How Primers can impact Efficiency and Costs in Adhesive and Bonding Processes
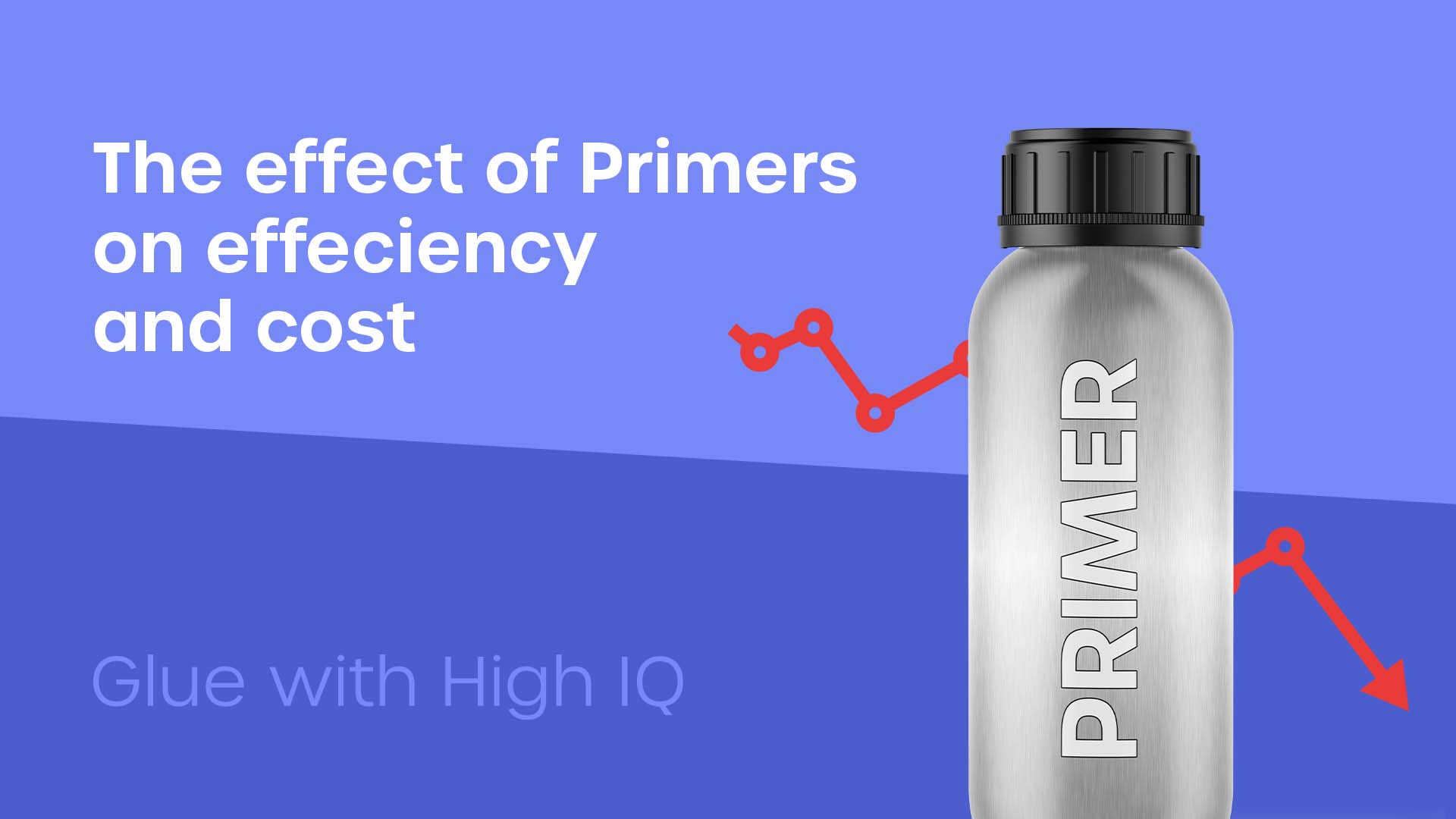
The objective for most manufacturing companies is to improve efficiency and reduce costs. After all, who wouldn’t want to maximise profit? Manufacturers who have bonding processes will seek ways they can improve them.
The use of primers plays a crucial role in promoting adhesion. They improve surface wetting and chemical compatibility. However, they also introduce challenges that can hinder efficiency and increase costs.
Here at Forgeway, we manufacture industrial adhesives. We’ve had over 25 years of experience helping industrial manufacturers improve their bonding processes. So we wrote this article. We want to publish the experience we’ve gathered about the use of primers.
By the end of the article, you’ll understand primer’s role in adhesive processes. You’ll be aware of the impact primers can have on efficiency and costs. And you’ll be given practical tips on how to improve these processes.
Understanding the Role of Primers in Adhesive and Bonding Processes
In the bonding process, primers are substances that interlink with the adhesive to form a strong bond. Primers are formulated to create a new surface that will improve the wetting and chemical compatibility between the adhesive and substrate.
Traditionally, primers were an essential part of the bonding process. But as adhesive technologies have advanced, they are no longer always a necessity.
The main benefit of using primers is that they will usually guarantee a strong bond between the substrate and the adhesive. You won’t need to worry about contamination or incompatible substrates impacting the adhesion.
Primers can help ensure a strong bond. Strong bonds improve the reliability of the end product.
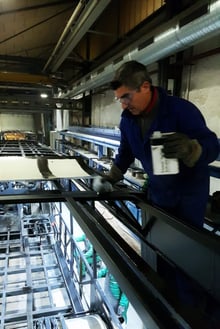
What Challenges are Associated with Primers for Adhesives?
Whilst primers will usually guarantee a strong bond, they can also bring challenges that affect efficiency and cost-saving efforts.
Priming will typically add a lengthy, and sometimes complex, procedure to the bonding process. Your objective is to create a repeatable and low-cost process. Primers often take you in the opposite direction.
There are several things you can do to create a repeatable process. Removing complex procedures can dramatically increase repeatability.
The priming process can be complicated. Sometimes, you will need to abrade the surface before priming. Then, you will need to clean the surface. After that, you can apply the primer. Now, you need to wait for the primer to cure.
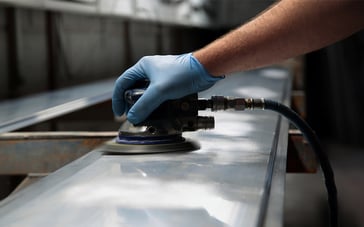
Four steps and 24 hours later, you are ready to start bonding.
As you can see, this process is lengthy. There are a lot of stages where operator error can take place. Inconsistent application will increase the likelihood of quality issues further down the line.
The other challenge associated with primers is the health, safety and environmental risks. Most primers will contain harmful chemicals. These harmful chemicals can hinder sustainable and environmental efforts.
They can also create the need for companies to provide health and safety screening for operators.
To summarise, primers can create several challenges. Whilst they are very beneficial in helping to ensure a strong bond, primers can create bottlenecks in production.
They can also add layers of complexity to production processes, as well as pose health and safety risks.
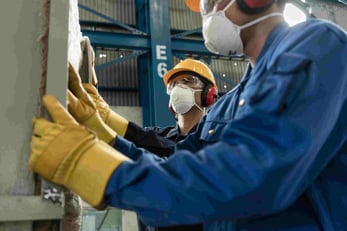
Can you replace primers in the bonding process?
Now that you know the challenges primers can create, you’re probably wondering what a primerless system looks like. As an adhesive manufacturer, we want to help you find the best adhesive system that will improve efficiency and reduce costs.
So we aren’t biased towards a primer-based system or a primerless system. We want you to find the best system that works for your organisation.
Having said that, manufacturing companies often ask us to help them with a primerless system. They are facing challenges with their primer-based system. They want to move away from using primers.
And you’ll be pleased to know that the answer is yes. It is absolutely possible to have a primerless adhesive system.
There are two options you can explore:
- Primerless one-component adhesives (such as MS Polymers)
- Primerless two-component adhesives (such as acrylic adhesives)
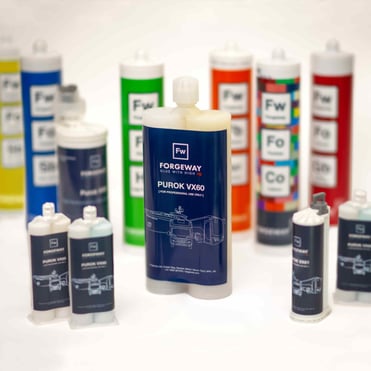
Whether you are using primers with one-component or two-component adhesives, there are primerless options available.
Whilst you will still need to clean the surface (in most cases) to achieve a strong bond, you will not need to go through the lengthy process of priming.
Primerless adhesives reduce curing times, enabling faster production cycles and increased throughput.
Secondly, they simplify the bonding process by eliminating the additional steps required for primer application. This streamlines operation and reduces the potential for errors.
Lastly, primerless adhesives can sometimes exceed the bond strength and durability of primer-based adhesive systems, ensuring reliable and long-lasting adhesive joints.
If you want to find the exact adhesive type for your application that doesn’t require primers, fill out the quiz. You’ll receive a recommendation in just 45 seconds.
Stick or twist? Should you remove primers from your process?
You understand the role of primers in bonding processes. You can see that primers can present challenges. You now also know that primerless adhesive systems are possible.
You can now start to decide whether using primers in your manufacturing process is the best route forward.
Here at Forgeway, we manufacture industrial adhesives. We have over 25 years of experience in helping companies find the best adhesive systems. Here is the advice we would give to companies who are in the same situation as you.
If the bonding process isn’t causing a bottleneck in your production or you are evaluating other areas that can have a bigger impact on efficiency and cost, then we wouldn’t advise looking at removing primers from your process.
However, in most instances, we would advise companies to remove primers from their process. Adhesive systems have advanced to the point where primers are mostly not required.
Nonetheless, you may still be unsure about your specific process. You may have a few more questions about whether a primerless adhesive system really is possible.
To speak to an adhesive expert, you can click the button below to discuss your exact details. The expert can help you decide what the best route forward is for your application.
Thomas is the Content Manager here at Forgeway. Thomas' job is to translate the technical jargon from the ivory tower of academia into easy-to-read content that everyone can understand. Forgeway's mission is to answer every question our customers and prospective clients ask, or are apprehensive to ask.
Topics: