Cyanoacrylate Adhesives: Analysing the Benefits and Drawbacks for Industrial Applications
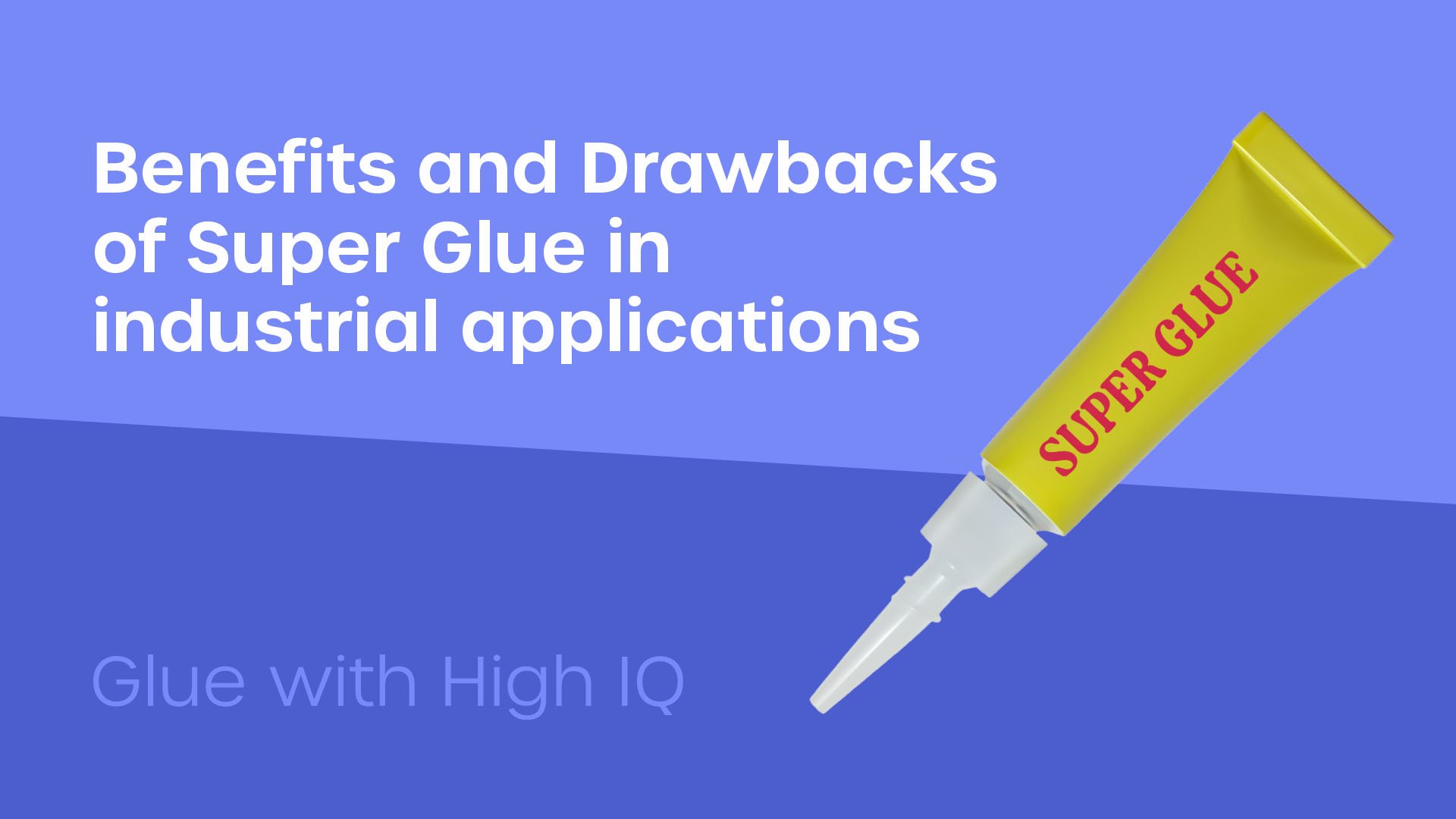
You’ve reached the point where you’re assessing cyanoacrylate (CA) adhesives as a suitable choice for your industrial application. However, It can be difficult to know whether they will be the right fit for you.
Here at Forgeway, we manufacture industrial adhesives. And whilst we don’t manufacture cyanoacrylate adhesives, we’ve worked with them in the past and understand the benefits and drawbacks of this adhesive type. You can tap into our knowledge of adhesives to gain a deeper understanding of the pros and cons of cyanoacrylate adhesives.
This article will go through the benefits and drawbacks of CA adhesives to help you become an expert. By the end of the article, you will understand whether this adhesive type could be the right choice for your industrial application.
What are the benefits of cyanoacrylate adhesives?
There are several benefits that we could touch on. However, the top 5 benefits of cyanoacrylate adhesives are as follows; easy to use, very fast cure time, high strength bonds, bond to a wide variety of materials, and relatively low toxicity.
In this section, we are going to analyse these benefits in more detail.
Cyanoacrylates are easy to use
One of the reasons for Cyanoacrylate’s popularity is the ease of use. The DIY market is one of the largest users of this adhesive type for this reason. There aren’t multiple complicated steps when it comes to using cyanoacrylate adhesives.
The ease of use is mostly because CAs are single-component. Single-component adhesives do not require mixing. You don’t need to worry about correctly mixing the adhesive before use to ensure a strong bond.
You also won’t need to worry about surface preparation. CA adhesives do not need specialist surface preparation to ensure a strong bond.
In most situations, bonding with cyanoacrylate adhesives is as simple as applying the adhesive and putting the substrates in place.
This ease of use can eliminate the need for complex processes in your manufacturing process helping to speed up production and reduce quality issues.
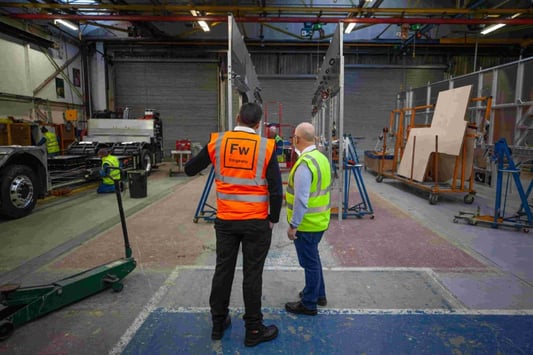
CAs have a very fast cure time
One of the key advantages of cyanoacrylate adhesives is their exceptionally fast cure time. This is because they rapidly polymerize as soon as they come into contact with moisture.
Cyanoacrylate adhesives achieve handling strength within seconds. A full cure can take up to 24 hours. However, after a few seconds the adhesive will be strong enough to put into light operation.
This fast-curing property improves productivity and reduces waiting times in manufacturing processes.
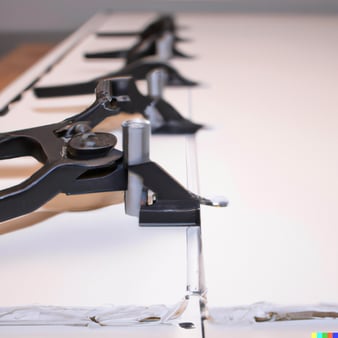
They can achieve high-strength bonds
The rapid polymerization of the curing process also results in high-strength bonds. Some cyanoacrylate adhesives can achieve strengths of more than 20 MPa. If you’re unsure what this means, we can explain.
P.S. The topic of adhesive strength is complicated. We advise reading our article if you want to learn more about this topic.
Let’s put cyanoacrylate’s strength in context. It would often surpass the strength of the materials being joined; resulting in substrate failure.
Some grades of plastic and GRP are examples of materials that would experience failure before the adhesive.
So when using cyanoacrylate adhesives, you usually won’t need to worry about the strength (as long as you get the joint design right).
They can bond to a wide variety of materials
Not only can cyanoacrylate adhesives achieve high-strength bonds, but they can also form strong bonds with a wide variety of materials.
Metals, plastics, rubber, ceramics, and even some porous substrates (like fabrics) are all compatible with CA adhesives.
This versatility allows users to form strong bonds in a wide range of applications.
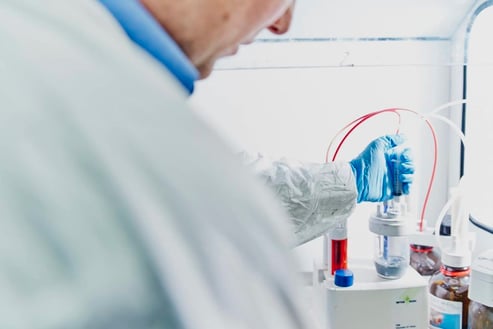
Cyanoacrylates have low toxicity
We aren’t saying that cyanoacrylate adhesives are completely harmless. There are certain situations where CAs have caused harm to users. However, compared to many other adhesive types, they have low toxicity levels.
You won’t need to worry about harmful VOCs or asthma-causing particulates like with some adhesives. Some adhesives are so harmful that restrictions are coming into force about their safe use.
But it isn’t the same with cyanoacrylates. They release minimal fumes during curing and will not cause sensitization in most cases. This makes them safe for users and reduces the need for extensive ventilation or PPE in manufacturing facilities.
This low toxicity is also why they are so popular in the medical industry. CAs can bond small cuts and tears without harming the patient.
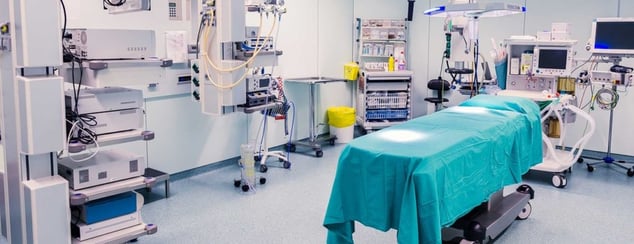
What are the drawbacks of cyanoacrylate adhesives?
Whilst there are plenty of benefits to using cyanoacrylates, there are multiple drawbacks too. Once again, we’ve highlighted the top 5 drawbacks.
The 5 most common drawbacks of cyanoacrylate adhesives are as follows; poor chemical resistance, high cost, poor shelf life, can damage aesthetics, and poor gap-filling capabilities.
This section will go over these drawbacks in more detail.
Cyanoacrylate adhesives have poor resistance to chemicals and impact
One of the most notable drawbacks of cyanoacrylate adhesives is their limited resistance to chemicals and impact. People will often refer to ‘durability’ when discussing chemical and impact resistance.
Whilst strength is one of the benefits we’ve highlighted, durability is one of the biggest drawbacks.
Adhesive durability (like strength) is a complicated topic. We’ve written several articles on this topic which we recommend you read. To summarise, an adhesive’s durability is how long it can maintain the strength advertised.
In this case, cyanoacrylate’s strength can reach 20 MPa (which is comparatively high). However, exposure to chemicals and impact is likely to have a significant effect on that strength.
So, when the cyanoacrylate adhesive faces exposure to chemicals (even salty water) the strength may reduce to the point of bond failure.
The same can occur when facing exposure to impact. Cyanoacrylates produce a high-strength but brittle bond. This brittleness means it will struggle to withstand light impact (like movement or vibration).
Before using cyanoacrylate adhesives for your application, we advise conducting testing to ensure the bond is durable.
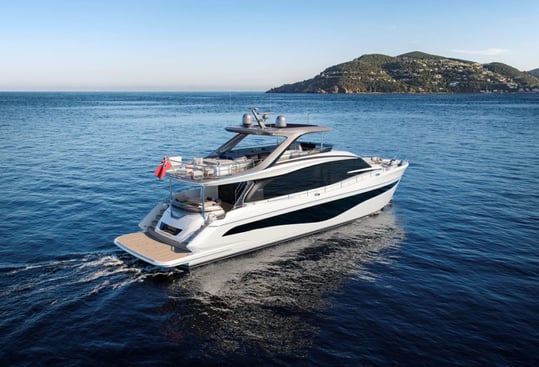
They are often the most expensive adhesive type
Cyanoacrylate adhesives are usually double the price of other single-component adhesives. The specialized formulations and rapid curing properties contribute to their higher price point.
Therefore, it is crucial to evaluate the overall cost of using cyanoacrylate adhesives for your specific application.
If you are using small quantities of cyanoacrylate adhesives (like small component bonding), the cost shouldn’t present too much of an issue. However, if you need an adhesive to cover a large volume, cyanoacrylates will be very costly.
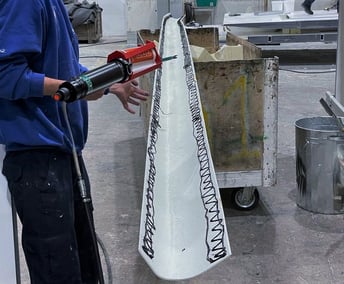
CAs can have a poor shelf life
Cyanoacrylate adhesives have a limited shelf life once the container is opened.
Due to the extremely reactive nature of the cyanoacrylate polymers, even a small amount of moisture will trigger the curing process. Even exposure to a small amount of air initiates the curing process
Proper storage and handling are necessary to maximize the shelf life and prevent premature curing.
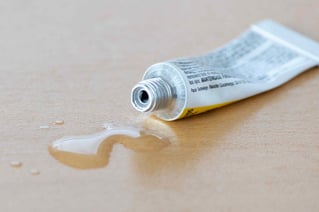
They can impact the aesthetic due to ‘blooming’
When used on certain substrates, cyanoacrylate adhesives can cause a phenomenon known as “blooming” which looks like whitening around the bond area.
You may not understand what we mean so let’s explain ‘blooming’. As we have already mentioned, cyanoacrylate polymers are extremely reactive.
Blooming occurs once you apply the adhesive. Small amounts of the liquid will then vaporize and rise.
The vapour from the liquid will react with the moisture in the air. This forms small crystals that fall back down onto the rest of the adhesive. As the adhesive is still curing, these crystals stick to the surface.
This then causes the white residue you now know is called ‘blooming’.
Blooming may leave an undesirable aesthetic impact in applications where visual appearance is critical.
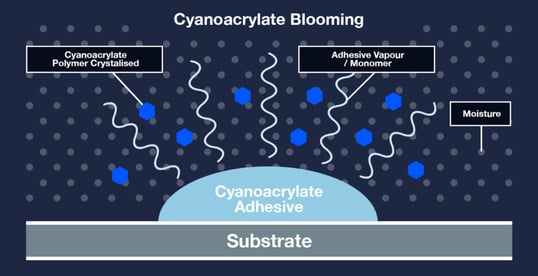
Cyanoacrylate adhesives have poor gap-filling capabilities
As you already know, CA adhesives require moisture to cure. This makes them ideal for thin bond line applications. However, this thin bond-line causes a problem in gap-filling applications.
The adhesive cures so quickly that a thick skin forms on the adhesive surface. This can prevent further moisture from penetrating to the uncured adhesive. The adhesive under the skin will take a lot longer to cure.
In such cases, alternative adhesive types with better gap-filling capabilities may be more appropriate.
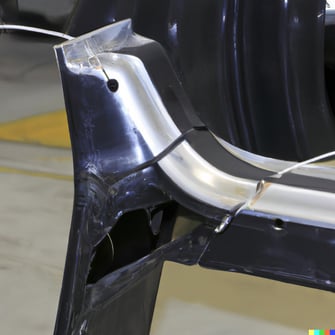
Are cyanoacrylate adhesives the right choice for your industrial application?
Now you understand the benefits and drawbacks of this adhesive type, it should be easier to decide their suitability for your application. It’s not always easy though.
Here at Forgeway, we’ve helped hundreds of companies find the right adhesive for their application. Even though we don’t sell cyanoacrylate adhesives, we’ve recommended them to companies where we believe they are the best fit.
Usually, we would recommend cyanoacrylate adhesives for small component bonding or where an ultra-fast-curing adhesive is required.
But we would never recommend them in situations if you need to bond a large area or use large quantities of adhesive.
If you’re still not sure and would like to speak to someone, you can reach out to a bonding expert. A member of our team will analyse your exact application and recommend the best adhesive.
Or, you can take the 45-second quiz below. After answering a few questions, you will have a recommended adhesive type based on your responses.
Thomas is the Content Manager here at Forgeway. Thomas' job is to translate the technical jargon from the ivory tower of academia into easy-to-read content that everyone can understand. Forgeway's mission is to answer every question our customers and prospective clients ask, or are apprehensive to ask.