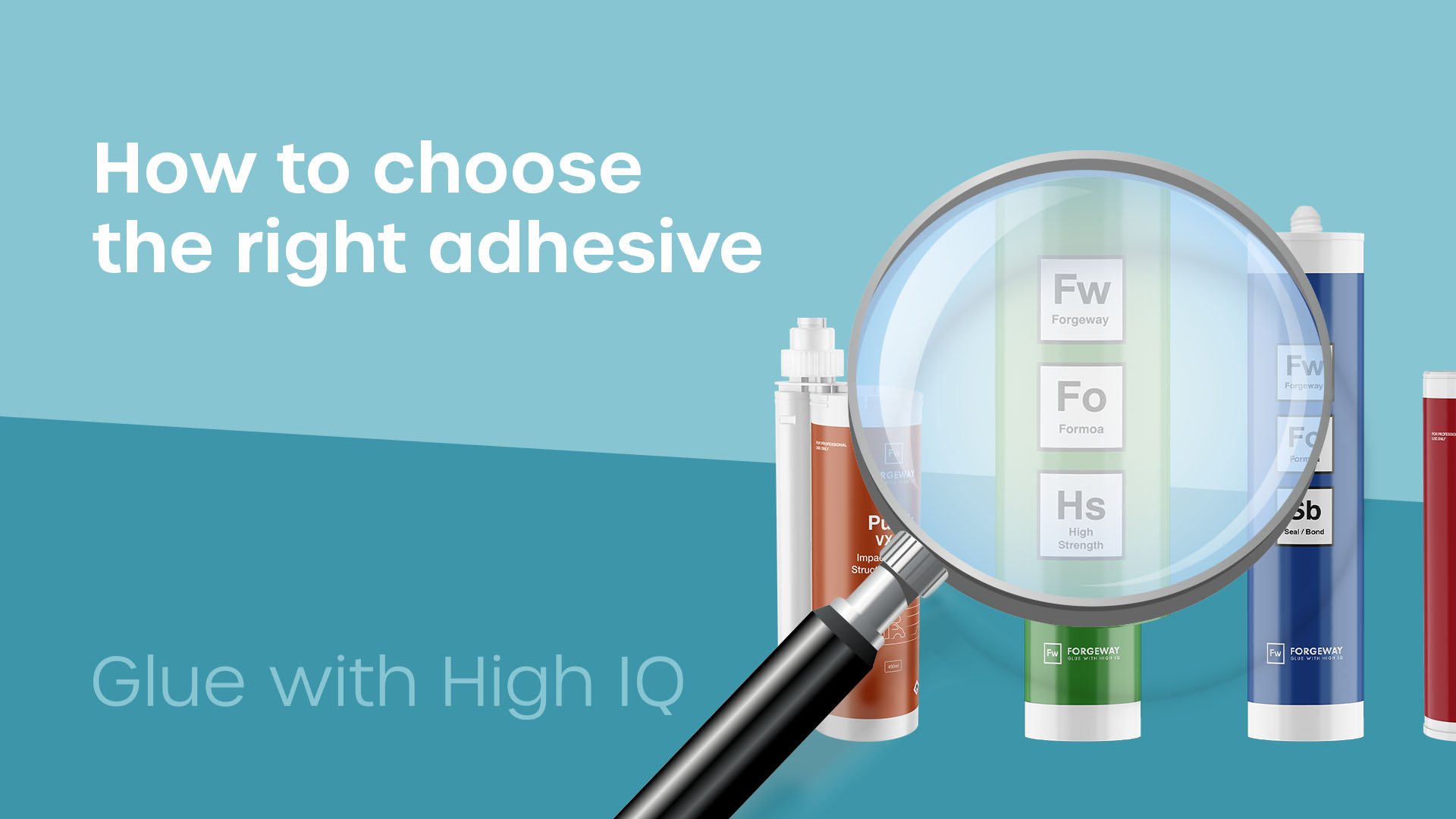
When choosing the right adhesive for your bonding application, it can be difficult to know where to start. Cure time, strength, and flexibility are three main factors that people consider before deciding on an adhesive. But there are so many different factors you need to consider to ensure the adhesive is the right match for your application.
Here at Forgeway, we have helped thousands of companies in a range of different sectors choose the right adhesive for their application. We have been manufacturing adhesives and sealants for over 25 years. Our knowledge of adhesives means we can often help our customers find the best adhesive for their application.
So we wanted to share the four-step process we use to identify which adhesive could be a good fit for your application. By the end of the article, you will know how to choose the right adhesive for your application. The next time it comes to choosing an adhesive, you will be much better prepared when choosing an adhesive.
Alternatively, you may prefer to watch this detailed video which will help you understand this topic in more detail.
Step one – Determine the material(s) you are bonding
Before you do anything else, you need to know what you are bonding. At this point, you need to establish whether the adhesive will stick to all the surfaces in the joint. Most adhesives will bond to dissimilar materials. In fact, that’s what makes adhesives such a popular option over other joining methods.
However, some materials are more difficult to bond than others. Low surface energy (LSE) plastics are typical examples of a substrate that is difficult to bond. If you are bonding LSE plastics, then you will need to use a specialist product or use specialist surface preparation methods.
If you don’t know whether your material will be difficult to bond, you have two options:
- Get in touch with your adhesive supplier and they will be able to guide you on whether the substrate is going to cause any problems.
- Undertake some testing to determine whether your substrate is going to cause problems when it comes to bonding.
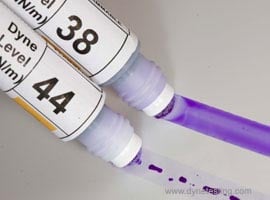
Step two – Find out how much time you have
After you have ensured the adhesive will actually stick the material(s) in the joint, you need to find out how much time you have. This may seem pointless, but it isn’t. Establishing the amount of time you have will play a major factor in which adhesive you choose.
There are two things you need to consider at this stage. How much time you have to put everything in place (open time), and how much time you have before you need to put the structure in use (cure time).
Open time
When applying any adhesive, the liquid state of the adhesive will transform into a solid-state. During this period, the adhesive will form a ‘skin’. Once the adhesive has formed this skin, it will not effectively bond to the surface of the substrate.
The time it takes to reach this state is called ‘open time’ or ‘skin-over time’. If you aren’t able to put the substrate into place quickly, you will want an adhesive with a longer open time. Alternatively, if it doesn’t take a long time to put the substrates in place, you won’t need to worry about the open time.
Read more about adhesive open time here.
Cure time
If you are a large-scale manufacturer, you need the adhesive to form a strong enough bond so that you can move to the next stage of the manufacturing process without damaging the integrity of the structure.
This is known as reaching ‘handling strength’ and is all part of the curing process. An adhesive with a quick cure time can reach handling strength quickly too. This means you can quickly move on to the next stage of your process without having to worry about the bond breaking apart.
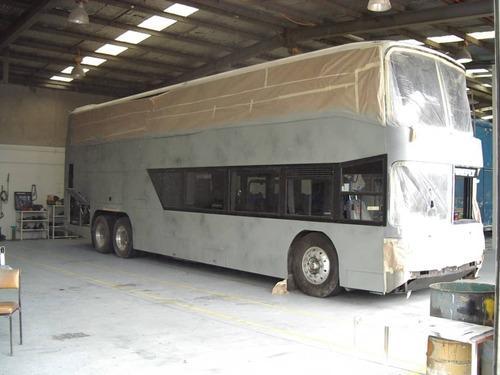
So if you don’t have much time to wait for the adhesive to reach handling strength, you will need an adhesive that has a quick cure speed.
Step three – Define the characteristics you want from the adhesive
So you’ve established what you need from the adhesive in terms of the curing process, but what else do you need to define?
There are several different factors that you need to consider at this point of the selection process:
- Strength: Most people automatically assume strength is the most important thing about an adhesive. However, you will not always need a very high strength adhesive. Ultimately, strength is still one of the most important factors to consider. Epoxies and methyl methacrylate adhesives can achieve the highest strengths.
- Flexibility: Some people argue that flexibility is more important than strength in an adhesive. Whilst the answer remains subjective and dependent on your situation, we would say you need to put strength and flexibility on the same level of importance. Usually, the stronger the adhesive, the less flexible it becomes. You will need a flexible adhesive when the structure you are bonding is likely to move or vibrate. MS polymers and polyurethane adhesives are traditionally the most flexible adhesives. However, you can formulate all adhesives for increased flexibility.
- Viscosity: This term often refers to how thick the adhesive is. Similar terms such as ‘thixotropic’ and ‘grab’ are terms you may hear when discussing the viscosity of an adhesive. Typically, adhesives with high viscosity will be thixotropic and will have a high grab. Thixotropic means it doesn’t run easily. Grab means it can hold the substrates in place without much external help (if any).
- Hardness: The hardness of an adhesive literally refers to how hard it is. A hard adhesive is the opposite of a flexible adhesive. The hardness is rated in terms of shore A hardness from 1-100. In some applications, a harder adhesive means that you can sand it (when joining a solid surface worktop for example). Harder products will also be less likely to stain or pick up dirt.
- Colour: Most of the time, the colour of the adhesive won’t matter as it will be hidden. Sometimes, the adhesive is on show, particularly if you are also using it as a sealant. And in order to maintain aesthetics, getting a colour-matched adhesive is the best option. You just need to ensure your adhesive option can be colour-matched. Most adhesive manufacturers can match (or come very close to) any colour providing the adhesive is colour-matchable. You can easily colour-match methyl methacrylates and MS polymer adhesives.
- UV stability: Sometimes the adhesive is going to be exposed to large amounts of UV radiation. If your adhesive is likely to experience high UV exposure, you will need to ensure it can withstand that exposure. Degradation and yellowing are common amongst sealants, but they can also affect adhesives.
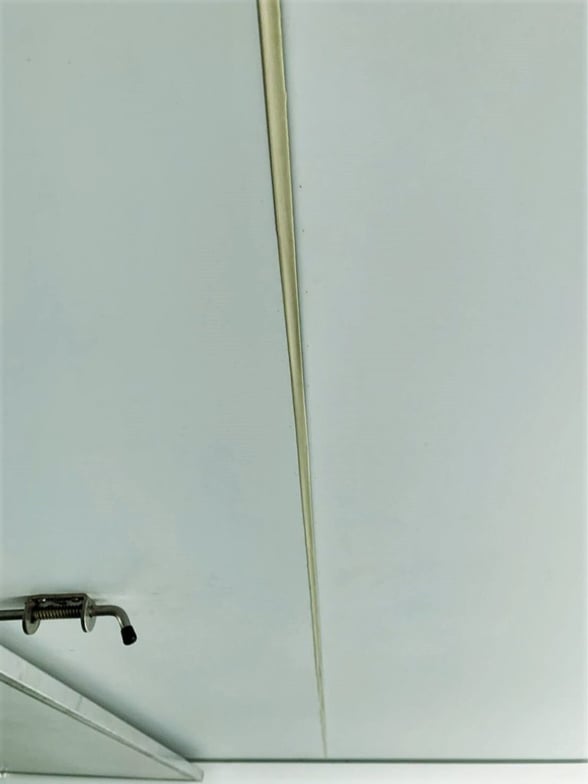
- Potential health risks: Some adhesives contain isocyanates and other harmful chemicals meaning they can pose health risks. Whilst you can manage any health risks, you should be aware of them before you decide on the best adhesive for you. MS polymer adhesives have no health risks associated with them. Epoxies and polyurethane adhesives tend to have more health risks.
- Temperature and chemical resistance: Sometimes, an adhesive will face a lot of exposure to extraordinarily high/low temperatures or chemicals. If you are using an adhesive in an application that would face either (or both) of these conditions, you will need to ensure the adhesive can withstand that exposure.
One important consideration you need to take at this stage is versatility. You may have read through this list and established what is most important to you. But further down the road, you realise that it’s very difficult to find an adhesive that suits all the reqirements you established as important to you.
You don’t need to worry, most adhesive manufacturers can adjust formulations of adhesives to suit your needs. For example, if you want a flexible adhesive that reaches handling strength in half an hour but also doesn’t have any health risks, the adhesive manufacturer will almost always be able to help.
Step four – Determine how much you want to spend
Controversially, we put the cost as the last thing to consider before choosing an adhesive. This is mostly because there are so many things you need to consider when analysing the cost of the adhesive.
Our article on cost covers this topic in much more detail, but in summary, you need to consider the following factors when looking at the price:
- Whether the supplier offers training?
- What technical support the supplier offers?
- What warranty is there?
- Do you need specialist application equipment?
- Do you need health and safety equipment?
- Do you need special waste disposal techniques?
- Does the supplier offer auditing services?
- Are you buying directly from the manufacturer or a third-party?
- What accreditations does the adhesive hold?
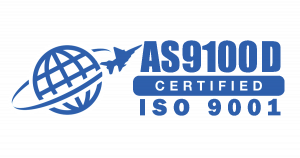
The main reason we put cost as the last step is simple. If you only focus on the cost of the adhesive, you are likely going to just choose an inadequate adhesive. Long-term, that low-cost option will end up costing even more.
So, you must make sure your adhesive option will meet your needs before looking at cost. We know that price is a massive part of any buying decision. But we cannot stress enough the importance of doing your homework, deciding what you need from your adhesive, and choosing the right product for you based on that research.
We know that the long term cost of not doing that homework will be far greater than the cost you save from choosing a cheap adhesive.
Choosing the right adhesive for you
The process of changing adhesive or sealant is incredibly challenging. Usually, companies will not go through this process unless the problem they are facing is greater than the resistance to change.
Making sure this change process was worth the effort is critically important. The last thing you want is to have to go through that change process again.
Here at Forgeway, we manufacture over 3000 tonnes of adhesives every year. We always use a four-step process to significantly reduce the risk of our customers choosing the wrong adhesive.
The four steps above will give you a good indication of what you need to consider when choosing the right adhesive for you. We recommend you read our article on structural adhesives next. It will go through the different types of structural adhesives and help give you an idea of one that could meet your needs.
You can always reach out to a member of our team if you need more help. Our experience and expertise give you the confidence that we know what we are talking about; we want to help you understand what you can do with glue.
Or you can choose the best adhesive all by yourself. Click the button below to take our product selector quiz.
Thomas is the Content Manager here at Forgeway. Thomas' job is to translate the technical jargon from the ivory tower of academia into easy-to-read content that everyone can understand. Forgeway's mission is to answer every question our customers and prospective clients ask, or are apprehensive to ask.