Speeding up production; Is a faster-curing adhesive always the best solution?
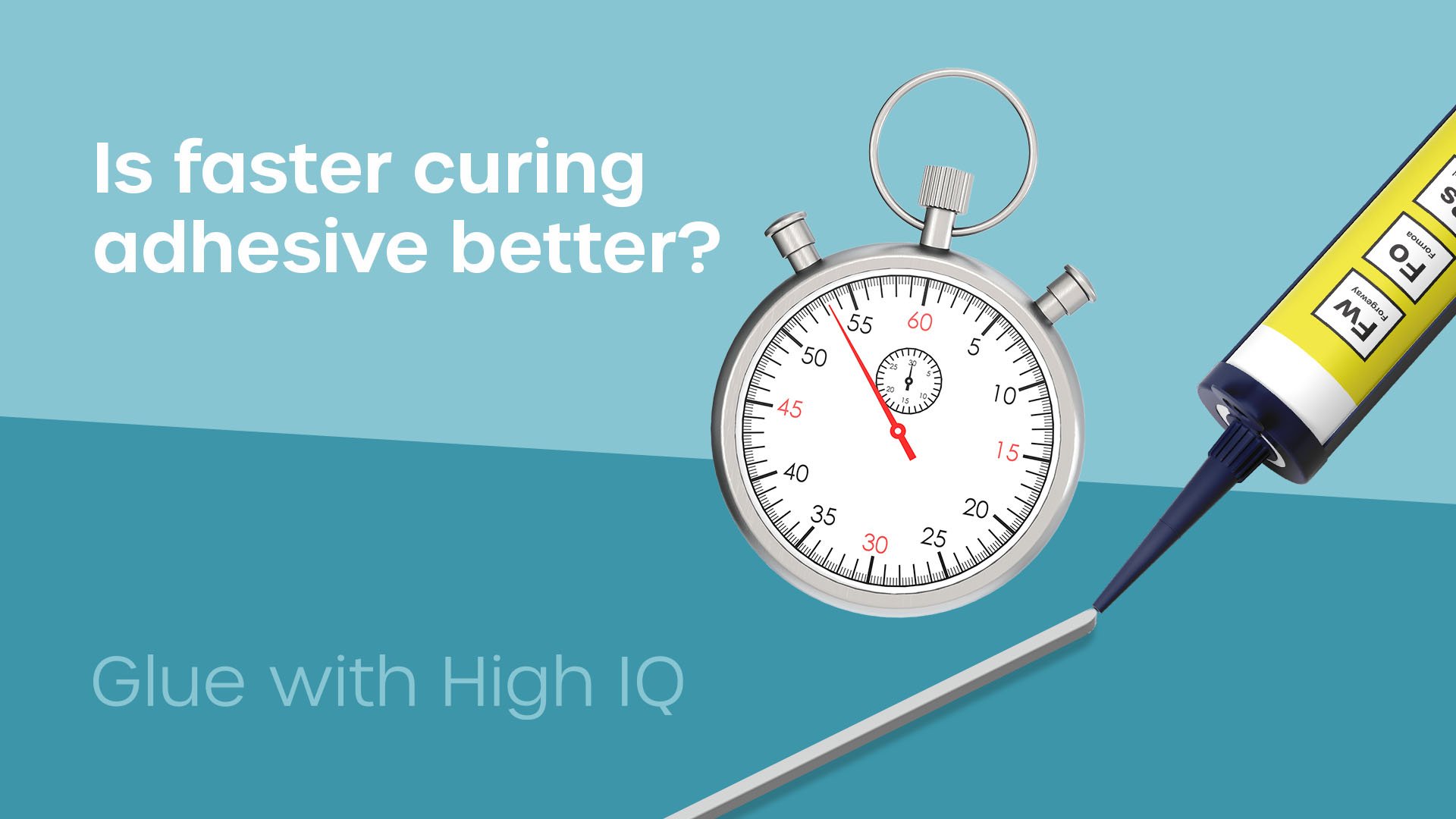
The objective of every company is to make money. At least, it should be. For manufacturing companies, one way to make more money is by making more products. As long as sales are coming in, the faster a company can make their products, the quicker it can make money.
As industrial adhesive manufacturers here at Forgeway, we know this only too well. We understand the principles of manufacturing. A large proportion of our customers are also manufacturers. They use adhesives and bonding in their processes and are constantly looking for ways to speed up production and improve throughput.
That’s why our customers often ask us for a faster-curing adhesive. On paper, it makes sense. A faster curing adhesive means quicker production. And as we know, faster production means more throughput.
But we’ve often seen that this isn’t the case. A faster curing adhesive rarely makes a significant enough difference to throughput figures. In this article, we’ll discuss why that’s often the case. We’ll also discuss what you should consider when speeding up the cure time of an adhesive.
Can a faster-curing adhesive speed up production?
As touched on above, speeding up production means you can make more money. In theory at least. So, can a faster-curing adhesive really speed up production?
The short answer is yes. A faster curing adhesive will help speed up production. But there’s a caveat. The efficiencies of using a faster-curing adhesive will usually not make a significant impact on throughput. Let’s explain why.
To use an example, let’s say you are a bus manufacturer. You’re using an adhesive that takes four hours to reach handling strength. The bus is dormant for four hours while the adhesive builds up enough handling strength. The bus also has multiple bonding stages.
Three of those bonding stages are dependent on each other. This takes the total curing time to 12 hours. So that adhesive is responsible for increasing production time per bus by at least 12 hours.
Now, you have to multiply those 12 hours by the 24 buses produced in a month. It’s no longer 12 hours of waiting for the adhesive to cure, it’s now 12 days worth of waiting in a month.
Therefore it’s simple surely? Find a faster curing adhesive, and throughput will increase dramatically.
Let’s use an example. Say you’ve found an adhesive that reaches handling strength in 30 minutes. It also matches the strength requirements for that application. You’ve just managed to reduce the 12 hours of waiting for curing to just 1.5 hours. Right?
As a result, the efficiency of the bonding process increases by 800%. In theory, that will increase throughput significantly. That’s not marginal. That’s monumental!
But, hold on. It’s not that simple. It never is. As we’ve found over the years, the adhesive bonding process is rarely the bottleneck in production. In the case of this bus manufacturer, the bonding process was not the bottleneck.
The true bottleneck in their production was the painting process. Only one bus can go through the painting process at a time. The entire painting process takes around 24 hours.
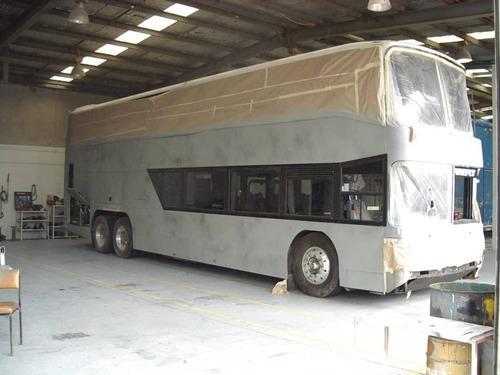
And as this bus manufacturer found, increasing the cure speed of the adhesive did very little to improve the overall throughput of their production. It only caused a hold-up in the painting process.
You might say that this example is a one-off. But we’ve seen the same thing happen in industrial manufacturers from various industries.
That’s why we say that a faster-curing adhesive will rarely help you increase production speed. You have to look at the real bottleneck in your production. You should only look at implementing a faster-curing adhesive if you can prove that it will make a significant impact on your throughput.
If you can’t prove the impact, we would recommend not exploring faster-curing alternatives. We’ve often had to help customers navigate through the unexpected side effects that come with fast-curing adhesives.
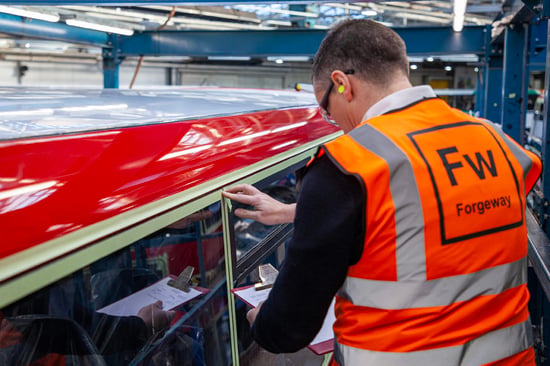
Can you speed up the cure without changing adhesive?
So you think you’re going to benefit from faster curing? Hold up. Before you get too far into researching an alternative adhesive, there may be ways you can speed up the cure of your existing adhesive product. This will depend on what type of adhesive you’re using, however.
One-component and two-component adhesives are very different. They also cure differently. A two-component (2K) adhesive will cure by mixing the two components together. This then triggers a chemical reaction to start the curing process. It’s often difficult to adjust the cure speed of a 2K adhesive without changing the base formulation which is costly, time-consuming, and will change its characteristics.
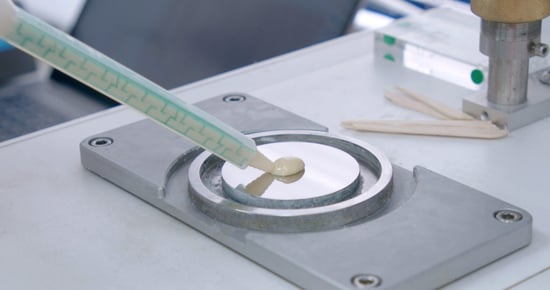
Let’s use moisture-curing adhesives as an example.
A one-component (1K) adhesive is different. It will cure via an external trigger like heat, UV, or moisture. As soon as the adhesive comes into contact with that external trigger, the curing process will start. If you’re using a 1K adhesive, it is often simple to increase the cure speed.
Adhesives that cure with moisture are very common. The super glue (aka cyanoacrylate) you use for DIY repair jobs uses moisture to cure. The atmospheric moisture all around us in the air is enough to trigger the chemical reaction that will start the curing process.
It’s not just cyanoacrylates that are moisture-curing. 1K MS polymer adhesives, silicone adhesives, and 1K polyurethane adhesives are other common examples of moisture-curing systems.
Simply increasing the amount of moisture available to these types of adhesives will increase the cure speed. You can do this by applying water spray, increasing the humidity, and removing the spew.
Although sometimes marginal, these methods will increase the cure speed. Other methods like warming the substrates and surrounding environment can increase adhesive cure speed.
When speeding up the cure, just make sure that operators put the substrates in place before the adhesive skins over. Speeding up the cure will also decrease the working time of an adhesive.
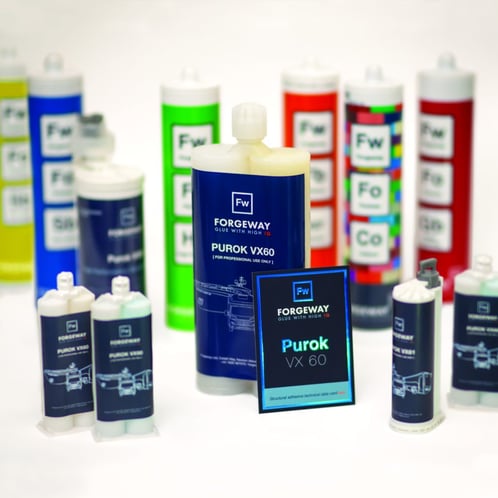
Be aware of the side effects of changing to a faster-curing adhesive
You’ve analysed your production and have worked out that a faster-curing adhesive will improve throughput. Now you can start looking for an alternative adhesive that cures faster.
But this is where it gets challenging. There are several things you need to consider when analysing a faster-curing adhesive solution.
Faster-curing adhesives can impact adhesive performance
One of the main considerations when assessing faster curing adhesives is the potential impact on adhesion. Faster curing often means there is limited time for the adhesive to interact and establish strong bonds with the substrate
Consequently, this can compromise the strength of the adhesion. Which can then lead to reduced performance and even bond failure.
That’s not all. The speed at which an adhesive cures can also affect the structure of its polymer chains. Faster curing processes tend to result in more linear polymer chains with limited crosslinking. This basically means that whilst you get improved cure speed, you’ll have to sacrifice an adhesive’s other characteristics.
This is because crosslinking is what determines an adhesive’s characteristics, such as flexibility and rigidity. In general, slower-curing adhesives are likely to provide stronger and more rigid bonds.
Cure speed not only affects adhesion but can also affect the characteristics of the adhesive. It’s important to make sure the adhesive still performs to the necessary requirements before using it in your application.
A fast-curing but incompetent adhesive is only going to slow production even further. First make sure the adhesive sticks. Then make sure it stays stuck.
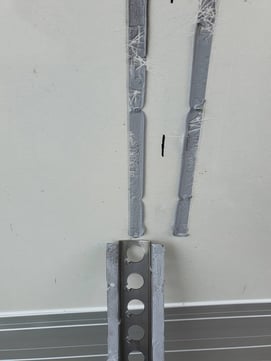
Faster-curing adhesives usually generate heat when curing
Increased curing speed often generates more heat during the curing process. This temperature increase can have several negative implications. However, you need to be aware of two possible outcomes in particular.
Firstly, the increased heat can make the adhesive inadequate. If you need the adhesive to gap-fill and need to apply a large volume in a gap, the large mass of adhesive can generate enough heat to evaporate some of its important ingredients. As a result, this impacts the adhesive’s performance.
Additionally, excessive heat can cause substrate damage. In some cases, we’ve seen the adhesive melt the surface. The heat generated during fast curing can also result in shrinkage. This leads to aesthetic issues like witnessing or uneven bonding.
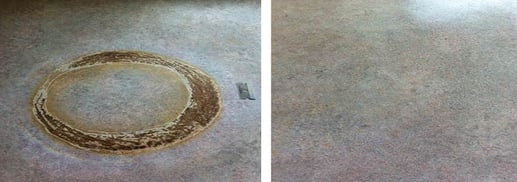
A fast cure means a significantly reduced working time
A critical factor to evaluate when considering faster curing adhesives is the available working time. The faster cure time will leave less time to put the substrates in place before it starts to cure. This is a problem.
In fact, less time can lead to several problems:
- You don’t have much time to ensure all substrates are in the right place.
- If you’re using an adhesive sealant, it can lead to a poor quality finish from the sealant ‘skinning’ over.
- Operatives are in a rush to put the substrates in place often leading to errors and not following SOPs.
- A fast-curing adhesive will often mean increased costs through additional nozzles and specialist cartridges
- A fast-curing product is often affected by ambient temperature
Just remember that a faster-curing solution will also affect the working time. If you have a large area to bond, a fast cure will likely present challenges.
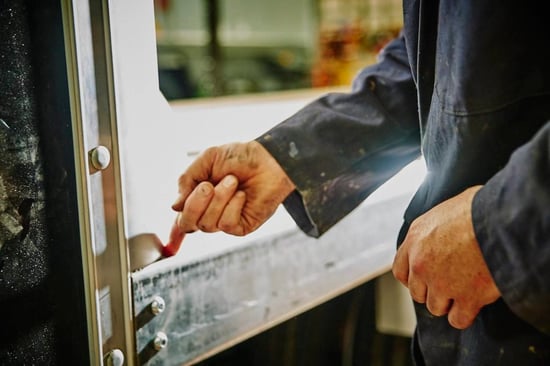
You should look at other adhesive characteristics aside from cure speed
So now you know that faster-curing adhesive isn’t always the perfect solution to improving throughput. Yes, it can improve throughput. But only in the right circumstances.
As adhesive manufacturers, we often get questions about fast-curing adhesive solutions. But we often ask a few questions back to determine if the company has done the research.
Do they really need a faster-curing adhesive? Will the faster-curing adhesive really improve throughput? Is the profit going to increase due to using a faster-curing adhesive?
Often, the answer is no.
If these aren’t the objectives of the company, we will happily help them find a speedy solution.
However, we often find it isn’t the case. The company is much better-off assessing other characteristics before analysing cure speed.
Characteristics like operator safety, ease of use, and long term reliability are more likely to improve your profitability in the long run. Don’t get short-sighted. Assess the bigger picture. Ask yourself; Do you need a faster-curing adhesive?
Take the quiz below to find the perfect adhesive match for your needs. In just 45 seconds, you’ll receive a suggestion based on your answers.
Thomas is the Content Manager here at Forgeway. Thomas' job is to translate the technical jargon from the ivory tower of academia into easy-to-read content that everyone can understand. Forgeway's mission is to answer every question our customers and prospective clients ask, or are apprehensive to ask.