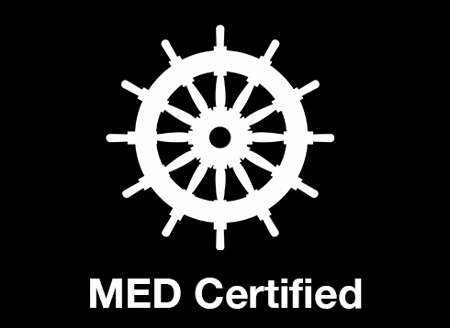
Understanding the MED Wheelmark accreditation for adhesives
The most common marine adhesive accreditation we have come across is the Wheelmark accreditation. The well-known ship’s wheel symbol is a mark of quality given by the Marine Equipment Directive (MED).
Any products bearing the ‘wheel’ of approval meet the quality and safety standards set out by the MED.
When a product, such as an industrial adhesive, bears the Wheelmark logo, it assures manufacturers and users that the product has undergone thorough testing and evaluation. This helps ensure its reliability and effectiveness in marine environments.
The European Union set up the MED but there is a Mutual Recognition Agreement with the United States Coast Guard where both EU and USA will approve each other’s authorised products. Since Brexit, the UK Conformity Assessed (UKCA) marking has taken the place of the MED Wheelmark in the UK.
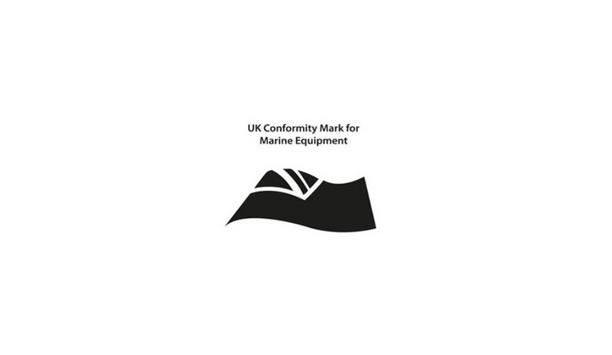
In summary, the Wheelmark or UKCA approval is a marker to indicate that products or equipment meet a recognised standard.
These accreditations are the most popular for marine adhesives and sealants. Nonetheless, you may still see specific standards from members of IACS that we mentioned above.
Lloyds Register, DNV, and RINA are members of IACS and have their own standards relating to adhesives. So, if you’re looking to build a vessel in compliance with one of those standards, it may need specific testing from one of these classification bodies.
However, more likely than not, the Wheelmark accreditation is the go-to for adhesives and sealants. Most manufacturers will accept products bearing the Wheelmark approval.
Are accreditations essential for marine adhesives?
The short answer is No, Marine Adhesives do not need to have accreditations. The longer answer is that some adhesives must have accreditations for certain marine applications, but not all.
The real answer depends on the application. Commercial boat and yacht builders are more likely to require certified products for their applications. Luxury and private manufacturers are less likely to require it. Pleasure vessels and boats less than 24 metres have a lot less stringent restrictions in place.
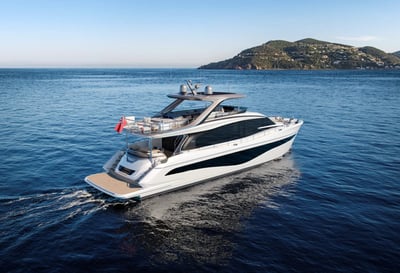
Mass transportation boats are higher-risk applications. Most manufacturers of these maritime vessels will specify that all their equipment must have the wheelmark accreditation.
The true benefit of having certified products is the reduced threat of scrutiny in the event of a tragedy. Using certified products appears to demonstrate a desire for quality-approved products.
Let’s use an example to demonstrate. Let’s say there was an incident on a large ferry transporting hundreds of civilians. A few of those civilians were harmed in the incident.
An investigation revealed the manufacturer had not used products that were quality assured to the wheelmark standard.
At best, the incident merely doesn’t reflect well on the manufacturer. Bad publicity follows.
At worst, a lawsuit ensues and a criminal investigation unfolds.
Manufacturing boats that will transport large amounts of people presents a significant amount of risk. Ensuring that products and equipment have a baseline of quality and safety is essential to reduce that risk.
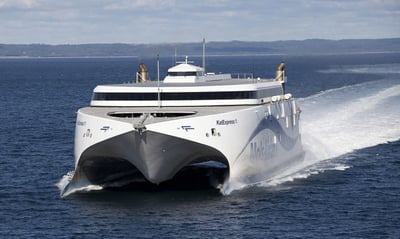
That’s what the wheelmark certification offers for adhesives and sealants (among many other products). It offers peace of mind that the adhesive or sealant has had a baseline of quality and safety testing.
But that’s really all it is; a baseline. It is not and should not be the only thing a manufacturer looks for in an adhesive. A high-quality and durable bond is reliant on much more than an accreditation.
Far too often, we see manufacturers who are looking for an adhesive fall foul of assumption. They will see the wheelmark of approval and automatically think it is good enough for the job.
By doing this, marine manufacturers overlook the very reason quality assurance exists (to ensure quality products).
So whilst accreditations are a useful indicator of quality (and in some cases essential), maritime manufacturers need to look further than just an accreditation when selecting an adhesive or sealant.
Read about how you can ensure a strong and durable bond.
Why accreditations should have little importance when selecting an adhesive
Choosing an adhesive purely based on its accreditations is a big risk. It’s similar to buying a vehicle and expecting it to perform well off-road just because it is 4×4. Yes, it’s more likely. But in reality, the 4×4 might not perform well off-road due to the ride height or the tyres or any of the other factors that make a vehicle perform well off-road.
The same is true of adhesives. Several factors can affect how well it performs in a marine application. Not just its accreditations.
Water absorption, UV resistance, and adhesion to GRP are very significant factors to consider in a marine adhesive. We explain what you need to consider in a separate article about saltwater adhesives.
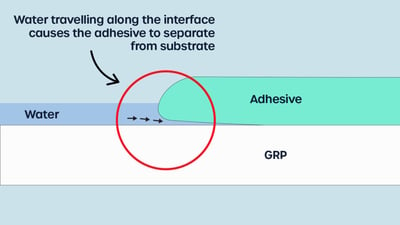
You could argue that if an adhesive has passed a marine accreditation, it is likely to have those characteristics we discussed above. And you would be right. Although you can’t guarantee it.
Here’s an example of this. We recently saw a marine manufacturer use a wheelmark-accredited adhesive sealant with a base chemistry of polyurethane. Despite its wheelmark accreditation, it performed poorly in an exterior sealant application.
The UV caused the sealant to turn yellow and eventually caused degradation.
So, we decided to compare this product. A wheelmark-accredited adhesive sealant against one without the accreditation. Those of you with a sense of poetic justice will guess the result.
The marine-accredited product turned yellow and degraded significantly faster than the unaccredited product.
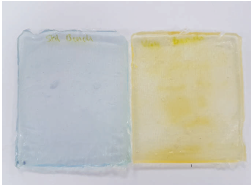
Both products were marketed as ‘adhesive sealants’. Just one had superior UV stability than the other.
But this wasn’t really a surprise. Polyurethane-based adhesives and sealants are well known for their poor UV resistance. It just so happened that this Marine-Accredited was polyurethane-based. The other adhesive sealant had a hybrid polymer base chemistry which has a much greater UV resistance.
The test highlighted what we like to tell marine manufacturers globally. Unless you know what characteristics are important in an application, you can’t guarantee a quality end result. Regardless of accreditations.
Accreditations don’t guarantee performance.
What characteristics are really important for marine adhesives
Here are a few other important factors that you’ll need to consider from an adhesive for marine applications.
Strength – It goes without saying that if you’re using the adhesive for structural applications, you’ll need to ensure it has enough strength. It can be tricky to determine how much strength you need from an adhesive but testing and calculations can give you a good idea of how strong it needs to be.
Flexibility – Most people don’t realise that flexibility is just as important as strength. This is particularly the case in marine applications. The adhesive will likely experience a lot of movement. Movement will cause the adhesive to crack and fail if it doesn’t have enough flexibility.
Durability – The term durability is an umbrella term for characteristics like chemical, heat, and weathering resistance. For example, if the adhesive or sealant application is in an engine room, it will need to be able to withstand the temperatures and any chemicals which can weaken the bond.
Substrates – Understanding what you are bonding can have a big impact on the adhesive choice. Some materials are difficult to bond. GRP and composites are the most common materials in marine applications. Nonetheless, plastics like polypropylene and metals like galvanised steel are popular too. These materials in particular can cause bonding challenges.
There are other characteristics to consider too (like price and cure speed among many others), but the above examples are to highlight that accreditations alone won’t determine how successful an adhesive is likely to be in a marine bonding application.
Choosing the best adhesive for marine applications
Despite what some people may lead you to believe, there are plenty of options available for marine bonding applications. If accreditations (like wheelmark) are essential for your application, then you should head over to view some of our competitors. There are a few that have the wheelmark certification.
However, if marine accreditations aren’t the most important thing in your adhesive choice, then you’re in the right place.
Here at Forgeway, we manufacture industrial adhesives. We’ve been solving complex bonding challenges for industrial manufacturers like you for more than 25 years.
Over the years, we’ve developed a range of products perfectly suited for the marine industry. However, there is no ‘perfect’ adhesive that is suitable for all applications.
From colour-matched sealants to specialist plastic bonders and everything in between, we have a range of products available for marine manufacturers.
If you want to research more about marine adhesives, make sure to click on the button below. It will take you to an article dedicated to helping you find the right adhesive.
Or, if you’re looking to speak to an adhesive specialist, you can reach out to a member of our team who would be happy to help solve your challenge.
Thomas is the Content Manager here at Forgeway. Thomas' job is to translate the technical jargon from the ivory tower of academia into easy-to-read content that everyone can understand. Forgeway's mission is to answer every question our customers and prospective clients ask, or are apprehensive to ask.