Less Weight, More Efficient Vehicles: What to Consider when Using Adhesives to Lightweight Vehicles
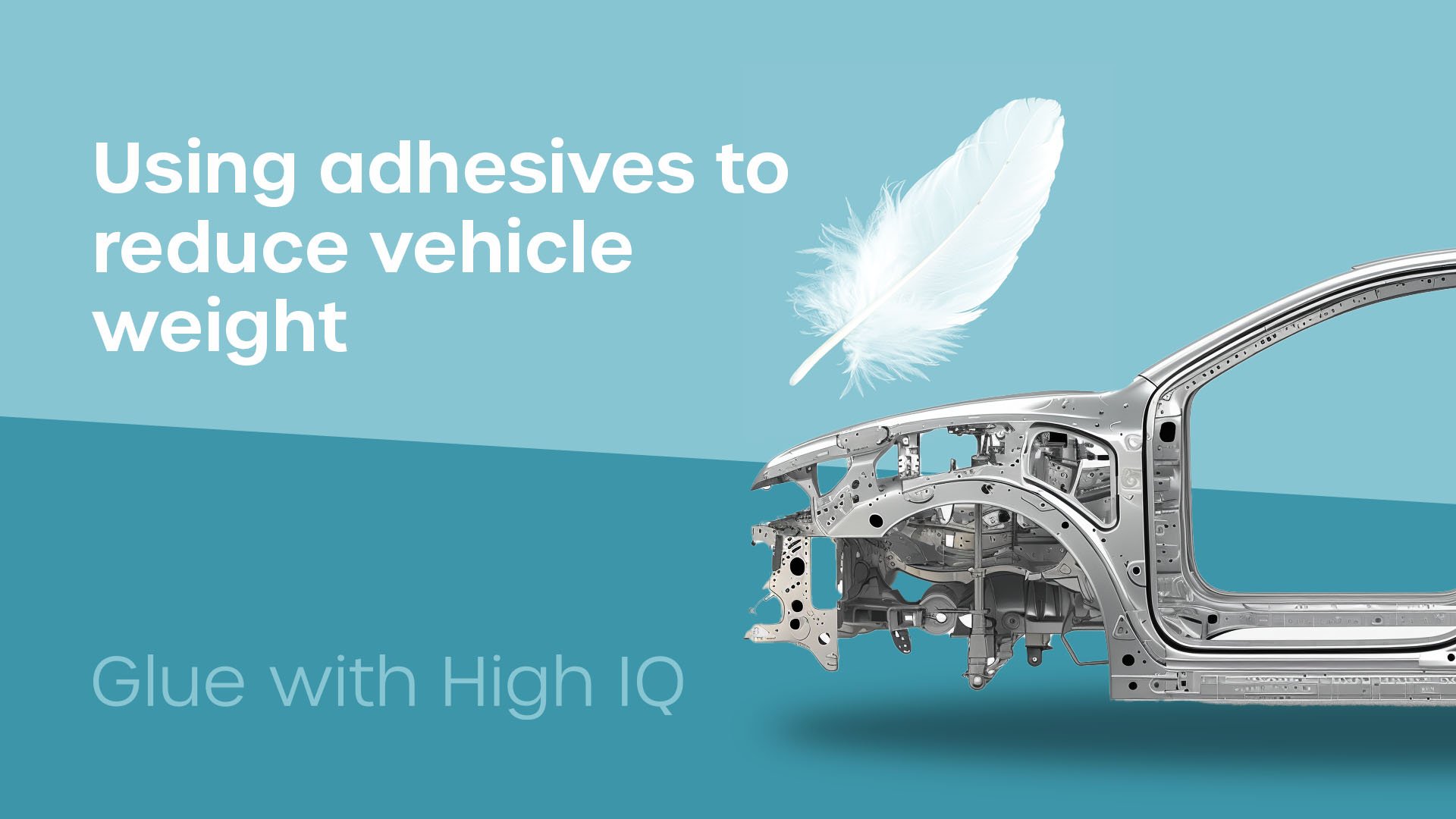
In recent years, the lightweighting of vehicles has been a prominent trend for vehicle manufacturers. Automotive, commercial vehicle and transportation manufacturers have all explored lightweighting solutions.
You may want to explore lightweighting further to understand why others are lightweighting and what you can do to lightweight your vehicle.
Here at Forgeway, we manufacture industrial adhesives. Vehicle manufacturers have been asking us how industrial adhesives can help them reduce their vehicle’s weight.
Whilst we have a few potential ideas, industrial adhesives are one of the less well-known solutions.
This blog will explore the different solutions we have seen vehicle manufacturers implement over the years to reduce the weight of their vehicles and how adhesives may be able to help you lightweight your vehicles.
By the end of the article, you will know all things lightweighting. It will help you get a better idea of how you can reduce the weight of your vehicles and what you should consider.
Why are companies Lightweighting their Vehicles?
Vehicle manufacturers (particularly in Europe and the UK) are trying to abide by regulations, improve payload, and most importantly improve fuel efficiency.
Reducing the weight of vehicles helps vehicle manufacturers meet these requirements.
Regulations like Euro 6 mean additional tanks (and weight) are required to make vehicles compliant. This added weight has meant that manufacturers need to reduce weight in other areas of the vehicle.
Improving payload is a desired outcome for most vehicle manufacturers. Commercial vehicles can carry more cargo, aeroplanes can carry more people, and boats can carry heavier cargo.
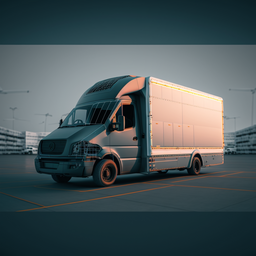
Ultimately, improving payload gets you more bang for your buck. You can get more into and out of the vehicle.
However, most vehicle manufacturers are looking to lightweight their vehicles so they can improve fuel efficiency. Improved fuel efficiency helps reduce running costs for the end user, potential taxation and environmental impact.
The research on this topic is staggering. Morgan Stanley estimates that if every vehicle (around 1 billion globally) was 50 KG lighter, $40 billion in fuel costs would be saved.
To put that into perspective, that is by removing 2.5% of the total weight of each vehicle. Marginal though it may seem, the impact is significant.
In addition to improved fuel efficiency, lightweighting also has a positive impact on vehicle performance.
Lighter vehicles are more agile, handle better, and have improved acceleration, making them more enjoyable to drive.
But in most cases, vehicle manufacturers are lightweighting to try and improve fuel efficiency.
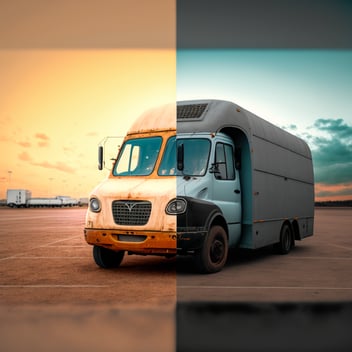
Evolution of Materials helping to Lightweight Vehicles
Thanks to innovation and technological developments, vehicle manufacturers can use newer and lighter materials to manufacture their products.
An example of this is aluminium. It has replaced the use of steel as it is not only lighter but can also have greater strength.
And vehicle manufacturers are increasingly using composite materials to replace metal altogether. Some composite materials are stronger and lighter than the metals they are replacing.
However, vehicle manufacturers have to remember one important thing. You can’t sacrifice the safety of the vehicles for lighter weight.
So when it comes to sourcing materials, manufacturers have to ensure they don’t reduce the safety of their vehicles.
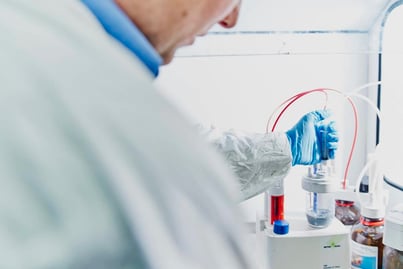
They also have to ensure that the new materials aren’t going to cause problems in other areas too.
As adhesive manufacturers, we often see issues arising at this stage. Vehicle manufacturers look to switch the materials, but they don’t consider the wider impact these new materials can have.
Sometimes, the new material has low surface energy which causes bonding issues. As you may already know, surface energy plays a very important part in the success of an adhesive.
Another thing to consider is corrosion. It is already a significant headache in electric vehicles. But galvanic corrosion is especially a problem when replacing steel with aluminium due to the different properties.
So if you intend to source lighter materials, make sure you consider the wider impact it could have.
In particular, we recommend considering the impact it will have on a bonded joint. If you are unsure whether the new material could cause bonding problems, watch the video below.
Techniques for Lightweighting Vehicles
When it comes to lightweighting vehicles, there are several techniques manufacturers can implement. This section will go over the two main techniques we recommend to help you lightweight your vehicles.
Technique 1: Use lightweight alternative materials
As we have discussed above, using lighter materials is one of the main techniques in lightweighting vehicles.
But where do you start when looking to replace those heavy materials?
As we have helped multiple vehicle manufacturers lightweight their vehicles, there is a process we usually take.
Whilst it may seem obvious, evaluating the heaviest materials is a good place to start.
Glass can often be one of the heaviest parts of the vehicle. But using a plastic alternative isn’t very desirable mostly due to the inability to break it in an emergency.
The engine is also another heavy part of the vehicle. However, it is difficult to reduce the weight of the engine without having a significant impact on the performance of that vehicle.
So, most of the time you will not be able to reduce the weight of the heavier parts. Either they are integral to the safety of the driver/passenger or the performance of the vehicle.
It is essential at this stage to remember that you should not sacrifice safety to reduce the weight of vehicles.
Most of the time, we have seen vehicle manufacturers reduce weight by making a large number of small changes.
An example of this was an automotive manufacturer using composite materials for the seats instead of metal. This managed to shave off more than 15 kg.
Whilst it doesn’t seem a lot, small but consistent weight reductions have a big impact on overall weight-saving efforts.
This is why we always recommend trying to reduce the weight of larger materials, but don’t forget to evaluate any smaller materials where you can reduce weight too.
Technique 2: Remove materials that add unnecessary weight
Whilst looking for alternative but lighter materials is one of the most common techniques of lightweighting vehicles, there are some instances where you can remove unnecessary weight altogether.
You may think that every piece of the vehicle is essential. However, there are occasions we have helped manufacturers remove items that don’t need to be there.
When it comes to perfecting this technique, the key is to think outside the box and question existing processes.
The best example is when we helped a commercial trailer manufacturer reduce the weight of their trailers.
After analysing their process and design, the question arose about their use of backplates and mechanical fasteners to hold the loadlok in place.
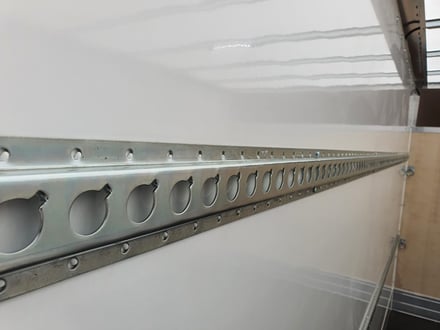
They then discovered the backplates were adding an extra 40 kg onto each trailer. After looking for an alternative method to mechanical fasteners, they were able to use adhesives to remove the need for these added backplates.
Whilst the trailer manufacturer needed the outside perspective from Forgeway, they were able to work out that the backplates were not essential.
It just required thinking outside the box to assess what they could remove from the vehicle.
What you need to consider when Lightweighting Vehicles
Now you know all about lightweighting and why it’s so important, it’s time to work out what methods you can use to reduce the weight of your vehicles.
Here at Forgeway, we manufacture industrial adhesives. Over the years, we’ve helped vehicle manufacturers all over the globe explore lightweighting solutions.
But whilst there may be several solutions to lightweighting your vehicles, we recommend considering the wider impact those changes are going to have.
The examples we have given are real-life examples. However, they demonstrate the importance of considering the bigger picture when implementing lightweighting methods.
If you’re looking for ways to reduce the weight of your vehicles, we would recommend exploring ways to remove unnecessary weight like mechanical fasteners.
Filling out the quiz below will help you assess which adhesive solution might be able to replace mechanical fasteners.
Or, you may want the help of an expert who has experience helping other vehicle manufacturers reduce the weight of their vehicles. You can reach out to one who will be happy to assess your application.
Thomas is the Content Manager here at Forgeway. Thomas' job is to translate the technical jargon from the ivory tower of academia into easy-to-read content that everyone can understand. Forgeway's mission is to answer every question our customers and prospective clients ask, or are apprehensive to ask.
Topics: